With an inverter programmed by a control logic that is simple to operate, the variable speed compressor opens a set of possibilities to simplify processes.
Working with refrigeration means having one eye on the present and the other on the future, always. Compressors are becoming smaller, quieter, more efficient, and more environmentally sustainable. However, little is said about the one device that has highly contributed to generating some of the most significant results in these topics during recent years: the inverter.
This electronic device is what drives the variable speed compressor (VCC). The compressor has been taking energy efficiency results to new levels. The levels in turn are pushed constantly up by the stringent energy consumption regulations for commercial refrigeration equipment in Europe and other regions around the world. After all, it has become clear that higher levels of energy efficiency are mandatory for environmental sustainability nowadays, and more so, in the future.
It is desired for any player in the commercial refrigeration segment to create more intimacy with the inverter, especially the original equipment manufacturers. This article tries to demystify the perception of complexity around this device, and to show the simplifications and gains it can bring to OEMs and the end user.
What is inside an inverter?
In a very simple explanation: inside the inverter’s enclosure there is an electronic board composed by an input stage called AC/ DC converter (from alternate to direct current converter), and an output power stage called DC/AC “inverter”, that generates from DC current an AC current at proper level and frequency. The device’s intelligence is embedded software, installed in a 0.2 square inches microcontroller. The software implements the motor control logic and the inverter operation to drive the compressor’s BLDC (Brushless Direct Current) motor.
The use of sensorless motor control technology, the one used by Embraco inverters, allows the solution to be simpler. The inverter dismisses any sensor by reading the feedback signal from the motor’s coils (also known as back electromotive force). With that, it calculates how to generate the proper output frequency and power to drive the motor at a given speed despite the load.
Speed is the key element
The inverter and motor compose a system that can modulate the cooling capacity. It can do so by adjusting the compressor’s working speed (inverter output frequency); reducing it during low demands (low ambient temperature or no door opening) and increasing it under high demands (pull down, reload or high ambient temperature). The variable speed compressor does that without switching on and off as frequently – as a traditional, fixed speed, compressor would do.
A variable speed compressor can usually work in a range from 1.600 to 4.500 rpm (rotations per minute),whereas a fixed speed only runs at the power supply frequency (3000rpm for 50Hz and 3600rpm for 60Hz). The variable speed compressor delivers a faster pull down or temperature recovery any time the refrigerator door is opened. For example, in food retail or food service establishments it happens all the time, all day long. After reaching the desired temperature, it goes back to a speed behavior, where the coefficient of performance is maximized. It means delivering the needed cooling capacity with the least energy consumption possible. By being quicker in these transitions, the variable speed compressor not only saves energy but preserves the food quality.
The graph shows how the variable speed compressor saves energy And we cannot fail to mention the lower noise levels delivered by variable speed compressors. Thanks to the fact that the inverter controls it in order to, operate in the lowest and more silent rotation levels possible, most of the time.
Taking complexity out of equation
The key in using a variable speed compressor, dealing with an inverter, is how to make this whole system work at its optimum cooling capacity and saving energy. This goal is achieved through the adjustment of a set of parameters. These might be implemented by the electronic controller of the appliance or by the inverter itself when configured to run with embedded control logic and a simpler controller (or even a thermostat). The embedded control logic of Embraco compressors, named Smart Drop-In (SDI), is in its second generation already. It was created to extract all the benefits from the variable speed compressor, in a variety of applications and conditions, in the most practical and simple way possible. With Smart Drop-in, the controller will be the same as the one for fixed speed (on-off) compressors, a thermostat, and the SDI logic, and will be responsible to determine the right speed, depending on the capacity demand. Simplicity comes from the fact that the adjustment of only one parameter allows the appliance to reach good results.
This movement of evolution in the inverter’s embedded control logic – is allowing the popularisation of the variable speed compressor in the commercial refrigeration industry, even for the smaller OEMs. Particularly, those OEM’s that are not always stacked with the required internal resources to deal with the complexity of a control unit. The use of a simple embedded control logic like the Smart Drop-In takes the complexity out of the equation, not only in the refrigeration equipment manufacturing lines but also during service in the field. Without having to go through extensive training, the OEM’s maintenance team connects their computer to the inverter and has a total of 6 parameters to work with, and that is it.
Developing today the solution for future Let’s take the following example of energy efficiency gains with the embedded control logic. At Nidec Global Appliance, holder of the Embraco brand of refrigeration solutions, a customer’s vertical freezer for professional kitchens currently uses compressors from the Embraco EMC lineup, the brand’s most efficient on-off compressor. With it, the application already achieves the B – label for energy consumption, with which the customer is very satisfied. No one in the professional kitchen segment has achieved A – label in this kind of application yet.
But, the customer is already working towards having a flagship product to reach A – label, especially considering, that the food service market expects new versions of the energy efficiency regulations, for this segment’s refrigeration equipment in 1 or 2 years. For that reason, we recently tested the same vertical freezer, under various ambient temperatures and conditions, using Embraco’s most energy efficient variable speed compressors family, the FMF, controlled by the Smart DropIn (SDI) logic, and were able to bring the energy consumption 15,7 percent lower. It is simple like that – only switching the compressor and making three SDI parameters tuning. It is important to add that if it wasn’t a comparison versus the most energy efficient (best COP) model on the market, but an average R290 fixed speed – the saving would be considerably higher, around 25 percent.
The end users in the food service segment will make the math of the return on investment over time and if a more efficient product pays for itself quick enough, it will be the right choice.
Versatility that leads to simplification
With an inverter programmed by a control logic that is simple to operate, the variable speed compressor opens a set of possibilities to simplify processes. In the production line, equipment manufacturers can simplify their compressor’s inventory working with less different models to deliver the desired cooling capacity, than when working with fixed speed devices. As said before, the inverter makes the compressor achieve a greater range of RPMs, allowing the use of the same compressor for a wider range of appliances sizes. It also allows the adoption of the same compressor for a wider range of ambient temperatures, not compromising temperature stability.
Inverters also make the compressor more reliable under voltage fluctuations, especially in low voltage environments. And, they can also lead to inventory simplification by enabling dual voltage solutions. At Nidec Global Appliance, we understand that the whole Embraco commercial refrigeration inverters portfolio must have dual voltage options. This way, with the very same inverter, a variable speed compressor can operate in 115V and 220V regions, even those with unstable electrical grids.
Moreover, in a variable speed compressor, thanks to the applied technology, the motor can be smaller doing the same job as its fixed speed counterpart, thus reducing the size of the whole system. This brings several benefits such as more available space for products in the cabinet, and reduced transport costs.
In conclusion, inverters and variable speed compressors contribute to reach higher competitiveness, by leveraging energy savings, reducing ambient noise, allowing more space in the cabinets, as well as reducing portfolio complexity with less compressors models (SKUs).
Cookie Consent
We use cookies to personalize your experience. By continuing to visit this website you agree to our Terms & Conditions, Privacy Policy and Cookie Policy.
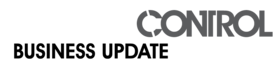