Using low GWP natural refrigerants and solar energy for cold stores along with value addition infrastructure.
Talking about using low GWP refrigerants, Anish Simha, Senior General Manager and Head, RINAC India remarks, we have started the RINAC Centre for excellence and training in Bengaluru. We all know what a cold chain is. Specifically for the perishables, it starts with the processing of handling material from the farm, till the end it reaches the consumer’s place or his location where he is going to have his breakfast, lunch or dinner.
We do categorise cold chain for fruits and vegetables, for dairies, for spices, meat and poultry, marine, pharmaceuticals and then there are other applications also. Now we have a big value chain for each and every aspect, say for instance, the poultry.
When we consider the perishables, fruits and vegetables where our country has been losing loads of rupees every year, we are trying to reduce the losses. We have the produce from the farm and then there are teams called aggregators. It can be for farmers’ produce organisations or a cooperative society. Some firms, traders and Mandis will negotiate with the farmers about the product. There are primary and secondary processing sectors where cleaning, grading, sorting, packing is done and sometimes, we do pulping of some of the products like tomato where the shelf life just 20 days whether you put them into the cold stores or not then pre-cooling is again another part of the primary or secondary processing unit. For distribution in cold stores, it can be a standalone cold store or it can be a pack house where packing can be done. In both the cases we require transport requisition to transport the material. Once it’s pre-cooled, then it has to be under refrigerated conditions and finally, we have the retailing. The convenience store, the supermarket, or doing exports require pre-cooling, thus processing the perishable fruits and vegetables under the cold chain.
The Government of India has put in a lot of effort. It implies they are also developing the cold chain. We have 100 percent FDI in processing industries in which the cold chain is also a part where you have the proactive government policies and fiscal incentives that are incentives for a change and we have about 1.38 billion consumers in India.
India is the largest producer of several Agri-commodities. We are the 5th largest economy in the world and hope India’s retail market to reach U.S. dollar 1.3 trillion by 2025. We have 42 mega food parks out of which 22 are functional and balance are under various stages. In addition to that the government promotes the integrated cold chain and then for already existing cold stores or processing units, we have the value addition infrastructure.
For expansion of food processing or preservation capacities, there are schemes for creation of backward and forward linkages. Backward and forward linkages are from the farm up to the cold stores. Storage is the backward linkage until it gets processed and then after processing it’s a forward linkage till it reaches the consumer. For any industry you will have food safety and quality. Unless you have these then there is no point. The people do not buy material, so we do have to follow the food safety and the quality. So now let’s talk about being a refrigeration engineer.
Pre coolers at pack houses
The pre-cooling is done as soon as you pick the fruit or vegetable we remove from the farm. Eat or bring it down to the storage temperature, maintain high humidity so that the product does not lose the humidity and still retains its fresh taste as well as the weight. So once that is done then the material has to be treated at a lower temperature. And, then we require a reefer vehicle to transport the material once it is pre cooled. From there the cold chain starts, and then it is brought to the pack house.
In the pack house, there might be a small cold room. Pack house is where you do the grading, sorting and cleaning of material. Then there are central cold stores and processing areas in some regions which are closer to the farm, you can have the central poster also.
Do what the Pack houses do, so in addition to that we do have the right wing chambers, precoolers, blast chillers, blast freezers, IKEA plate freezers, and then after it is processed, we will have the cold warehouse. It can be a positive temperature or a negative temperature that you have. The condition passages, anteroom, stock station, then we do have these required warehouses. Then we do have the pre-engineered building construction with storing boxes.
The current trend is to give a turnkey solution to one single contract which also includes severe electrical, plumbing and sanitary fire fighting. Process equipment storage tanks, automation storage racks, and insulated panels are done by requisition contractors as most of the customers want a single point of contact.
The sliding doors in the room in which you’re maintaining the required temperature have all the insulation that prevents the amount of heat entering. Also, the air which gets blown through there’s no outside air entering it. This is another way the insulated panels are manufactured. In a tall building, the length of panels can go up to 15-20 metres.
These are the storage so you just first build the racks and then you clad it with the insulator panel. So these are all modern techniques used now in the cold storage industry. This is what we have already used in India and we’ll be seeing more of such coming to India.
Expectations in 2022
In fully automated cold stores, the product always moves automatically on the conveyors and then there are cranes. The crane positions them inward and outward both through the conveyors. In the year 2022, the worldwide model cold stores need to meet the recommendations for the 2022 cold chain.
India is promoting green refrigeration; so surely, we would like to go green. Also, we should make a guideline where 3000 metric tons is allowable and should use only natural refrigerants with very low global warming potential and better use solar energy for all cold stores. Make it compulsory to use solar energy. So precoolers are a part of the pack house or it has to be near the farm then we do have the reefer vehicle to transport the material.
I am not talking about solar refrigeration, but use solar energy and make it mandatory based on the capacity, say 3000 metric ton and above which should be mandatory. I am sure now we have remote cold rooms with solar refrigeration or solar energy used in refrigeration systems.
Cold chain should be within the reach of the farmers or within the reach where it is being cultivated. For cold stores the government does provide subsidies. So if a cold store has been constructed with a subsidy saying that fruits and vegetables are being stored, we should ensure that at least a minimum quantity of fruits and vegetables are stored there. If it’s 100 percent, it’s good, but then we should not use them to start using them to store other commodities rather than the fruits and vegetables, so have a check on the plant efficiency and promote uniform power tariff. We cannot have a highly power consuming system, then people will find it inoperable and then they switch off and then it leads to a lot of other discrepancies in the material in the product.
Finally, let’s all ensure that we promote a power tariff for cold stores whichever way it can be; initially, till the cold store industry stabilises. Then award the cold stores with higher power efficient refrigeration plants and bring in a uniform 12 percent GST for all the components of the cold chain. Cold chain is everything, including packing, grading, everything. Instead of 18 percent, make it 12 percent, like providing uniform import duty for all cold chain components. In treaty with certain countries we do have zero duties.
We have stabilised cold stores and for stabilised components, we will come out with a model which will be more economical and workable; then Indian companies will also start manufacturing similar components. It is mandatory to use precoolers, which can be two or five metric tons. Once you pre-cool, nobody will transport it in a vehicle which is not refrigerated. So this gives the more usage of reefer vehicles. So you can start the cold chain directly after pre-cooling the product. So we should ensure that once the product is picked from the farm, it has to be pre-cooled within.
Further, we have refrigerants which have been banned and which should not be released into the atmosphere just like that. There are methods that need to be taught to a lot of people in our country about how to handle refrigerants. It must also be ensured that the installation is done with trained manpower so that we do not have short circuit leaks. Anish concludes proper handling of the material is needed; this is what we would like to see in the year 2022 and for future cold stores.
Cookie Consent
We use cookies to personalize your experience. By continuing to visit this website you agree to our Terms & Conditions, Privacy Policy and Cookie Policy.
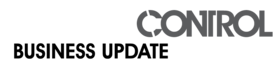