The die and mould industry has undergone stupendous transformation, and is now confidently poised to compete with the global market. Here, the die and mould experts shares what makes them click and shine.
Several studies and surveys have indicated the estimated demand for machine tools to be Rs 14,250 crores in FY 17-18. Production is estimated to have grown by 26 per cent and consumption is estimated to have grown by 23 per cent. This is a very optimistic sign for the entire engineering industry in India including the tooling and die and mould making industry.
Die and mould shaping up India
Die and mould making industry support and supply tools to companies from cross vertical domains such as automotive, aerospace, industrial machinery and heavy engineering, defence to consumer goods and electronics. Raju Battula, National Manager – Technical Support, DesignTech Systems Ltd says, “With augment in industrial output and aggressive promotion of ‘Make-in -India’ campaign, backed with the support of necessary statutory policies restructuring to facilitate ease-of-doing business, the machine tools industry and by that extension, die and mould making industry are envisaged to grow manifolds.”
The die and mould making industry in India has evolved over the years and is at par with the best of international industry names. Ram Grover, Managing Director, Elesa and Ganter India Pvt. Ltd says, “Today, die and mould makers in India can confidently compete with the global market and over the years have recorded phenomenal all-round market growth.”
High quality standard components and high precision are the buzzwords of any die and mould business. The tool room industry is undergoing a change in manufacturing practices. Where earlier, only few important components were manufactured using the CNC machine, now the industry is switching over entirely to CNC to gain a competitive edge. Ram Grover attributes export as another factor for the rapid growth of exports, which involves superior quality standards for the international market. He says, “With this, the need for adopting better technology, components, materials and machinery to ensure high quality, has become very important for Indian businesses.”
The die and mould industry in India has evolved over the years and today it has become a major contributor in Indian economy. Sanjib Chakraborty, Managing Director, Hurco India Pvt Ltd is of the opinion that the automotive industry is the main growth driver for Indian die and mould industry. He says, “Indian automotive sector is set to register a turnover of $ 200 billion by 2026 and auto component industry is set to become the third largest in the world by 2025. Hence, there is enormous potential in coming years.”
Challenges faced
Raju Battula lists some of the challenges which could hinder the growth:
• Trial and error approach
• Inability to invest
• Unavailability of trained manpower
Sanjib Chakraborty is of the opinion that the challenges are within the die and mould community itself. He says, ”With the globalisation of the Indian manufacturing industry, we are seeing a qualitative change with increasing complexity of the product profiles and higher accuracies, coupled with demand for extremely fast deliveries. Today’s die and mould industries need highly efficient process, machine and management system.”
Technologies used
Not only there are several new technologies being introduced to add efficiency and effectiveness to companies’ design and manufacturing operations, but also a lot of technologies that have been around for quite some time, have evolved greatly.
According to Raju Battula, “Die design, no matter how complicated with defining the right tolerances, cooling channels, and gateways, can be done with intricate precision.” He suggests CAE solutions, FEA (finite element analysis), thermal and fluid flow analysis i.e. (CFD) Computational Fluid Dynamics which can be well studied and analysed using virtual simulation software.
He says, ”With the new-age 3D Printing technologies, companies will find it easier to develop patterns in production grade plastic that is not subject to material property variation caused by the changes in temperature and external conditions.”
Today the latest technological trends are driving the die and mould industry by providing cost-effective, energy efficient and environmental friendly solutions for the dies and mould makers. Ram Grover says, “High speed machining, rapid tooling and right CAD/CAM solutions are the latest technologies available in the die and mould making machinery.”
High-speed machining have resulted in the reduction of workload as well as the cost of producing high precision surface finishes, whereas, with the use of proper CAD/CAM solutions, the risk of errors have drastically gone down.
Ram Grover adds, “This sector is emerging as a net exporting industry by understanding and catering to international industrial needs.”
Sanjib Chakraborty says, “The die mould industry in India is mostly limited to SSI and MSI segment. But the investment for latest technology by SSI and MSI units are increasing year by year in India.” Indian companies are now using latest CAD and CAM software, digital technology, in-process probing system.
Is the future optimistic?
Tooling and die and mould industry supply to and support companies from cross vertical domains and industries. With many global companies setting-up their R&D and manufacturing plants in India, this industry will continue to grow.
Government of India is establishing aerospace dedicated SEZs and manufacturing parks in south India. Raju Battula talks positively about the future by saying, “‘Make-in-India’ initiative will provide the thrust to overall engineering and manufacturing industry in India, including industrial machinery and consumer goods. The tooling and mould and die industry will thrive on this growth opportunity. It’s their time to shine.”
The Indian die and mould sector can contest globally with aplomb, where we also see lots of technologies coming up in the industry. Ram Grover says, “There’s no denying that with globalisation, there has been a lot more emphasis on the quality when it comes to the kind of moulds being utilised across different industry segments.”
The industry also brings with it the demand for innovative technologies and resourceful products. Moreover, cost competitiveness through shorter run times and upgrading productivity are some of its foremost deliverables.
Sanjib Chakraborty of Hurco India concludes by saying, “The fastest growing aviation and medical component industry along with automobile industry assured immense potential in die and mould industry. I am very optimistic. So, we shouldn’t focus on the short-term high point and low point of the growth curve. I would look at the large numbers for India and it is telling us that we have enormous potential in coming years.”
I would look at the large numbers for India and it is telling us that we have enormous potential in coming years
Sanjib Chakraborty, Managing Director, Hurco India Pvt Ltd
Die design, no matter how complicated with defining the right tolerances, cooling channels, and gateways, can be done with intricate precision
Raju Battula, National Manager – Technical Support, DesignTech Systems Ltd.
High speed machining, rapid tooling and right CAD/CAM solutions are the latest technologies available in the die and mould making machinery
Ram Grover, Managing Director, Elesa and Ganter India Pvt. Ltd.
Cookie Consent
We use cookies to personalize your experience. By continuing to visit this website you agree to our Terms & Conditions, Privacy Policy and Cookie Policy.
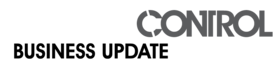