The construction sector’s growth in India is heralding wider opportunities for the Mechanical-ElectricalPlumbing services market.
Opportunities for MEP in the Indian market today
Increasing investments from commercial (I.T. and retail), industries, residential, hotels, hospitals, etc., have given the required impetus to the growth of the MEP market. The value of Indian real estate projects that touched the U.S. $100 billion in 2010 is expected to touch $265 billion in 2020. According to an analysis from Frost & Sullivan, if we factor in total construction projects valued at $265 billion, then at least 25 percent of the construction value can be attributed to MEP design and works. This represents a potential opportunity of $67 billion in the next 10 years. The market witnessed a growth rate of around 9 percent in 2013.
The commercial segment, particularly office and mall space, has remained flat and showed signs of a slowdown in the recent past; however, new office space, malls, hospitals, hotels, and construction projects are expected to be back on track once credit rates and inflation lessens. According to industry sources, India’s area for the commercial building sector is expected to reach 1.9 billion square feet by 2030, as against the present 659 million square feet. About 75 percent of the value of the real estate projects is contributed by the residential segment, which includes not only single homes, ground (G)+2/3/4 floors, but also taller and increasingly complex structures touching up to 30-40 storeys.
“Current MEP projects are not only large but are also complex. Complexity arises due to revisions or amendments in building codes that require the mandatory installation of certain products and systems. Apart from standard services like plumbing and heating, ventilation, air conditioning and refrigeration (HVAC&R), the Indian construction industry is undergoing a sea change concerning the installation and usage of extra-low voltage/ low voltage (ELV/LV) systems, keeping in mind the design and safety aspects of the electrical equipment.”
Increasing penetration of green buildings is also creating a requirement for high-quality and reliable MEP work because of the complexity of designing and constructing a green building. The presence of multiple unorganised participants catering to small, commercial, and residential buildings makes the market highly cost-competitive. This, along with low awareness about integrated MEP offerings shortage of qualified, skilled, and competent workforce, serves as a challenge to this sector’s growth. At the same time, the absence of codes and standards for MEP works in India allows easy entry for the participants, but it creates an environment where quality is often neglected for substandard work.
Globally and in India, there are an increasing number of smart city initiatives that are witnessing more usage of information technology (I.T.) in buildings, transforming them into smart buildings. This will be a real estate and construction trend in the coming years. The study finds that with the advent of convergence of technologies, such as pre-casting, building automation, energy management, etc., MEP players will be dealing with a whole new competitive environment and may have to partner with companies from different industry verticals as never before. Growth in the construction sector, increasing green building penetration, and the need to deliver projects on time drive market growth.
Automation and robotics impact MEP operations
Current research projects aim to bring digital fabrication onto building sites. Integrated design, planning and robotic control processes are being investigated. Versatile onsite fabrication robots are being developed, and cooperation models are being finessed for man-machine and machine-machine interactions. This research is searching for answers to the dilemma of adopting new technologies so the industry has unique capabilities and resilience.
One waste-free robotic fabrication process uses moulds made out of mesh, which enable concrete walls and columns to be fabricated without old-style formwork. A computer generated digital model directs a robot in making high-precision steel mesh dense enough to retain wet concrete. An additive to the concrete makes it thicker and amenable to the mesh mould. This process is especially beneficial for non-standard shapes like geometrically curved walls, thus eliminating the need for expensive custom formwork. The mesh remains part of the final product; hence no waste. The process has already garnered international awards.
Research is also proceeding on digital fabrication: custom-designed, large-scale prefabrication of complex architectural elements. The process combines resource-efficient material systems, joining methods, design tools, and computer technologies. One example is combining high performance fiber-reinforced concrete with 3D printing of sandstone. The sandstone is laid down in an aesthetic architectural design, which includes internal voids; the voids are then filled with HPFRC. This process is explained in a paper presented at the 2017 RILEM Symposium on Ultra-High Performance Fibre-Reinforced Concrete. Such options for custom architectural elements are encouraging to a design world that doesn’t want to be taken over by cold, impersonal machines.
But like it or not, robots are ideally suited to the precision assembly of geometrically complex anything, including timber modules with framing cut to any angle, not just the angles that people can cut and join. As the Connect & Construct article put it, the only thing that matters for robots on the construction site is the tool’s location. The result is that the possibilities and intricacies of timber construction are expanded. The appropriate geometric structure provides its rigidity. As two robots work in machine-machine interaction, one guides the timber as it’s sawed to size, and the other drills the holes for the connection hardware. Together, they guide the framework members into positions as detailed in the digital model. Human workers manually bolt the beams together.
One progressive home builder, Bensonwood, has been a champion of the timber frame home. With its sister company Unity, Bensonwood begins every new construction project with a complete BIM model. It contains all the design, engineering, construction, and machine information embedded in one model. They deploy that model to their automation equipment and build prefabricated homes in a completely automated process. Since 2018, the companies have used state-of-theart robotics in their New Hampshire homebuilding factory. Owner Ted Benson discusses his company’s use of robotics in this thirteen-minute video, “Robotics in Construction.”
Whether or not you’re using robots in your construction projects, they are changing the complexion of your Beginner, intermediate or advanced at any stage, your processes will benefit from having a champion “in the business.” Take a few minutes to request an Applied Software discovery call and discover how emerging technologies and processes like prefabrication can boost your firm’s productivity, safety and profit margins.
Skilled workforce challenges for MEP
The construction industry has a problem: a growing need for more new housing and infrastructure and not enough skilled professionals to do the work. According to estimates, companies need to hire more than 600,000 this year alone and more than 2.2 million over the next three years to meet demand. And according to the U.S. Chamber of Commerce, nearly 90 percent of contractors have experienced moderate-to-high difficulty finding skilled workers.
There are many reasons for this, from increasing retirement rates— more than 20 percent of construction workers are older than 55—to reduced immigration. And with greater automation and digitisation in the industry, future construction jobs will not be the same as the jobs in the past. So even if the industry can find the workers, new skills and approaches are required.
While there’s no simple solution, Autodesk has begun or joined a range of initiatives to help solve the problem, including launching the “Make It Real” program, which aims to bring more young adults into the industry. We’re helping make skills based education available in various formats, awarding microgrants for students that can be used to cover everything from tuition and equipment to transportation and childcare. We’re also sponsoring the While there’s no simple solution, Autodesk has begun or joined a range of initiatives to help solve the problem, including launching the “Make It Real” program, which aims to bring more young adults into the industry. We’re helping make skills based education available in various formats, awarding microgrants for students that can be used to cover everything from tuition and equipment to transportation and childcare. We’re also sponsoring the “Make It Modular” student design challenge, allowing students to test their skills with modular design strategies.
Build your knowledge and increase your insight about how to solve construction workforce challenges with these A.U. resources. Learning Industrialized Construction from Experts in Industry and Academia Taking an industrialised approach to construction is essential to making the industry more efficient, predictable, and sustainable. That means the next generation of construction workers must be familiar with the technologies and processes that make industrialised construction possible. This panel shares how industry and academic institutions can work together to train students today for tomorrow’s construction jobs, so they can enter the job market with the skills they need.
Cookie Consent
We use cookies to personalize your experience. By continuing to visit this website you agree to our Terms & Conditions, Privacy Policy and Cookie Policy.
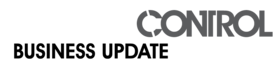