Batteries make up most of the EV cost. With the advantage of energy efficiency and the shortest manufacturing lead time, the LDP technology is the ideal solution for manufacturing cost-effective Li-ion batteries.
The advanced technology used in electric vehicles is strengthening its proposition as the future of the automobile industry. EVs are being sought across the globe for their eco-friendly solutions, which are efficient at curbing the release of vehicular exhaust into the air. Even India is actively participating in this mission of EV transformation and has pledged to become the EV first nation by 2030.
EVs are the best alternative to fossil fuel-powered vehicles backed up with cleantech solutions for nullifying the emission of harmful gases into the environment. The advantage of lower maintenance cost is another factor driving the acceptance of EVs in the country. The green solutions in EVs are possible only because they depend on electricity for power. Hence, electricity is essential in driving the industry’s unrivalled EV performance.
As a result, the importance of Lithium-ion batteries comes to the forefront, which is at the heart of the EV ecosystem. It is highly preferred for its high energy per unit mass compared to other electrical energy storage systems available in the market.
The advanced technology in Li-ion batteries gives it the advantage of high energy efficiency, high power-to-weight ratio, high-temperature performance, and low self-discharge. Along with this, the batteries have better energy storage density that requires a smaller size.
Given the wide gamut of advantages, Li-ion batteries are the preferred choice in the EV industry. It is globally accepted for its highly competitive latest technology, the ability to charge and discharge energy safely, and minimum charging time. And to top it all up, the plunging prices make it to the list of manufacturers. The importance of Li-ion batteries can be seen from the fact that they make up 40-50 percent of the electric vehicle cost. Forming a crucial part of the entire vehicle, any fault in the Li-ion battery will be responsible for revoking the vehicle from the market and can cost the growth of the entire industry as a whole.
With so many EVs catching fire coming to light, a lot of responsibility lies on the battery sector to come up with highly competitive and safe batteries. Therefore, before venturing into EVs, the industry must first focus on setting the proper infrastructure for battery manufacturing. The components making up Li-ion batteries are highly hygroscopic and tend to absorb moisture in the air. Hence, carrying out the battery manufacturing process is highly controlled environmental conditions is a prerequisite. The humidity level must be highly regulated and monitored throughout the battery manufacturing and assembling and must be maintained at less than 1 percent humidity in a stable environment.
To achieve the required environmental conditions, Li-ion battery manufacturing must be carried out in Dry Rooms. It comes with the Environment Control Dehumidification System for maintaining the RH at less than 1 percent and 10 percent during lithium cell manufacturing and battery assembling, respectively. Dry Rooms come with the backup of moisture control equipment for achieving extremely low dew point, as low as -80°C for the ideal processing of hygroscopic and moisture-sensitive materials.
Considering the importance of desiccant dehumidification technology, Bry-Air Dry Rooms come with the patented Environment Control Dehumidification System, Green DryPurge (GDP) series, and highly efficient Super Low Dew Point (LDP) series that provide dehumidification/ moisture control solutions in perfect confluence with a refrigeration system to maintain the desired RH within the narrow humidity bracket. As mentioned above, batteries make up most of the EV cost. With the advantage of energy efficiency and the shortest manufacturing lead time, the LDP technology is the ideal solution for manufacturing cost-effective Li-ion batteries.
Failing to control the humidity can give rise to safety concerns where the chances of explosion are high due to the production of inferior- quality batteries. This event compromises the performance of the vehicle. As a result, the manufacturers must be agile enough to adopt dehumidification technology to manufacture error-free, high-quality Li-ion batteries.
Cookie Consent
We use cookies to personalize your experience. By continuing to visit this website you agree to our Terms & Conditions, Privacy Policy and Cookie Policy.
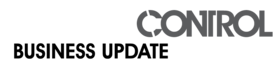