Authored by- Ravi Saran Key Account manager, APAC Swiss Rotors.
Plate heat exchangers are efficient heat recovery units used in a range of commercial, industrial and residential settings. By extracting sensible energy from exhaust air, and using it to cool or heat incoming air, a plate heat exchanger can make a dramatic difference to a building’s energy costs and environmental impact. They are built using a simple engineering principle. Layers of aluminium or polymer plates are positioned in the heat exchange core with gaps between them, enabling air to flow freely. Exhaust air is carefully funnelled between some of the layers.
At the same time, incoming air is funnelled in the other direction between the other layers. Depending on the climate, the exhaust air heats or cools the plates. This sensible energy is then transferred to the incoming air. Modern plate heat exchangers can recover the vast majority of sensible energy, so their impact is significant. Plate heat exchangers also offer other considerable benefits. Because a plate heat exchanger keeps incoming and exhaust air supplies separate, there is no risk of cross contamination. Swiss Rotors’ plate heat exchangers, for example, are tested in accordance with EN308 to ensure no leakage.
They also hold VDI 6022 and SWKI VA104-01 hygiene certificates. As the world battles a pandemic and becomes increasingly focused on securing substantial and clean indoor ventilation, the impact of removing cross-contamination worries cannot be understated. Plate heat exchangers are also capable of reversible energy recovery, making them well suited to warmer climates where the focus is on cooling – rather than heating – incoming air. They are popular in hot regions such as the Middle East, where demand for HVAC solutions is permanently high. Finally, plate heat exchangers are available in a range of different sizes. This means they are appropriate for different buildings, different situations and different industries.
Why is a plate heat exchanger the most efficient heat recovery unit?
To understand how effective and efficient a plate heat exchanger is, we must first establish what a ‘perfect’ solution would look like. Why? Because efficiency is a comparison between real-world performance and ideal performance. Professor Ahmad Fakheri defines heat exchanger efficiency as “the ratio of the heat transferred in the actual heat exchanger to the heat that would be transferred in the ideal heat exchanger”. Ideal performance is established with modelling, and includes the limitations imposed by factors such as the second law of thermodynamics, which says that increasing amounts of energy are wasted every time it is transferred or transformed.
By establishing the levels involved in ‘perfect’ or ‘ideal’ heat exchanger efficiency, which transfers the maximum amount of heat and generates the minimum amount of entropy, a benchmark is set, against which existing plate heat exchangers can be measured. With those factors embedded into industry calculations, plate heat exchangers are still consistently found to be the most efficient of all heat exchangers. Typically, they can achieve efficiency rates of approximately 90 percent. This is higher than the efficiency offered by kettle, tubular, spiral or shell and tube heat exchangers. And, it is that efficiency that makes plate heat exchangers so attractive for building managers looking to reduce their energy costs and lower their environmental impact. However, there is still a range of performance available within the plate heat exchanger family.
Older models may offer lower efficiency, while counterflow heat exchangers – the latest iteration of plate heat exchangers – take performance to new levels. These next-generation models bring together best manufacturing practices with the most efficient choices in materials, packaging and overall production costs. Counterflow heat exchangers extend the energy exchange path while maintaining the minimum possible pressure drop. This is the secret to their high efficiency level. Moreover, high energy recovery levels and zero cross-contamination, counterflow heat exchangers also feature double-folded plate connections (which ensures airtightness), uniquely-shaped plates (designed to ensure effective distribution of the air) and comparatively low purchase prices. Swiss Rotors’ range of counterflow heat exchangers are made with either aluminium or composite plates. Sizes range from 19.5” x 10.5” up to 46.5” x 37.5”. All models are tested to EN308 and are operational from -40°F up to 158°F (aluminium plates) and from -4°F up to 122°F (composite plates).
Calculating the efficiency of plate heat exchangers
Two main models exist to help you calculate the performance efficiency of a plate heat exchanger. The log-mean temperature difference method (LMTD) provides a rate of heat transfer through the following calculation:
Q = UA(FΔTlm)
In this equation, U is the overall heat transfer coefficient, A is the total area of heat transfer, ΔTlm is the log-mean temperature difference, and F is the log mean temperature difference correction factor. The LMTD approach is most commonly adopted when the inlet and exit temperatures are established, but the size of the heat exchanger is still to be decided.
As an alternative to the LMTD approach, the thermal effectiveness method determines the real-world heat transfer occurring inside the heat exchanger against the maximum possible heat transfer. It is expressed as a ratio.
E = Q / Qmax
This approach is most common when building managers or engineers are attempting to determine the heat transfer rate and the fluid exit temperatures, and already know the size of the heat exchanger and the inlet temperatures. Swiss Rotors has developed a free online tool to help you calculate the efficiency of your heat plate exchanger. Simply input details relating to the air (volume, flow, temperature, relative humidity) alongside your exchanger type, plate distance and static pressure measurements. The tool will then calculate your exchanger’s efficiency levels – completely free of charge.
How to choose the most efficient plate heat exchanger
Choosing the most efficient plate heat exchanger will depend on your use case and the wider environment in which you operate. However, there is no doubt that a plate heat exchanger is the most efficient type of heat exchanger currently on the market – and Swiss Rotors’ counterflow heat exchangers take this performance to the next level. Our counterflow heat exchangers offer further options to refine performance as appropriate for your application. For example, choose the 2mm fin spacing to ensure the highest possible efficiency as or opt for 3mm fin spacing to guarantee minimal pressure loss. Hospitals and laboratories regularly choose our counterflow heat exchangers simply because of the outstanding hygiene levels involved.
The construction of the exchanger guarantees the separation of the air streams, with either ultrasonic welding or double-folded edges and hot-melt glue working to prevent leaks and cross contamination. This is validated by the units’ ongoing VDI 6022 and SWKI VA104- 01 certifications. Furthermore, all our exchangers are tested for air tightness in accordance with EN308. A full range of sizes is available to fit all standard industry formats, while the option of aluminium or polymer provides versatility capable of meeting different needs. Polymer counterflow heat exchangers, for example, are generally cheaper and easier to handle during the manufacturing process – creating a lower final product price. They are also more resistant to corrosion, and easier to install due to their lighter weight.
Aluminium counterflow heat exchangers, meanwhile, offer a wider range of operating temperatures. They can function anywhere between -40ºC and 70ºC and require an air compressor – rather than a pressure washer – for cleaning and ongoing maintenance. By offering reversible energy recovery, counterflow heat exchangers are suitable for both building cooling or heating. Our highly automated manufacturing process is built on a guarantee of Swiss precision, competitive pricing and a short two-week lead time.
Cookie Consent
We use cookies to personalize your experience. By continuing to visit this website you agree to our Terms & Conditions, Privacy Policy and Cookie Policy.
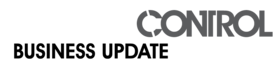