HVAC systems are complex with a number of connected parts and more often than not, automated to ensure that the desired operating conditions are maintained. A number of factors need to be considered to ensure safe operations of HVAC equipment, the requirements and practices for which are covered under the safety standards such OHSAS in which FSC is certified. Some key practices that are vital to ensure safe practices are
Identifying Hazards
Based on the standards defined, a HIRA (Hazard Identification and Risk Assessment) is carried out to identify any potential hazards on each job site and take the proper safety precautions during operations. A detailed HIRA identifies the hazards, details the consequence &identifies the frequency and arrives at a risk estimation based on the existing controls. Recommendations are then drawn and implemented to reduce those risks which are not under acceptable limits and the same Hazard is re-evaluated to ensure that they are now under control.
Sensors to detect leakage of refrigerant
Refrigerants used for HVAC system such as Ammonia are flammable and Hazardous thus posing a great danger in the event of a leakage. It is thus critical that sensors are in place to identify the leakages so the same can be addressed immediately before any unforeseen event occurs.
Preventive Maintenance
Given the high number of moving parts and complex ducting and electrical systems, it is vital that there is a preventive maintenance schedule is drawn up and the same is adhered to. This helps in ensuring that the systems are safe and operating at the optimal levels.
Training
Ground personnel, especially the one working on the refrigeration systems need to be trained to handle the systems and exigencies that may arise on failure. Emergency response training for refrigerant leak, system failures or fire will have to be regularly arranged to ensure that there is no backlog in process training for those responsible for handling the specific instruments and equipments.
Lockout-tagout, or LOTO
Apart from hazards from machines during operation, there are also hazards when the machines are switched as long as energy sources such as electricity, refrigerant, steam, pressurized water, and compressed air are attached to the HVAC system. A step by step Lock Out – Tag Out procedure should thus be in place which ensures that all the employees are notified, the equipment are shut down properly, all secondary sources are cut off and proper procedures are followed.
There may be several reasons for taking a risk, but one must work to be cognisant of these critical parameters and factors and make efforts on marginalising them. In order to provide safe access and fall protection the layout should include suitable stairs, ladders, and guarding throughout the engineered system. Because dropping off pallet or equipment at elevated levels, may be required as well in such engineered systems, providing for safe drop zones (through an opening in the side railing to allow east receipt) should be properly planned.
So, when optimal storage, material flow, safety and compliance are required in a warehouse, proactive managers will get the help they need up front to avoid costly surprise, delay or retrofits.
Cookie Consent
We use cookies to personalize your experience. By continuing to visit this website you agree to our Terms & Conditions, Privacy Policy and Cookie Policy.
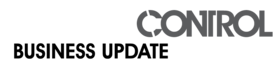