The production and availability of energy is not only fundamental for any country’s economy and for the health of the population, but is also a global environmental issue.
Refrigeration is vital for food preservation and economic development, as well as for medical and scientific progress, but it is a major energy user. The estimate from the International Institute of Refrigeration is that the sector (including air conditioning) consumes about 17 percent of the overall electricity used worldwide. The good news is that refrigeration is a highly technological sector and energy efficiency is among the top priorities in the constant quest for this industry’s evolution and innovation. When talking about evolution, we may say that one of the biggest technology drivers of the last two decades in the refrigeration sector are the variable speed compressors (also known as inverters or VCC), especially because of their energy efficiency. Inverter compressors are already mainstream in air conditioning and household refrigeration applications in many parts of the world, including India, and are gaining increased momentum in the commercial refrigeration industry worldwide. It is just a matter of time before it proves its advantages to Indian commercial refrigeration equipment manufacturers as well. In comparison with a fixed speed compressor, a variable speed has a different type of motor, the BLDC (brushless direct current) motor, also known as ECM (electronically commutated motor). Another difference is that this motor works connected with an electronic device named inverter. The inverter controls the motor, making it rotate at different speeds, according to the targeted cooling load, decreasing it when the ideal temperature has been achieved and increasing it when there is need for more heat removal. Thanks to these characteristics, variable speed compressors have significant advantages over the fixed speed ones, which are the traditional compressor’s technology, also known as on-off. Here, we list these advantages in the perspective that matters the most: the end users. Energy saving: A traditional fixed speed (on-off) compressor operates at a constant speed, continuously switching on and off to meet the refrigeration equipment’s cooling demand. This operational pattern requires abrupt power loads when starting; furthermore, as the compressor maintains the maximum speed for all the running period independent from the thermal load, it leads to wasted energy.
As described previously, variable speed compressors come with an embedded set of electronics that allow the compressor to control its working speed, decreasing it when reaching the target temperature and also increasing it when there is need for more heat removal, ideally without switching on and off (or with a consistent reduction of on-off cycles and with a limited starting torque power versus on-off compressors). This enables the compressor to use only the amount of energy required at each moment and nothing more. The energy saving from variable speed varies according to the application, but it is always significant. We have made many case studies with Embraco compressors where the only change made was the switch from a fixed to a variable speed compressor, and the results were energy savings of at least 15 per cent up to around 40 per cent. Just to give an example, in a horizontal island freezer with optimised performance (using an on-off high efficiency R290 compressor), the energy consumption reduction was 38 per cent, in an ambient temperature of 25°C, when using an Embraco variable speed compressor with Smart Drop in (SDI) control logic, without any other system optimisation (graphic below).
Wide voltage feature: Furthermore, the variable speed compressor has a very good behaviour in severe voltage fluctuations, because it can rotate in very low and very high voltages. This characteristic makes this kind of compressor highly reliable. In many countries, it is normal that the voltage drops down way below the nominal standard voltage. If you have an on-off standard compressor, it may not even start in a low voltage situation. But, a variable speed does, keeping the system performing in this condition without the need of voltage stabilisers or protector switches. It protects the end user from the loss of the refrigerated cargo, which can be high value products such as ice cream or frozen food.
Quicker recovery of the heat load: VCCs recover from door openings much faster. By overdriving to higher RPMS (revolutions per minute) these compressors are able to quickly regulate the delta between product and ambient temperatures. It has a quicker average pull down time, which is the time required to bring down the temperature of the product, from its temperature at the time of entry (in the refrigerator’s cabinet) to the final desired temperature. Tests with VSCs have shown a 20 per cent average pulldown time reduction compared to the on-off ones. These working modes also contribute to the energy saving versus the fixed speed compressors: the VCC reaches rapidly the stabilised conditions, in which it runs at a low (energy saving) speed.
Low noise and vibration: Variable speed technology allows the applications to also generate less noise due to the fact that it operates at lower rotation speeds for longer periods than the fixed speed. In addition, there is the “soft start” characteristic, which means the compressor starts at a lower speed, ramps up to full speed within a few minutes and continually adjusts current to provide needed power depending on the system’s conditions, with less vibration and noise. But it is important to say that at speeds over 3,000 RPM, the VCC noise is equivalent to an on-off compressor’s noise.
Life cycle: Because of the way a variable speed compressor works, controlling its rotation speed according to the condition and the temperature needed, with long running times at low speeds, its expected life will be inherently longer in comparison with a fixed speed one. Another behaviour that contributes to that is the fact that the variable speed compressor doesn’t turn on abruptly each time the temperature rises, because normally it is already on, just at a low speed, and it has the inverter controls to allow a soft start when it is needed. This also avoids the motor’s stress and preserves its functioning.
Space efficiency: VCCs are not only energy efficient, they are space efficient too. because you can produce a smaller variable speed compressor to do the same job of a bigger fixed speed one. During the design phase of an on-off it is necessary to project its size to withstand the highest cooling capacity peak, since it will always operate at full speed. Whereas in a variable speed, the size can be designed for the average speed that it will have for the most part of the time, which will be a lower speed. By freeing up more merchandising space in commercial cabinets without changing any external dimensions, manufacturers can more creatively design equipment and provide more flexible layout options to stores.
Energy regulations and technology dissemination: Despite the fact that the variable speed compressors’ advantages highlighted here have a higher impact on commercial refrigeration than in residential, the adoption of variable speed in domestic refrigeration has been high in many countries because of stringent energy consumption regulations-one example is Europe. Energy consumption regulations tend to target residential appliances first, because of their massive use.
At Nidec Global Appliance, holder of the Embraco brand, we perceive that in commercial refrigeration the key obstacles for the wider adoption of variable speed compressors are: their benefits should be better disseminated, their price is higher than the fixed speed compressor, and for many years there was the need for an additional control unit to regulate the compressors working parameters, which made the whole system more expensive. But all that is changing. Because of the evolution in the compressor’s technology and in its embedded electronics, the price difference of variable speed versus on-off compressors has diminished and made VSCs more Furthermore, taking into account the energy bill savings, the investment has a fast payback (even six months in some applications for retailers). In regard to the necessity of a control unit, that is not true anymore. There are solutions available in the market that eliminate the need for an additional control unit.
Embraco is one example with its variable speed and Smart Drop In logic, that has more intelligence inside the inverter. In this new moment in the global economy, when saving energy is an economical and environmental concern, we are seeing an intense movement towards variable speed in commercial refrigeration. The energy efficiency of an equipment is becoming a relevant decision-making criterion, side by side with reliability and technology that delivers both benefits is becoming increasingly more affordable. This write-up includes contributions of contributions of Marino Bassi, Peter Buksar, Daniel Hofmann, John Prall and Daniel Hense, all from Nidec Global Appliance. Since 1971, Embraco has been a global provider of refrigeration technology for the complete domestic and commercial cold chain, counting on a broad, efficient and competitive portfolio for household, food service, food retail, merchandisers and special applications. As part of Nidec Global Appliance, a division of Nidec Corporation, its solutions are differentiated by innovation that exceeds customer’s most challenging expectations. Further information: www.embraco.com.
With over 15,000 employees across 9 countries, Nidec Global Appliance manufactures and commercialises products for home and commercial applications, including refrigeration solutions, motors for washing machines, dryers and dishwashers, as well as components for heating, ventilation and air-conditioning systems (HVAC). Its focus is to deliver a complete and innovative portfolio with high standards of quality, reliability, competitiveness and energy efficiency. Nidec Global Appliance is a division of Nidec Corporation, a global leader in motors and components for a wide variety of industries, with headquarters in Japan. For further information, access the company profile. (This case study was jointly authored by – Esequias Pereira, Sales and Marketing Director at Nidec Global Appliance, and Renato Gava, Sales Manager at Nidec Global Appliance, where they represent Embraco refrigeration solutions portfolio for the Asia Pacific region).
Cookie Consent
We use cookies to personalize your experience. By continuing to visit this website you agree to our Terms & Conditions, Privacy Policy and Cookie Policy.
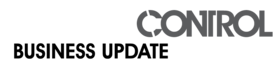