Low-cost fillers as additives in storage media in thermal storage systems can replace expensive high-temperature storage media.
Many industrial processes produce waste heat that is often released unused into the environment. With rising energy prices, waste heat recovery and storage are becoming increasingly attractive for companies as a substitute for fossil fuels.
Analysis
In the Fenopthes project, the Fraunhofer Institute for Solar Energy Systems ISE worked with industrial partners to develop and optimise low-cost fillers for thermal storage systems. Fillers as additives in storage media in thermal storage systems can replace expensive high-temperature storage media. The new technology was tested in a storage unit for waste heat utilisation in an industrial company.
Thermal oils and molten salts are typical working fluids in high-temperature storage systems operating between 250°C and 600°C. To reduce the amount of these expensive storage fluids in thermal storage systems, filler materials can be used. Other low-cost gaseous working fluids, such as air, can also be utilised, allowing temperatures up to 1000°C and more. Air has a very low heat capacity. Therefore, the thermal energy is stored in the filler material when used as a heat transfer fluid.
Project manager, Julius Weiss from Fraunhofer ISE explains, “In the Fenopthes project, we investigated the ideal shape, size and properties, e.g., density and thermal conductivity, of the filler material. The objectives were to achieve the maximum possible heat transfer and the most compact packing for the storage unit.”
Ceramic materials developed by the industrial partner Kraftblock GmbH were investigated in the project. They consist of a low-cost recycled material, phosphate binders and additives. Replacing expensive fluids with filler material having the same or even higher thermal capacity results in a cost savings potential of around 30 percent.
The filler material was manufactured in different shapes so that the influence of the geometry on the thermal efficiency of the accumulator could be investigated. First, the compatibility of the filler material with different high-temperature media (thermal oils, molten salt) was investigated using ageing tests. Subsequently, chemical analyses of the fillers and fluids were carried out, as well as a test on the mechanical stability of the fillers. In parallel, the different filler configurations were characterised initially with water, which behaves physically like molten salt under certain boundary conditions. The project team observed that different filler configurations show different temperature profiles and time histories during cyclic charging and discharging of the storage reservoir. A selected packing configuration was additionally analysed experimentally in a molten salt tank at Fraunhofer ISE.
Demonstration of high-temperature storage in an industrial plant
A real-life application in an industrial company shows that storage technology can improve the energy efficiency of industrial processes through the time-independent utilisation of recovered heat. At Comet Schleifscheiben GmbH, an air-storage demonstrator system with filler materials was tested. The system stores the waste heat generated by firing the ceramic grinding wheels.
A heat exchanger integrated into the chimney recovered the waste heat. One challenge here was the temperature level of the waste heat. In this process, the exhaust air is normally diluted with ambient air and thus cooled before entering the stack, making achieving high temperatures challenging. The researchers remark that selecting the best system must be made on a case-by-case basis, as the best storage solution depends on the parameters specific to the production process, for example, temperature levels, volume flows, flexibility in heat recovery, predicted number of cycles and available space.
Many industrial applications
The project team sees many possible applications for intermediate storage and industrial (waste) heat utilisation. Processes carried out over a wide temperature range between 150°C, and 900°C are suitable. These include applications from the paper, foodstuff or chemical industry, and steam generation.
Dr. Thomas Fluri, group manager for Climate-neutral Industrial Processes and High-Temperature Storage, explains, “Not only heat recovery provides an exciting prospect for industry. Also, power-to-heat is gaining importance as more processes become electrified.” With this concept, heat generation occurs when electricity prices are low and then through storage concepts made available for the entire 24 hour day. This allows load shifting from peak times to off-peak times, saving companies money and reducing the strain on the power grids.
The Fenopthes team sees a further need for the scientific supervision of additional large-scale demonstrators. “High-temperature thermal energy storage technologies and systems are important topics for the heat transition, and we need more demonstrations showing how this technology can be implemented on a large scale,” says Dr. Fluri of Fraunhofer ISE.
The waste heat potential was determined for each chimney, and the waste heat recovery was implemented at the one with the most potential. The project was funded by the German Federal Ministry for Economic Affairs and Climate Protection BMWK.
Cookie Consent
We use cookies to personalize your experience. By continuing to visit this website you agree to our Terms & Conditions, Privacy Policy and Cookie Policy.
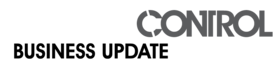