When a life-saving vaccine arrives safely or a crate of fresh produce reaches your plate crisp and cool there’s an unsung hero behind the scenes: insulation. Often hidden from view, insulation quietly works to preserve temperature, prevent spoilage, and ensure reliability across the cold chain. It keeps the cold in, the heat out, and the world running — from hospital corridors to kitchen tables. In industries like pharmaceuticals and logistics, it’s not just about energy savings or efficiency — it’s about trust, safety, and resilience. Experts say insulation isn’t just a component — it’s the backbone of cold chain reliability.
Why Insulation is the Backbone of Cold Chain Resilience?
When a life-saving vaccine arrives safely or a crate of fresh produce reaches your plate crisp and cool — there’s an unsung hero behind the scenes: insulation. Often hidden from view, insulation quietly works to preserve temperature, prevent spoilage, and ensure reliability across the cold chain. It keeps the cold in, the heat out, and the world running — from hospital corridors to kitchen tables. In industries like pharmaceuticals and logistics, it’s not just about energy savings or efficiency — it’s about trust, safety, and resilience. Experts say insulation isn’t just a component — it’s the backbone of cold chain reliability.
========
In the evolving world of HVAC and refrigeration, one element is closely reshaping the insulation industry. Often overlooked and hidden from sight, insulation has stepped into the limelight—fuelled by a global push for energy efficiency, sustainability, and better indoor environmental quality.
The advancements in insulation materials and adherence to regulations are shaping the efficiency and safety of refrigeration systems. Whether it is energy-efficient polyurethane or fire-resistant options, insulation is pivotal in preserving perishable items, averting condensation, and enhancing system performance. Key aspects such as choosing suitable insulation materials, correct installation, upkeep, and moisture management are vital for maximising thermal insulation efficiency and helping in blocking condensation. These tactics improve efficiency, reduce energy consumption, and prolong system durability.
Condensation prevention
Insulation creates a barrier between cold interiors and warmer surroundings, preventing condensation and frost formation. It minimises moisture-related issues and improves energy efficiency while preserving product quality and safety.
Consider the importance of insulation in preventing condensation and ice formation within refrigeration systems. Insulators reduce heat transfer from outside to inside temperatures, thus decreasing energy consumption and enhancing system efficiency. With rising energy costs and environmental concerns, there is a growing focus on using insulation to reduce energy consumption and improve efficiency in refrigeration systems. Advancements in insulation technologies offer newer solutions that further refine this process, reducing energy consumption and ice density.
The challenges posed by condensation and frost formation in refrigeration systems compromise product quality and increase energy consumption. Insulation minimises these issues by sustaining consistent temperatures and reducing the need for the system to compensate for heat loss or gain. This results in lower energy consumption and operational costs, making insulation a vital component in optimising the performance of refrigeration systems while ensuring product quality and safety.
Insulation for refrigeration systems
Thermal insulation safeguards perishable goods along the cold chain by regulating temperatures and minimising heat exposure. The insulation offerings include glass wool and stone wool, known for their high thermal resistance, acoustic properties, and excellent fire safety. Various materials such as polystyrene, polyurethane, fibreglass, rubber, silicates, and silicon-based substances contribute to temperature stability in refrigeration systems, ensuring product quality and safety during transportation and storage.
Using thermal insulation helps keep heat from escaping or entering, which makes it easier to control the temperature around refrigeration systems. This reduces the energy needed to run the system, saves money, and helps the equipment last longer. Insulation works by lowering heat transfer, so the compressor does not have to work as hard to keep the temperature steady and improve overall performance.
New technologies in insulation materials have made refrigeration systems even stronger and more efficient in industries like pharmaceuticals and logistics. When choosing insulation materials, it is important to consider how well they prevent heat and its impact on the environment, safety, noise control, fire resistance, and how much energy they help save.
Kartik Jalan, founder and CEO of Indicold, observes that curtains and automated doors are effective insulation tools that play a vital role in energy conservation. Air curtains help maintain temperature stability by keeping cold air in and preventing hot air from entering when doors are open—beneficial during frequent loading and unloading operations. Meanwhile, automated doors minimise exposure to external air by opening and closing swiftly, thereby improving the refrigeration efficiency of cold storage environments.
In short, applying thermal insulation helps refrigeration systems retain energy better, reduce heat loss, and reduce the need for extra heating or cooling. This results in big energy savings and helps the systems run well for longer.
Insulation in pharma
Thermal insulation directly affects operational efficiency and energy consumption in temperature-sensitive industries. Subramanian N E, Managing Director, Saint-Gobain India – Insulation Business, notes that even minor temperature deviations can compromise product integrity in pharmaceuticals and cold chain logistics.
Advancements in thermal insulation technology improve the effectiveness of refrigeration systems, particularly in sectors like pharmaceuticals and logistics. These advancements for their ability to enable precise temperature control, maintain product quality, and promote sustainability by reducing energy consumption and environmental impact throughout the supply chain.
These advancements improve insulation quality and temperature maintenance and reduce energy consumption in refrigeration systems, ultimately boosting equipment efficiency. Moreover, refinements in thermal insulation technologies result in cost reductions associated with implementing and maintaining refrigeration systems, thus increasing equipment productivity.
Furthermore, advanced thermal insulation technologies contribute to environmental benefits by lowering energy consumption and greenhouse gas emissions. Proper thermal insulation also significantly extends the lifespan of refrigeration equipment. These advancements contribute to productivity and promote environmental protection in industries that rely on refrigeration systems.
Regulatory standards
Regulations act as powerful catalysts for innovation. Subramanian states that as India moves towards its net-zero goals and adopts green building codes like ECBC and IGBC, the thermal performance and fire safety standards are becoming more stringent. We see this as an opportunity, not a challenge. The regulations and standards are pivotal in driving innovative thermal insulation materials in the refrigeration industry. Setting benchmarks for quality and performance compels companies to invest in research and development to enhance their materials to meet these requirements. Bhupendra Ojha, an HVAC industry professional at Marudhar Industries Limited, emphasises that regulations such as ASHRAE standards, EN 378, and ISO 23953 impact pushing the refrigeration industry toward innovation. These standards mandate energy efficiency, safety, and environmental protection, prompting manufacturers to develop better insulation materials and systems. Compliance with these standards is a key driver of R&D investments, resulting in high-performing and environmentally responsible products.
Moreover, adhering to regulations and standards is essential for ensuring the safety and well-being of workers and end-users. Addressing these concerns can inspire innovative solutions in the field. Overall, compliance with regulations and standards in the refrigeration industry can improve quality, safety, and technological development in thermal insulation materials, driving innovation and progress in the field.
Industry-specific standards set by organisations like ASHRAE and ISO further push manufacturers to improve performance and sustainability. This helps advance more efficient, sustainable, and compliant insulation materials, benefiting the industry and global conservation efforts.
Subramanian highlights the role of building codes in enhancing efficiency and performance in HVAC systems. Guidelines like the Energy Conservation Building Code promote sustainability and energy efficiency. Proper insulation over the duct thermal bridging ensures uniform temperatures, reducing heat load and energy bills. Hence, ensure to follow the ECBC 2017 norms and guidelines when designing warehouses. Vishnu Sasidharan, VP and Business Head Climate Technologies, PLUSS Advanced Technologies, suggests a layered approach includes high-performance insulation using materials with low thermal conductivity to minimise external heat ingress, along with thermal energy storage systems such as PCMs, which help in shifting energy loads and maintaining temperature consistency during power outages or transit. Several crucial considerations should be considered to improve the thermal insulation in refrigeration systems.
Insulation and safety
selecting insulation materials tailored to specific requirements, such as thickness, stability against environmental factors, and resistance to melting point and moisture, can enhance system performance.
Secondly, ensuring proper insulation installation at key points where heat transfer is more pronounced can boost system efficiency. Comprehensive insulation coverage across all necessary areas, including joints and irregular surfaces, helps prevent heat leakage and improves system performance.
As Subramanian mentions, fire safety in HVAC insulation is paramount. Fire-resistant insulation is critical in preventing the rapid spread of flames and smoke during fires, facilitating safe evacuation and minimising damage. Unfortunately, fire safety is often overlooked when choosing insulation for HVAC systems. Considering fire safety aspects is essential for ensuring the overall safety and efficiency of HVAC systems. Resolving these issues necessitates thorough inspections at intervals.
Inspections
Bhupendra Ojha, an HVAC industry professional at Marudhar Industries Limited, says regular inspections, timely damage repairs, moisture management, correct installation, and monitoring systems are vital for maintaining thermal insulation efficiency in refrigeration systems. These maintenance practices ensure optimal energy efficiency and performance over time.
Regular inspections must detect signs of damage, wear, or moisture infiltration. Prompt repair of damaged insulation is essential to prevent heat leaks and maintain thermal efficiency. This involves sealing gaps, repairing tears or punctures, and replacing deteriorated insulation material.
Moisture management is crucial to prevent issues like reduced effectiveness and mould growth. Proper installation of insulation materials minimises gaps and thermal bridging, ensuring consistent temperature control. Keeping insulation clean and free from debris, dust, and contaminants helps maintain optimal thermal conductivity and extends lifespan.
Implementing a monitoring and testing system helps regularly assess insulation performance. This may involve conducting thermal imaging tests or using temperature sensors to identify areas of heat loss or inadequate insulation. Maintaining refrigeration systems components, such as doors and seals, complements insulation effectiveness by minimising heat transfer and maintaining thermal efficiency.
Educating personnel on insulation maintenance ensures early identification of potential issues. By following these maintenance practices, thermal insulation in refrigeration systems can be effectively preserved, ensuring optimal energy efficiency and performance over time.
Future innovation
The industry is already seeing the impact of smart insulation technologies integrated with sensors to monitor thermal performance and detect moisture intrusion in real-time. There’s also a growing shift toward eco-friendly and recyclable materials—solutions that perform well and align with global sustainability goals.
Montreal Protocol policy regulation drives the advancement of environmentally friendly and effective insulation materials. Governments and regulatory bodies are tightening standards, too, pushing builders and engineers to rethink insulation as a critical investment—not a cost. This shift presents a golden opportunity for HVAC and refrigeration professionals to lead with innovation, responsibility, and value.
Insulation improves energy efficiency in refrigeration systems, reducing energy consumption and costs and contributing to environmental preservation by minimising its impact on the planet. Regular maintenance, including repairing or replacing damaged components and protecting insulation from wear and tear, is essential to maintaining effectiveness.
Proper moisture control, using suitable materials and methods like waterproof insulation, is crucial for preserving efficiency and extending the system’s lifespan. Ongoing research and innovation in insulation materials drive progress, sustainability, and efficiency in refrigeration systems, facilitated by collaboration among industry players for mutual benefit and environmental conservation. As India advances in infrastructure and smart building development, insulation will play a central role in reducing energy loads, lowering emissions, and enhancing occupant comfort. Plans include the integration of IoT and sensors in insulation systems to monitor real-time performance, enabling smarter energy management and predictive maintenance.
Conclusively, insulation is emerging, finally getting the recognition it deserves. Implementing Smart monitoring systems enables real-time tracking and optimisation of energy usage, echoes Vishnu. It increases productivity. From safeguarding vaccines to keeping fresh produce crisp, from reducing carbon footprints to increasing bottom lines, think of an insulation layer that can make it all possible.
Larger doors also increase air exchange between temperature zones, compromising performance.
Insulation is a support system and a strategic enabler of green, efficient, and resilient HVAC systems. So the next time you think HVAC, think beyond compressors and chillers. Think insulation -the naiveness of performance and sustainability.
============
Vishnu Sasidharan, VP and Business Head Climate Technologies, PLUSS Advanced Technologies.
A layered approach includes high-performance insulation using materials with low thermal conductivity to minimise external heat ingress and thermal energy storage systems such as PCMs, which help maintain temperature consistency during power outages or transit.
Subramanian N E, Managing Director, Saint-Gobain India – Insulation Business.
Regular inspections, prompt damage repairs, moisture management, proper installation, and monitoring systems are essential for maintaining thermal insulation efficiency.
Kartik Jalan, Founder and CEO, Indicold Pvt. Ltd.
Air curtains and automated doors play a big role in saving energy. Air curtains help by keeping cold air in and hot air out when doors are open, which is useful during frequent loading and unloading.
Bhupendra Ojha, HVAC Industry Professional, Marudhar Industries Limited.
Regulations play a pivotal role in pushing the refrigeration industry toward innovation. These standards mandate energy efficiency, safety, and environmental protection, prompting manufacturers to develop better insulation materials and systems.
Cookie Consent
We use cookies to personalize your experience. By continuing to visit this website you agree to our Terms & Conditions, Privacy Policy and Cookie Policy.
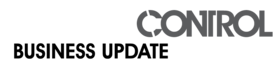