Application of prescribed standards and guidelines for cleanrooms can enhance the quality quotient in manufacturing facilities.
Hina Gupta,Operations Head,MG Cooling Solutions
A Cleanroom is a controlled environment with a low level of contaminants and pollutants such as dust, airborne microbes, aerosol particles, and chemical vapours. Cleanrooms typically are used in any kind of manufacturing like pharma, electrical, semiconductor industry as small particles can adversely affect the manufacturing process. Other than that, cleanrooms are also used in critical process manufacturing common in aerospace, optics, military.
These have controlled settings that incorporates low level pollutants like dirt, microbes, mobile microbes, aerosol particles, vapours, chemical remains in any particle or on a metal surface. A cleanroom is any given contained space where provisions are made to reduce particulate contamination and control other environmental parameters such as temperature, humidity, and pressure.
Since there is a high level of cleanliness required for any kind of manufacturing facility, it becomes imperative for the any kind of manufacturing industry to maintain high Cleanroom standards to sustain quality with no cross-contamination which can be achieved through some of the factors mentioned below:
Cleanroom clothing
All the people who work in the cleanroom must wear cleanroom clothing to make sure there is no contamination from usual clothes as they release particles or fibres which spread contamination of the environment by personnel. Otherwise, it can cause cross-infection during the manufacturing process inside the manufacturing facility.
Cleanroom garments include boots, shoes, aprons, beard covers, bouffant caps, face masks, lab coats, gowns, glove, and shoe covers. Though this looks like a big list the type of cleanroom garments used depends upon the cleanroom and its specifications. More is the requirement of stringent conditions in the cleanroom, more the person needs to go for cleanroom clothing. A cleanroom suit is usually required for entering a cleanroom. For example, a class 10,000 cleanrooms may use simple smocks, head covers, and booties, but a stringent class 10 cleanrooms, careful gown wearing procedures with a zipped coverall, boots, gloves, and complete respirator enclosure are required.
The internal surface
It refers to inside walls, flooring ceiling and other associated things. Compliances used for manufacturing like GMP (Good Manufacturing Practices) states that to achieve the cleanliness specification, all inside surfaces in a cleanroom should be impervious and smooth. The internal surface should not generate any kind of their contamination like dust, peel, flake, rust or corrosion. Also, the surface should not provide a breeding ground for micro organism to flourish. The surface should be easy to clean and should not crack, shatter or dent easily.
Cleanroom airflow
The cleanroom needs a lot of fresh air at a particular temperature and humidity and as a direct rule, more the cleanliness of the room more air it will require. It maintains particulate-free air either through HEPA filters or ULPA filters, using the stratified or turbulent airflow principles.
The HVAC system itself is responsible to consume 60 percent of the power in the cleanroom. Hence, to reduce the energy costs, AHUs and HVAC systems are designed to recirculate (if product characteristics or process permit) about 80 percent air through the room, removing particulate contamination as soon as it is generated and keeping the temperature and humidity stable.
However, a well-designed HVAC system should deliver both “fresh” and “recirculated” filtered clean air. The reason is that recirculated air will not bring in any oxygen for the working personnel which is only possible with the entry of fresh air. Also, the contaminants, particulate materials, moisture, noxious vapours or gases from processes, raw materials or products cannot be recirculated; and hence they get exhausted out of the cleanroom and is further replaced by 100 percent fresh air.
A good HVAC system makes sure that air is kept moving throughout the cleanroom.
Operation and maintenance of cleanrooms
Since there is a lot of expenditure required to construct a cleanroom, it becomes imperative to maintain it. Even the operating personnel must be trained before giving access to the cleanroom.
The facility department must clean the facility to strictly controlled procedures with regular maintenance of the facility and equipment. Since filters are at the core of any cleanroom regular monitoring of the air filters and air flows must be done by qualified HVAC personnel.
Air change rate
This refers to the number of times the air is changed within a cleanroom and calculated by taking the total volume of air introduced into the cleanroom and dividing it by the volume of the room over an hour and expressed as air changes per hour (ACH) and for cleanrooms, this is normally between 20 and 40 air changes per hour.
HEPA filters
Since filtration is at the core of any cleanroom, this filtration is achieved by High-Efficiency Particulate Air (HEPA) filter that is used to trap particles and Ultra Low Particulate Air (ULPA) filters are used. HEPA filters consist of a large, box-shaped filter that removes airborne particles of specific sizes very efficiently. Hence, they must be monitored, cleaned and tested regularly to make sure they are active.
Going by the above, it is essential to follow the cleanroom standards during the initial or construction phase. This can be done by hiring cleanroom consultants or HVAC consultants which are well versed with the cleanroom standards. By maintaining the standards of cleanrooms one cam maintains the quality quotient high as it is crucial for any kind of manufacturing facilities.
Cookie Consent
We use cookies to personalize your experience. By continuing to visit this website you agree to our Terms & Conditions, Privacy Policy and Cookie Policy.
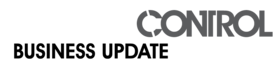