A compressor’s total cost of ownership includes the cost of purchase as well as the cost of operation over its lifespan.
When your company decides to convert to an energy-efficient, environmentally friendly air compressor, it has already made the most essential and advantageous decision. However, there are a number of factors to consider in order to optimise your savings and lower your total cost of ownership.
While alterations can be made after the compressor has been purchased, these changes are usually linked with greater costs. As a result, it’s critical to get it properly the first time.
Keeping down investment costs
A compressor’s total cost of ownership includes the cost of purchase as well as the cost of operation over its lifespan. The most recent environmentally friendly compressors with the most cutting-edge technology are normally more expensive, but they have reduced running expenses, which saves money in the long term. In actuality, the original investment accounts for a minor portion of the total cost of ownership, with energy expenditures accounting for the majority.
Choosing the correct air compressor type is still important, even though contemporary air compressors are all about efficiency. That implies buyers must first determine their compressed air requirements.
That starts by asking themselves the following questions:
- How much airflow and pressure do they need and for which applications?
- Will the compressor run constantly or intermittently?
- How important is air quality?
- Does the air demand fluctuate or remain steady?
The answers to these questions will decide the optimal compressor size, if a model with variable speed drive is better (for changing air demand), and whether a piston compressor or a rotary screw compressor is required (for intermittent use and limited air demand).
An oil-free compressor is the best option if air quality is a priority. A drier should be included if the application requires dry air.
All of these options demonstrate the importance of knowing the answers ahead of time. An air dryer, for example, could be installed after the fact, but it would be more expensive.
Keeping down operating costs
After you have decided on the most energy-efficient air compressor for your needs, the next step is to cut operating costs even more. You have a lot of possibilities. Keep in mind that the quality of the intake air is just as important as the purity of the departing air.
It is preferable if the air is cleaner. If the compressor is installed in a location where the intake air is filthy or dusty, for example, such particles will find their way into the equipment, necessitating the use of filters to keep them out of the compressed airflow. And each filter will increase your maintenance price and cause a pressure decrease, hence increasing your energy bills.
That is why it is important to place the compressor in an area where such air contaminants are kept to a minimum. Ambient temperature also matters. A 5°C increase in the air inlet temperature will reduce the compressor’s performance by 2 percent. And that efficiency loss adds up over time.
Another way to optimise your compressor efficiency is to reduce the pressure in its distribution system by 1 bar (14.5 psi), which saves 7 percent in electric costs. If your applications can run at a lower pressure, then this is a very simple measure you can take to cut your electric bill even more. An effective way of doing this is to use a central controller for all compressors and dryers. This allows operators to choose the best machine combination and save energy. This type of controller can also be combined with connectivity technologies, allowing you to monitor and optimise your compressed air system from anywhere.
Do not let your heat go to waste
Heat is produced by compressors. To keep the ambient temperature low, most organisations allow the heat to dissipate as rapidly as possible. However, rather than letting it go to waste, installing an energy recovery system will allow you to collect and reuse up to 90 percent of the energy used to drive a compressor.
Don’t let the warmth evaporate into thin air. Use it to heat a structure, water, or steam instead.
Allow a professional to assist you in selecting an energy-efficient air compressor.Granted, there is a lot to consider, but if you follow the suggestions above, you will soon reduce your carbon footprint while also lowering your energy bill.
Cookie Consent
We use cookies to personalize your experience. By continuing to visit this website you agree to our Terms & Conditions, Privacy Policy and Cookie Policy.
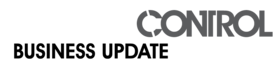