Growing tends in IoT and efficiency are now affecting cold room applications to meet the need for improved food quality and energy savings
Cold rooms are, presently, a very permanent part of everyday living. The increase in the number of foods requiring refrigeration has been the leader in the field; however, unfinished products for eventual processing, drugs, pharmaceuticals, etc., all are adding to the growing need. The ability of the cold storage warehouse owner to wisely select his capital facility and operate it at a low cost will affect all phases of the refrigerated product industry.
In this article, industry experts would be discussing the various aspects considered in the selection and design of cold rooms, and performance improvements in chillers.
Selection and design
The growing global trends in efficiency and IoT are quickly spreading in the food service market, too, affecting commercial and industrial cold room application. Customer requirements increasingly concern reliability, food quality and energy saving aspects that can easily be addressed during the design or retrofit phase of cold room equipment by choosing from the high performance products and modern technologies already established on the market.
Stefano Soggia, CAREL Application Manager, Refrigeration, says, “Reliability comes from product quality, but nowadays, reliability also means connectivity. The ability to connect a cold room 24/7 to a monitoring system that can warn the end user or a trusted installer about any anomaly is priceless, allowing rapid service intervention where necessary. Preventive warnings, alarms and data reports can be accessible anytime and anywhere, from laptops to smartphones, ensuring peace of mind for any user, from shop/restaurant owner to logistics centre manager.”
He adds that cold rooms are essentially used for food storage with the aim of preserving the quality and value of stored goods. Constant and uniform cold distribution must be assured independently of changing working area conditions. The cooperation and continuous communication between an electronic expansion valve assembled on the evaporator and an inverter DC Technology condensing unit, allows the user to avoid the ON/OFF cycle and subsequent temperature “jumps” in the cold room, modulating the refrigerant flow on the evaporator and keeping the room temperature stable within a very narrow band.
A further benefit of this kind of regulation is that the compressor works mainly at a low speed rate, reducing global energy consumption. The electronic expansion valve adapts its working conditions accordingly, automatically optimising system efficiency both in summer/winter changing conditions.
Soggia suggests, “The Cella Range is the Carel cold room product line, a complete package of solutions for refrigeration professionals, including advanced electronic controllers (UltraCella), electronic expansion valves and drivers (ExV Sistema), adiabatic humidifiers (Humidisk) and safety devices (Coldwatch and Gas Leakage protection).”
Condensing units are powered by Carel Inverter DC Technology (Hecu), which brings added benefits thanks to the system approach in communication with UltraCella. Full monitoring capabilities are provided by boss, the system supervisor, ensuring complete local and remote cross-platform supervision.
Improving chiller performance
Today’s technology means there are already solutions available that can considerably increase chiller unit efficiency, says Mirco Temporin, CAREL Application Manager, Commercial Air Conditioning. The first step in many cases is the introduction of advanced control logic, continuing with the integrationof more advanced technologies like electronic expansion valves, modulating actuators and variable-capacity compressors, capable of optimising unit operation in different conditions.
“These devices, linked to an advanced control logic, provide complete unit control based on different environment conditions, with the aim of guaranteeing the optimum conditions for operation, and, in turn, maximum reliability,” he adds. “This brings significant increases in unit COP at part load operation, meaning a higher seasonal performance factor.”
Temporin believes that another distinctive factor, today, thanks to IoT infrastructures, is that systems are always connected. This allows us to optimise system operation in real time, so as to exploit the availability of energy in a ‘smart’ way, especially when this energy comes from renewable sources.
“CAREL offers a comprehensive range of products and solutions to satisfy demand for high efficiency chillers, such as drivers for BLDC compressors, a complete range of electronic expansion valves and tERA, the cloud system for covering customer need in terms of performance and energy efficiency, and guaranteeing system reliability,” he suggests.
Reliability comes from product quality, but nowadays, reliability also means connectivity
Stefano Soggia, CAREL Application Manager, Refrigeration
Connected systems allow us to optimise system operation in real time, so as to exploit the availability of energy in a ‘smart’ way
Mirco Temporin, CAREL Application Manager, Commercial Air Conditioning
Cookie Consent
We use cookies to personalize your experience. By continuing to visit this website you agree to our Terms & Conditions, Privacy Policy and Cookie Policy.
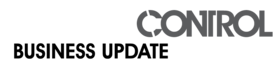