Jayakumar K, Vice President, Sales-India, Middle East & Africa at Copeland, states, “As part of the Make in India initiative, we are shifting from importing scroll compressors to manufacturing them locally. The 500 crore investment is being used to expand our operations. The lab here is not a manufacturing facility; it is more of an innovation center.“
What is the purpose of this lab facility, and why was Pune selected as one of the locations over other options?
Pune provides us with a highly diverse pool of talented engineers. It is a global hub, and we have been operating there for a long time, initially just investing without fully utilising its potential. We aim to tap into the local STEM workforce, as India contributes significantly to the global STEM talent. By leveraging this, we are driving innovation in the region. With our recent inauguration of the copeland Engineering & Technology Center in March 2025 , we are committed to strengthening our presence in Pune.
How will this facility impact your global supply chain distribution?
Copeland operates globally, and we are developing supply chain solutions globally. The innovation happening at this facility is crucial, as it contributes to the global supply chain. India is just one part of it, with eight other locations worldwide working together to support the entire supply chain process.
What production capacity do you expect from this facility?
This is not a manufacturing facility; it is more of an innovation centre. Here, we focus on enabling technologies that help manufacture products at our plants. We have a manufacturing facility in Atit, Maharashtra, where the innovations and technologies developed at this center, will be implemented. Further, these technologies will also be used in manufacturing locations outside of India.
What sustainability goals are you implementing, and how do you ensure their maintenance?
We are committed to driving the energy transition. We conduct analytical research on low GWP (Global Warming Potential) technologies. This aligns with India’s net-zero goals and supports our philosophy and objectives. The initiatives we are pursuing
are aligned with India, what India wants to achieve in terms of sustainability.
India’s government is focusing on a sustainability goal for 2070; what is your company’s sustainability goal?
India’s development approach seems to be on track to achieve its sustainability goals. Many of the products we develop are in line with these objectives. As India undergoes rapid urbanisation and industrial growth, there will be an increasing demand for technologies addressing sustainability challenges.
How does the 500 crore investment support local scroll compressor manufacturing under the Make in India initiative?
As part of the Make in India initiative, we are shifting from importing scroll compressors to manufacturing them locally. The 500 crore investment is being used to expand our operations, including investments in this facility and manufacturing plant in Atit, Maharashtra. This will allow us to produce scroll compressors for the local market.
What is your objective towards collaboration with local suppliers, research institutes, and government initiatives.
Training and development are key for us. We collaborate with the refrigeration and air conditioning industry and annually train around 1,000 engineers in fields like HVACR and refrigeration. This aligns with our corporate social responsibility efforts and helps ensure that the industry has the necessary talent to service equipment. Further, we have a training facility in Gurgaon and a cold chain center focused on refrigeration applications.
Can you elaborate on the technology innovations integrated into this facility?
At this facility, we focus on research and development with three main pillars: sound and vibration, material science, and low GWP technologies to aid carbon and emission reduction. We also collaborate with ISHARE for training and development in these areas. We establish that energy efficiency and sustainability innovations are researched and developed here.
What is your focus on skill development and training and what job creation do you expect here?
The HVACR industry is evolving rapidly with new technologies, such as variable-speed compressors and low GWP refrigerants like R32, which are flammable. We are focusing on training technicians in these new technologies. The industry is gradually adjusting, and we are helping by providing essential training. That will ensure a skilled workforce, is ready to handle these changes.
Currently, around 400 engineers work at this facility. As we progress, we plan to expand this number to meet the growing demands, but the workforce here consists of about 400 people.
How will you ensure the quality of your equipment from this facility?
The lab at this facility is equipped with technologies for sound and vibration testing and reliability assessments. In addition to the testing in this lab, our factories also have labs dedicated to reliability testing. This ensures that our products meet high-quality standards essential for exports to regions like North America, China, and the Middle East. We have Copeland style. All products adhere to Copeland’s global quality standards, which are the same and consistently followed in India.
India is a price-sensitive market; how will you address this?
India is an important market for us, experiencing rapid growth and intense competition. This facility helps us develop technologically advanced and cost-competitive products, enabling us to stay ahead in the market. Innovation is at the core of our strategy to offer high-quality, affordable products that cater to the needs of the Indian market, which again aligns with the Make in India initiative.
How will this facility impact your R&D?
While this facility is a global innovation hub, it also enables us to address the specific needs of the Indian market faster. By having this facility in India, we can develop products that meet local demands, making the development process faster and more efficient.
What is your feedback mechanism?
This facility is focused on research and development. Once a product is designed and qualified, manufacturing occurs at our global plants or Atit. Reliability is monitored at the plant level, and if issues arise in the field, they are addressed by the engineering team. In case of design flaws, the feedback is sent back to our labs for further analysis, whether related to material, sound, or system issues. This feedback loop is part of a continuous improvement process to ensure that quality always stays on top of it.
Cookie Consent
We use cookies to personalize your experience. By continuing to visit this website you agree to our Terms & Conditions, Privacy Policy and Cookie Policy.
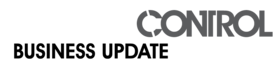