Integrating AI, machine learning, and IoT into temperature control systems revolutionises efficiency and sustainability. Gaurav Bawa, Senior Vice President of WIKA India, perceives digital technologies, including IoT and 5G, as enhancing real-time monitoring and enabling proactive management and connectivity in temperature control systems, impacting manufacturing.
How do you perceive emerging trends in temperature measurement and controls for insulation and cooling systems?
Temperature sensors and controllers have played a pivotal role in the functioning of insulation and cooling systems, evolving significantly since the introduction of the modern thermostat in the early 20th century. Progressing through direct digital control in the mid-20th century and embracing open protocols and network communications by the century’s end, recent years have shifted towards the Industrial Internet of Things (IIoT) and cloud-based computing. These advancements have enabled remote operations and the widespread use of intelligent, connected devices in insulation and cooling systems. This transformation allows for remote monitoring and facilitates predictive maintenance and energy optimisation.
Artificial intelligence and machine learning are increasingly integrated into temperature control systems as technology advances. These developments mark a significant shift, empowering industries to achieve greater efficiency, sustainability, and reliability in insulation and cooling processes. Integrating smart sensors, IoT, and wireless communication technologies enhances real-time monitoring capabilities. Furthermore, advanced data analytics and machine learning algorithms provide predictive insights, enabling proactive system management. This comprehensive approach aligns with the industry’s focus on energy efficiency and sustainability, supported by precise temperature measurements, adaptive control algorithms, and the seamless integration of temperature control systems into broader building management frameworks. Emphasis on cybersecurity measures ensures the secure operation of these interconnected and intelligent temperature control systems.
How does metrology contribute to ensuring the consistency of temperature data for scientific research and meeting regulatory standards?
Metrology ensures the consistency and accuracy of temperature data used for scientific research and regulatory compliance. Metrology is the science of measurement, and in the context of temperature measurement, it involves establishing and maintaining the standards, methods, and best practices to ensure the reliability and traceability of measurements.
Metrology is fundamental to maintaining the uniformity and accuracy of temperature data in scientific research and regulatory adherence. It accomplishes this by establishing universally recognised standards that benchmark temperature measurements in various laboratories and environments. These standards form a consistent reference point, ensuring cohesion across diverse settings.
Calibration, a pivotal facet of metrology, involves routinely assessing instruments used in scientific and regulatory contexts against these established standards. This meticulous process guarantees the accuracy and traceability of these instruments, reinforcing their reliability in temperature measurement.
Precision, a focal point within metrology, assures the consistency of temperature measurements. In scientific fields where even minute temperature fluctuations hold significance, this emphasis on precision enables reliable comparisons and analyses, contributing to robust research outcomes.
Metrology does not just set standards; it also guides the correct selection and validation of measurement instruments and methodologies. This ensures their appropriateness and dependability for specific applications, a critical aspect in various industries, such as pharmaceuticals, healthcare, and environmental monitoring.
Industries reliant on temperature data for compliance, such as pharmaceuticals and environmental monitoring, benefit immensely from adhering to metrological principles. Metrological principles ensure that temperature data meets stringent standards and legal requirements, fostering trust in the accuracy and reliability of information.
Furthermore, metrology champions data integrity and reproducibility by establishing a robust framework for measurement processes. This framework supports replicating experiments and verifying research findings, which is essential for scientific advancement and regulatory compliance.
Ultimately, metrology’s comprehensive approach—establishing standards, ensuring traceability, guiding calibration and validation processes, and advocating for quality assurance practices—forms the basis of reliability and consistency in temperature data across scientific and regulatory landscapes.
Please explain the significance of international standards and calibration methods to ensure the precision of temperature-measuring devices.
Ensuring the accuracy of temperature measurement instruments involves adherence to international standards and well-established calibration procedures. International standards provide a common calibration framework and help achieve measurement consistency across laboratories and industries. These standards serve as the backbone for accurate temperature measurement instruments.
The International System of Units (SI), managed by the International Bureau of Weights and Measures (BIPM), establishes fundamental units like the kelvin for temperature. The International Temperature Scale (ITS) also provides a standardised framework for understanding the temperature of material properties, offering a globally accepted reference for temperature measurements.
Various organisations contribute to setting and maintaining these standards. The International Organisation for Standardisation (ISO) develops norms such as ISO 17025, outlining requirements for testing and calibration labs’ competence, while ISO 9001 addresses quality management systems. ASTM International and the National Institute of Standards and Technology (NIST) in the United States also play critical roles in defining standards related to temperature measurement across industries.
Calibration procedures are essential for ensuring the accuracy and reliability of instruments. These procedures establish traceability by calibrating instruments against known reference standards, ensuring measurements can be linked back to internationally recognised benchmarks. Accredited calibration laboratories following standards like ISO 17025 conduct these calibrations and are regularly audited to meet international criteria.
Critical considerations include calibration intervals, environmental conditions, and uncertainty analysis. Calibration intervals are determined based on instrument stability and measurement criticality, with more crucial applications requiring more frequent calibrations. Environmental factors like temperature and humidity are accounted for during calibration to ensure accurate readings.
Documenting calibration processes is crucial. Detailed records noting calibration dates, standards used, adjustments made, and associated uncertainties ensure transparency and reliability. Calibration laboratories issue certificates documenting calibration results, proving traceability and compliance with quality standards.
Regular maintenance of temperature instruments is integral to calibration practices. This upkeep involves cleaning, checking for wear, and adjusting to uphold accurate measurements. Adhering to international standards and meticulous calibration processes ensures the precision and reliability of temperature measurement instruments, which is crucial for meeting quality requirements, regulatory compliance, and upholding integrity in scientific research and industrial operations.
What challenges arise when upholding temperature measurement standards in data centres and electronics manufacturing environments?
Ensuring precise temperature measurements is paramount in data centres, where on-site IT operations are prevalent. The hardware within these centres is meticulously designed to operate within specified temperature and humidity parameters. Straying from these predefined ranges could damage equipment and nullify warranties.
The American Society of Heating, Refrigerating, and Air-Conditioning Engineers (ASHRAE) has been overseeing temperature and humidity standards for data centres since 2004. Adherence to these standards is imperative for organisations aiming to safeguard the longevity of their hardware. ASHRAE’s “2021 Equipment Thermal Guidelines for Data Processing Environments” provides temperature recommendations for different hardware classes (A1 to A4). According to ASHRAE, the recommended temperature range for A1 to A4 class hardware is 18 to 27 degrees Celsius (64.4 to 80.6 degrees Fahrenheit). This metric is based on the dry-bulb temperature, representing the ambient air temperature surrounding the equipment.
What advantages do digital technologies offer for real-time data analysis and remote monitoring?
One of the significant benefits of digital technologies like IoT in Manufacturing is real-time monitoring of equipment and production processes. Installing advanced IoT sensors on machinery enables continuous data collection of the performance of the equipment and production processes. Manufacturers can analyse this data instantly and proactively identify potential issues before they escalate, enabling predictive maintenance strategies that prevent breakdowns and minimise downtime. This results in enhanced operational efficiency and productivity, ultimately translating into significant cost savings for manufacturers.
Moreover, manufacturers can use IoT technology to monitor product quality in real-time. Manufacturers gain a comprehensive understanding of quality parameters by integrating sensors directly into products and collecting data throughout the entire production process. The timely analysis of this data facilitates the early detection of defects or deviations from standard specifications. This, in turn, allows manufacturers to make instantaneous adjustments to the production process, ensuring higher product quality and reducing defects. The seamless integration of digital technologies enhances operational efficiency, product quality, and cost-effectiveness.
How might integrating 5G technology impact temperature measurement instruments in the manufacturing sector?
The advent of 5G technology is poised to transform manufacturing instruments designed for temperature measurement. With its significantly enhanced connectivity and faster data transfer speeds, 5G opens up new real-time monitoring and control possibilities. This technology facilitates the seamless integration of temperature measurement instruments into Internet of Things (IoT) networks, enabling centralised management and analysis across manufacturing environments. The low latency of 5G supports remote monitoring and decision-making, allowing manufacturing facilities to respond swiftly to temperature fluctuations. Moreover, the increased sensor density made possible by 5G networks provides a more detailed understanding of process temperature variations.
The synergy between 5G and temperature measurement instruments also creates opportunities for innovative applications, such as integrating augmented reality (AR) and virtual reality (VR) for training purposes. As manufacturers embrace Industry 4.0 principles, combining 5G and temperature measurement instruments is expected to contribute to more efficient, responsive, and interconnected manufacturing processes. However, it is imperative to address cybersecurity considerations to ensure the secure operation of these connected systems.
Cookie Consent
We use cookies to personalize your experience. By continuing to visit this website you agree to our Terms & Conditions, Privacy Policy and Cookie Policy.
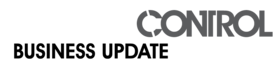