Big chillers and heat pumps will be the best solution shortly when district heating and cooling are the reference system design.
Current market shift and evolving trends for cooling technologies
This can be best answered in two parts. In the short term, the HVAC/R sector worldwide needs to overcome the shortage of components, raw materials, and electricity/ fuel/ gas. This situation requires extraordinary R&D efforts to mitigate the adverse effects. Smart and circular design, high-efficiency technologies – I have mentioned below – effective maintenance services and a new regional approach in the supply chain are some key emerging trends. In the long term, the HVAC/R sector will have one unique target: being environmentally sustainable. The key trends will be electrification, which means heat pumps and the demand for improved efficiency, natural refrigerants, which require dedicated design and technologies, and new business models, i.e. cooling/ heating as a service. Eventually, I believe there will also be space for new technologies as alternatives to the traditional vapour compression circuit, such as magnetic refrigeration – to cite one example.
New opportunities available for large space cooling with increasing industrialisation and urbanisation
If ‘large space cooling’ means high capacity hydronic installations based on high-capacity water chillers, we will need to wait a few more years before seeing any positive evolution. Large chillers and heat pumps will be the best solution, hopefully shortly, when district heating and cooling are the reference system design. This will combine needs and solutions for residential, commercial, and industrial markets. Nowadays, with emerging and evolving demands. Large space cooling is associated with commercial and large building applications.
Specific features of hydrocarbon chillers
Like any hydrocarbon refrigeration and air conditioning applications, hydrocarbon chillers have two specific features. Hydrocarbons as refrigerants offer high efficiency with a simple design in various working conditions. This means that with the same simple design (i.e. type of components required, installation casting materials, design pressures), plenty of applications, from small refrigerators to large water chillers, can effectively work with hydrocarbons. As a second specific feature, which is a drawback, hydrocarbons are flammable and require proper safety measures.
Global warming impacts the demand for cooling equipment
Yes definitely. Global warming is an excellent opportunity for the cooling and heating industry. The opportunity is to dramatically increase the technology used to optimise efficiency and use low-impact refrigerants, such as hydrocarbons, ammonia and carbon dioxide. I believe those who think this is negatively impacting their current business are blind and conservative. They look at the immediate obstacle and do not see great opportunities available.
Chiller system design and operation increase efficiency
As far as design is concerned, the use of advanced technologies such as variable capacity compressors, fans, electronic expansion valves and related control electronics are nowadays the baseline in evolved markets. These bring energy savings exceeding 30 percent compared to traditional technologies that cannot adapt to the variable load and ambient conditions. In terms of operation, the increasing use of monitoring systems allows service companies to check system efficiency in real time, program and, more importantly, optimise maintenance and thus ensure that ideal system efficiency is maintained for years.
Specific refrigerants for the user with chillers from an eco-friendly point of view
They are propane and ammonia. These are the best simply due to their zero ODP, negligible GWP and high efficiency. Going one step further, I would mention carbon dioxide, which has no drawbacks in terms of safety (it’s not flammable and not toxic). Still, it has lower efficiency in this type of application and, in general, lower flexibility.
Since being introduced into the market around 20 years ago, oil-free centrifugal chillers have continued to grow steadily in terms of demand in the air conditioning market. The main reasons are low energy consumption, low noise, and reduced maintenance costs over the compressor’s life. This growth trend will presumably continue over the next few years, with peaks likely higher than recently recorded in both the industrial and comfort sectors.
Two factors will have an influence in this sense: the first is technological and involves the expansion of the operating range of these units, eroding part of the market for chiller units with screw compressors.
The second is geopolitical. The phaseout of fossil fuels due to environmental impact and increasing costs will increase demand for applications such as heat pumps and heat recovery chillers.
μChiller
Process is the CAREL solution for managing air/water and water/water process chillers. The maximum configuration manages two compressors in a single circuit. The distinctive element of the μChiller Process is complete control of high efficiency units through integrated management of two electronic valves (ExV) – expansion and hot gas bypass – and brushless BLDC compressors. This guarantees a prompt response of the compressor as well as higher protection and reliability without neglecting high unit efficiency. The user terminal allows wireless connectivity with mobile devices and is built-in on the panel-mounted models or sold separately on DIN rail-mounted models. The CAREL “APPLICA” app can download and send operating logs relating to serious alarm situations on the unit.
Cookie Consent
We use cookies to personalize your experience. By continuing to visit this website you agree to our Terms & Conditions, Privacy Policy and Cookie Policy.
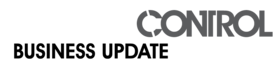