MEP design is a strategic factor in modern construction, ensuring buildings are functional, safe, energy-efficient, and sustainable. Given buildings’ complexity, according to Himanshu Sirohi, Manager—MEP, Lodha, MEP design is central to optimising performance and securing LEED certification.
Why is MEP design considered a strategic advantage for engineering firms in modern construction?
Mechanical, Electrical, and Plumbing (MEP) design ensures the functionality, comfort and safety of a building. MEP design has become more than just a necessity. It has become a strategic advantage for engineering firms. With the increasing complexity of buildings and the demand for sustainable and energy-efficient solutions, MEP design has taken centre stage in shaping the future of construction. The significance of MEP design lies in its ability to optimise building performance and occupant comfort. Without proper MEP design, buildings would lack functionality, efficiency, and safety. The importance of MEP engineering also lies in its ability to integrate these systems seamlessly into a building design and construction process. MEP engineers work closely with architects, structural engineers, and other professionals to ensure that the building infrastructure meets functional requirements and complies with safety codes and regulations.
Efficient MEP design optimises energy consumption, reducing operational costs and enhancing building sustainability. With the increasing focus on environmental conservation and energy efficiency, MEP engineers implement innovative technologies and strategies to minimise buildings’ carbon footprints. This includes integrating renewable energy sources, Smart building automation systems, and energy-efficient equipment and appliances.
How can existing buildings benefit from MEP retrofits to improve energy efficiency?
As the world prioritises sustainability and environmental consciousness, retrofitting MEP systems in existing buildings has become increasingly important. Existing buildings were constructed without the same level of energy efficiency standards. Outdated MEP systems can result in excessive energy consumption, poor indoor air quality, and limited control over comfort levels. Additionally, these systems may not be equipped to handle the requirements of modern technology and advancements in building management systems. Retrofitting MEP systems offers a transformative solution to these challenges. Building owners and managers can achieve significant energy savings, reduce greenhouse gas emissions, and enhance occupant comfort and well-being by upgrading and optimising the MEP systems.
Retrofitting can prolong a building’s lifespan, increase its market value, and align it with current sustainability initiatives and regulations. However, retrofitting MEP systems has its challenges. One of the primary challenges faced during retrofitting is integrating new MEP systems into the existing building layout. The structural constraints of the building, such as limited space or outdated infrastructure, can pose significant obstacles.
Another challenge is navigating the complexities of building codes and regulations. Budget constraints also play a significant role in retrofitting MEP systems. Retrofit projects are typically more cost-intensive than new construction, requiring extensive upgrades. Furthermore, coordination between different MEP disciplines can be a challenge during retrofitting. But once these are taken care of, this can be a game changer.
How does MEP design influence building eligibility for LEED certification?
Leadership in Energy and Environment Design (LEED) certification is a globally recognised rating system for Green buildings that assesses the environmental performance of a building and promotes sustainable design and construction practices. LEED-certified buildings are designed and constructed with a focus on energy efficiency, water conservation, waste reduction, and improved indoor air quality. It helps to reduce operating costs and creates healthier and more comfortable spaces for occupants.
People tend to choose LEED-certified buildings due to their awareness among the public. MEP design plays a crucial role in maximising energy efficiency, reducing environmental impact, and ensuring the overall sustainability of a building. One of the aspects of MEP design for LEED certification is optimising energy usage. It involves implementing advanced HVAC systems, intelligent lighting solutions, and efficient plumbing systems. Another consideration in MEP design for LEED certification is water conservation. By incorporating water-efficient fixtures, implementing rainwater harvesting systems, and innovative plumbing designs, MEP professionals can help reduce water wastage and promote sustainable building water usage.
Furthermore, MEP design plays a vital role in ensuring indoor environmental quality. Proper ventilation, air filtration systems, and low-emission materials create a healthy and comfortable indoor environment. In conclusion, MEP design is critical in achieving LEED certification for sustainable buildings.
How do automation technologies enable MEP systems, resulting in optimised energy consumption?
BMS has complete control over the building’s Air conditioning, energy consumption, security measures, lighting automation, and more – all from one centralised platform. Building Management Systems encompasses building management beyond energy. It is concerned with the overall control, monitoring, and automation of building systems to ensure efficient and safe building operations. Building Energy Management System (BEMS) is a subset of a BMS that deals with energy-related systems and their optimisation for improved energy efficiency and cost savings. BEMS primarily deals with monitoring and controlling MEP systems and other energy-consuming components to minimise energy consumption and reduce the environmental impact of the building.
BMS can include energy-related functions, but a BEMS is tailored to energy management and optimisation. The choice of terminology might depend on energy efficiency or a broader range of building management functions. Implementing building automation systems in MEP design has numerous benefits.
Firstly, it allows for centralised control and monitoring, providing facility managers with a comprehensive view of the building’s performance and status. This real-time visibility enables proactive maintenance and troubleshooting, reducing downtime and enhancing operational efficiency. Secondly, building automation systems enables energy optimisation through intelligent control strategies. The operation of various systems can identify energy-saving opportunities, implement demand response strategies, and adjust settings based on occupancy patterns and environmental conditions. It reduces energy consumption and also contributes to sustainability goals and cost savings. Thirdly, it enhances occupant comfort and well-being. With the ability to monitor and control parameters like temperature, humidity, and lighting levels, building automation systems can create personalised and comfortable environments for building occupants. It improves productivity and contributes to a healthier and more enjoyable indoor experience.
Lastly, building automation systems facilitate data-driven decision-making. By collecting and analysing data on energy usage, system performance, and occupant behaviour, BAS provides valuable insights for optimising building operations, identifying potential issues, and planning future upgrades.
What kinds of trends and challenges require continuous upskilling and training?
Whether design or system development, technology is at the core of MEP design, which every engineer involved in the project knows very well. Therefore, they need to keep pace with technology while considering all the latest trends in building construction. Apart from that, all the engineers and consultants should know the local codes and regulations municipal bodies release for a particular area.
MEP systems must comply with many regulations and standards, varying significantly depending on the region. Maintaining these regulations and ensuring compliance is a continual challenge for contractors and engineers. Non-compliance can result in costly fines and project delays.
MEP industry challenges include complex coordination, wherein integrating mechanical, electrical, and plumbing systems in construction projects is inherently complex. Each system has its requirements and coordinating can be challenging. Poor coordination can lead to clashes between systems, delays in construction, and increased costs. For instance, a ductwork system might interfere with electrical conduit pathways, requiring redesign and rework.
The labour shortage in the skilled trades particularly hits the MEP construction sector. This shortage leads to delays and increased costs as companies need help finding qualified professionals. The ageing workforce and lack of new entrants exacerbate this issue.
Further, increasing pressure exists to design and implement energy-efficient and sustainable MEP systems. This requires staying abreast of the latest technologies and best practices, which is resource-intensive. Additionally, retrofitting existing buildings to improve energy efficiency presents its challenges.
How does the initial building design impact the layout and configuration of MEP systems for future modifications?
The initial building design significantly influences the layout and configuration of systems when considering future modifications. Close collaboration between MEP consultants and design professionals is essential to optimise functionality and aesthetics.
Another factor is flexibility in design, especially for industrial facilities that frequently undergo expansions or modifications. Planning for adaptability allows for easier upgrades and minimises costs during retrofitting, ensuring that performance and safety are not compromised.
High-rise buildings present specific challenges due to their vertical nature, requiring MEP systems to handle increased load demands, manage varying temperatures across different levels, and ensure proper air circulation throughout the structure. Electrical systems must be reliable and resilient to meet power, lighting, communication, and security needs. Plumbing and hydraulic engineering (PHE) systems require careful consideration of water pressure, pipe sizing, adequate supply and efficient waste management system.
Optimising space utilisation is essential for innovative equipment designs. While planning MEP, one should consider using vertical space for various equipment. As redundant systems may require additional space, planning for future equipment needs is crucial.
Cookie Consent
We use cookies to personalize your experience. By continuing to visit this website you agree to our Terms & Conditions, Privacy Policy and Cookie Policy.
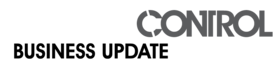