Refrigeration and automation technologies are revolutionising the dairy industry, enhancing product quality, reducing environmental impact, and minimising waste. Madhur Sehgal, Head of Climate Solutions, Danfoss India, explores the technologies’ role in dairy processing and how they contribute to a more sustainable and efficient future.
How does refrigeration technology contribute to the freshness of dairy products throughout production and distribution?
Refrigeration technology is integral to maintaining the freshness of dairy products throughout production and distribution. It achieves this by creating and sustaining temperatures lower than the surrounding environment, effectively cooling to inhibit the growth of bacteria and achieving low bacterial levels in milk and its derivatives.
This is mostly done using ‘vapour compression refrigeration’ where devices like compressors, condensers, and evaporators are used to create a cooling effect. From the moment milk is collected from the farms, it must be cooled within three to four hours to prevent spoilage. This is where refrigeration comes in. Refrigerated bulk tanks and dedicated refrigeration units help rapidly cool fresh milk to around 4°C, maintaining its freshness and nutritional value.
Throughout the distribution process of dairy products, refrigeration is the key factor in upholding the right temperature levels, guaranteeing that these products are delivered to retailers and consumers without compromising their safety, quality, and freshness. Danfoss India enhances high-pressure applications by incorporating sight glasses, supplying refrigeration compressors that deliver a 20 percent increase in efficiency compared to traditional technologies. It employs check valves to regulate the unidirectional flow of refrigerants, thereby ensuring the preservation of product freshness throughout the entire supply chain.
How do refrigeration systems help achieve temperature and humidity control parameters in dairy processing facilities?
Refrigeration systems are vital components in dairy processing facilities, crucial in regulating temperature and humidity. These systems are essential for maintaining specific temperature and humidity conditions throughout the dairy product processing chain, ensuring the preservation of product quality. They are indispensable at various stages, including the cooling and storage of milk, the production of items like butter and ice cream, and the facilitation of low-temperature transportation and distribution. By sustaining the necessary temperature and humidity levels, these systems ensure dairy products’ quality, safety, and shelf life. Danfoss India offers solutions that include semi-welded plate heat exchangers for efficient heat transfer and stable temperatures, differential pressure controllers to eliminate pressure fluctuations, and control valves for precise temperature control, even at low flow rates.
Please discuss how refrigeration and allied technologies are being optimised to reduce environmental impact in dairy processing.
In response to environmental implications, refrigeration technologies are now optimised for energy efficiency and environmentally friendly refrigerants. Modern refrigeration systems are becoming increasingly efficient, reducing energy consumption by up to 20 percent when compared to older models. Adopting natural refrigerants such as CO2 and ammonia, which have no Ozone Depletion Potential (ODP) and low Global Warming Potential (GWP), significantly decreases air pollution. Furthermore, heat recovery units capture and repurpose waste heat generated by refrigeration systems to heat water within facilities, contributing to further energy savings.
Nowadays, refrigeration technologies are being engineered to minimise environmental impact, focusing on energy efficiency and adopting eco-friendly refrigerants. Advanced systems featuring automated power and process controls help to minimise energy usage, thus reducing greenhouse gas emissions. Danfoss India is committed to reducing its environmental footprint across all its operations, including dairy processing. Their variable frequency drives (VFDs) facilitate capacity modulation under varying load conditions, resulting in substantial energy conservation. Danfoss also employs smart purging systems to efficiently remove non-condensable gases, maintaining the optimal performance of refrigeration systems. They prioritise using natural refrigerants like CO2 and ammonia, which have a low global warming potential.
What refrigeration technologies are used in the dairy industry to preserve milk and dairy products?
A wide array of refrigeration technologies is employed to preserve the freshness of milk and dairy products. These solutions encompass basic cooling methods and intricate vapour compression refrigeration systems. Vapour compression refrigeration systems are the most prevalent choice for preserving milk and dairy items in the dairy industry. These systems transform a refrigerant from a low-pressure gas to a high-pressure liquid, producing the necessary cooling effect to protect dairy products. There are various types of refrigeration systems depending on the dairy plant’s size, design, and application. Danfoss India offers control and regulation valves that help maintain extremely low refrigerant temperatures, essential for rapid and uniform ice formation to handle peak demands. Their thermostatic expansion valves are responsible for controlling the injection of liquid refrigerant into evaporators, ensuring precise operation and an extended service life for the refrigeration system.
With the increasing focus on reducing food waste, how does refrigeration technology contribute to minimising product losses in the dairy industry?
Refrigeration technology plays a vital role in the dairy industry by effectively reducing product losses. It achieves this by slowing down bacterial growth, ensuring dairy products’ quality and safety, and decreasing spoilage and wastage. Moreover, maintaining the correct temperature throughout the entire supply chain extends the shelf life of dairy products, guaranteeing the delivery of fresh and safe dairy to consumers, which in turn minimises waste.
Through the provision of continuous and controlled cooling, refrigeration technology significantly decreases the vulnerability of dairy products to spoilage, leading to a reduction in product losses. Rapid and efficient cooling immediately after production and maintaining precise temperatures during transportation prevent bacterial growth, thus increasing the longevity of dairy products and reducing waste. Danfoss India’s refrigeration solutions, such as their pre-cooling stages, enhance product freshness by ensuring accurate temperature control, thereby reducing wastage.
How do dairy producers ensure uninterrupted refrigeration and cold chain management to prevent spoilage?
Dairy producers ensure the uninterrupted operation of refrigeration. They also manage the cold chain by employing advanced and dependable refrigeration systems, conducting regular maintenance, and having backup power sources. This comprehensive approach involves regular system inspections, prompt repairs, the regular cleaning of coils, periodic recharging, and checks for refrigerant leaks. Many dairy producers also have contingency refrigeration capabilities and backup generators to safeguard against spoilage in power outages or equipment malfunctions. They meticulously oversee the entire process, from production to transportation to final storage, to maintain optimal temperatures and prevent spoilage. Danfoss safety relief valve can be used in CO2 applications on low-pressure and low-charge ammonia systems.
Can you explain the role of automation and AI in modern dairy processing plants and how they transform the industry?
The modern dairy processing industry is transforming with the integration of automation and AI, particularly in managing processes like refrigeration. AI-powered software can continuously monitor crucial parameters such as temperature and humidity, making real-time adjustments to enhance productivity, efficiency, and safety. Automation plays a pivotal role in reducing the likelihood of human errors and increasing efficiency in various phases, including production, packaging, and distribution. It also allows for on-the-fly adaptations to refrigeration systems in response to changing requirements, ultimately improving energy efficiency. AI and automation are harnessed for various tasks, from automating repetitive procedures and overseeing refrigeration systems to utilising data analysis for predictive maintenance and process optimisation. This technological evolution streamlines the dairy industry, making it more efficient, consistent, and environmentally friendly.
Danfoss India has worked on implementing state-of-the-art technology in dairy plants to lower ownership costs and enhance refrigeration operations’ environmental impact. This has been achieved through an ongoing innovation process in areas like pre-cooling facilities, cold storage, dairy processing plants, logistics for refrigeration, and supermarkets. Danfoss India’s commitment to integrating AI and automation into dairy processing plants goes beyond improving sector efficiency. It also paves the way for a greener, more sustainable, and economically viable future. This encapsulates their core ethos, i.e., the fundamental philosophy – leading the transformation towards greener industries.
Cookie Consent
We use cookies to personalize your experience. By continuing to visit this website you agree to our Terms & Conditions, Privacy Policy and Cookie Policy.
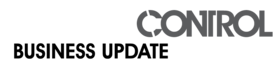