New opportunities also exist in cold chain infrastructure, material handling systems, and reduction of human labour – due to safety and material picking error reasons.
Indian logistics sector to catch up with potential opportunities and future-ready technologies
India is the largest producer of milk. It is the second-largest producer of fruits and vegetables. Unfortunately, 18-20 percent (Valued at 14,500 Crore approx.) of the farm produce is wasted annually – according to the Central Institute of Post-Harvest Engineering and Technology (CIPHET) data. One of the major causes for this is a need for more relevant infrastructure in the country, followed by a lack of awareness. India has about 7500 cold stores with an approximate capacity of 30 million tons, covering only 11 percent of the country’s perishable produce. Hence, the Indian logistics sector must catch up on the cold chain infrastructure. With the announcement of Mega Food Parks projects, there will be a massive demand for good infrastructure in cold chains. It will have a seamless link for the farm product’s movement between the farm gate and the customers. As the largest milk producer India contributes approx. Twelve percent of global milk production. Milk production has been growing over 7 percent CAGR at approx. 227 million. A little more than half of this is available as market surplus, while the remaining is consumed locally. Out of this market surplus, around 36 percent is processed by the organised sector.
In comparison, 64 percent is questionable because a lot of it is going to waste due to a lack of relevant infrastructure. The processed milk products will grow by 50 percent because the market size for these value-added milk products is around USD 10 billion. So clearly, if we see the wastage in the seafood segment – at least 30-40 percent- then the cold chain industry has a lot of untapped potentials with future-ready technologies. The Indian government is actively playing an essential role in this area, and this is a clear growth area for all the stakeholders of this business ecosystem.
Increasing online demand for perishables
With the increase in the buying pattern and the shift towards an online purchase model, there is an apparent demand for robust technologies which will enable material handling in the cold chain more efficiently with the shortest turnaround time. New opportunities are emerging around the last mile deliveries, i.e. delivering them fresh. This may include the various value-added services based on the delivery time duration for multiple customers. An enormous scope of additional cooling processes is required to maintain the cold chain without any break with temperature logging and complete visibility, with the help of growing IoT-based modern cold chain ecosystems. Although material delivery is involved here, there is still a significant ‘Customer Centricity’ element.
Online delivery encouraging warehouse automation technologies
The emerging warehouse automation technologies use “Artificial Intelligence (Data based predictions)”, which is required for the automated systems/equipment to churn out the best performance. In the past, the degree of automation was a factor considered. Now, it is about the intelligence built into these machines to make calculated decisions based on predictive analysis, which is backed by a large amount of data generated in any warehouse. Equipment like AS/ RS cranes, pallet shuttles, carton shuttles, Autonomous Mobile robots (AMRs) and other robotics-based equipment can perform tasks based on intelligent algorithms. This accordingly adjusts the output per the warehouse’s peaks and lows.
Technologies and systems in various combinations
New opportunities exist in the form of cold chain infrastructure, state-of-the-art material handling systems, and reduction or elimination of human labour – due to safety and material picking error reasons. Various technologies and systems in various combinations can be implemented in the cold chain industry. These include material handling, order processing, packaging and last-mile delivery in an environment-friendly manner considering ‘Sustainability” in the process designs.
Cold storage owners must deploy IoT-enabled monitoring solutions.
Cold chain owners must also foresee the potential risks and challenges of implementing modern technologies. And thus, manage post-construction challenges, such as maintaining energy efficiency, temperature balance, and seamless chain operation. There should be careful planning to deal with breakdowns. Hence, the cold storage owners should deploy IoT-enabled monitoring solutions like embedded sensors throughout the cold chain facilities, freezers, chillers or containers. These sensors collect data on environmental conditions and promptly send failure alerts via 4G/5G networks. They transmit the aggregated data to warehouse management systems to ensure a coherent tracking network. It will be worth an investment in incorporating IoT-based solutions for cold chain transformations. The transition from outdated cooling containers to other shipping packages ensures better temperature control, real-time data monitoring and automated reporting. Predictive analytics will help cold chains to be future-ready and sustainable.
Value-added services to qualify as a green cold chain.
The refrigeration sector, including air-conditioning, is responsible for almost 18-20 percent of global electricity consumption. This can be as high as 40 percent of the total national electricity in developing countries. This seriously impacts the environment depending upon the mode of power generation. Adopting natural refrigerants has zero impact on climate; energy-efficient refrigeration systems and technologies qualify for green cold chain. Also, using sustainable packaging like asset pooling like pallets, totes, or any form of reusable packaging, using automation with power regeneration or energy-saving features can collectively help qualify as green cold chain. All this starts from the design of the cold store itself before implementing the technologies.
Intra-logistics solutions
There are various options available when it comes to the intralogistics part. It starts with the design of the cold store, and flooring is taken into consideration; when it is known what kind of material would be stored. Based on various products/materials, the intralogistics solution can be implemented like manual racking systems, multi-tier shelving or mezzanine systems or fully automated solutions like AS/RS systems, conveying solutions, AGVs, robots, shuttle systems etc. The intralogistics solutions are designed based on the product or material type and volume to be handled, weight, pallet size, throughput etc.
Cookie Consent
We use cookies to personalize your experience. By continuing to visit this website you agree to our Terms & Conditions, Privacy Policy and Cookie Policy.
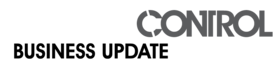