Temperature monitoring and logging using temperature loggers is common practice in the Pharmaceutical industry to ensure the integrity of temperature-sensitive drugs, vaccines, medications, and biological samples during transportation and storage.
The origins of temperature loggers can be traced back to the early days of data recording technology. Initially, these loggers were mechanical and used a pen on a rotating drum to capture temperature fluctuations. However, as technology progressed, so did the capabilities of these devices. With the advent of digital technology, temperature loggers have become more compact, efficient, and affordable. With the latest development integrating Internet of Things (IoT) technology into temperature loggers, this trend has persisted, enabling even more advanced features and functionality. With the latest real-time temperature logging devices, you can monitor temperature and other parameters like Humidity, vibration, pressure, shock and light.
IoT and sensors for temperature monitoring during transportation
By employing an IoT sensor, the temperature of a shipment can be automatically monitored and recorded. These temperature readings are accessible in near real-time from any Internet-connected device worldwide.
Several technologies have been tested to obtain real-time temperature data during the air transport of shipments, but a challenge arises when the shipment is in the air. To avoid interference with the aircraft’s navigation system, the sensor must be turned off during the flight. However, the recorded data is still captured and becomes available once it is transmitted to the cloud after the flight has landed.
Affordable packages for temperature-sensitive goods
In the context of transporting temperature-sensitive products, affordability is an important consideration, but it should be prioritised after assessing the product’s value. For instance, if the product is a life-saving drug, vaccine, clinical trial sample, or R&D sample, where any temperature deviation could compromise its integrity, affordability becomes a secondary concern to imply affordability should be the last factor to be looked at.
However, calculated risks and assessed chances can be taken for finished products with stability data supporting slight temperature deviations. Various cost-effective packages are available in the market, such as combining refrigerants like ice packs and gel packs with insulation materials like EPS. It is crucial to ensure that any packaging system is qualified before use.
Packaging systems
Two packaging systems help maintain temperature control in temperature-sensitive shipments, active and passive. Active systems are systems that require an external energy source to maintain temperature. In contrast, passive systems use Phase Change Materials which only need to be prepared in freezers/ refrigerators for a stipulated time to help maintain the temperature in the packaging system during transportation.
Transport facilities ensure controlled temperature retention.
The transportation facilities at various stages of the transport cycle have different requirements. When preparing samples at the manufacturing site, it is crucial to use an appropriate packaging system that complies with regulations.
Once the correct packaging system is utilised, it must be transported to the airport (for air transport) in a suitable storage unit such as an air-conditioned or temperature-controlled vehicle or a reefer vehicle. Upon arrival at the airport, the package should be stored at the appropriate temperature in cold rooms equipped with calibrated temperature sensors. During this time, it should be protected from prolonged exposure to ambient air on the tarmac, and if necessary, cool dollies or thermal blankets can be used. Selecting an airline that offers temperature-controlled services is crucial.
The temperature-controlled package must be stored at the correct temperature on the aircraft and during the flight. The same process should be followed upon reaching the destination, ensuring proper storage and transportation until the final delivery to the recipient.
Storage temperature to longer distance transport
When transporting over longer distances, it is crucial to use a packaging system that is suitable and qualified for the anticipated transit time. For example, if the estimated transit time is 100 hours, it is recommended to utilise a packaging system qualified for 120 hours. The package should be stored at the appropriate temperature during transit, and, if necessary, the refrigerant should be replenished before the qualification time of the package expires.
In the case of shipments using dry ice, it is important to regularly top up the dry ice at each transit point or every 24-48 hours, depending on the size of the box. As for PCMs (Phase Change Materials) or gel packs, it is essential to ensure proper storage and replenishment to maintain the desired temperature conditions.
Expertise shared by – Preeti Saluja, Pharmaceutical cold chain and GDP expert.
Cookie Consent
We use cookies to personalize your experience. By continuing to visit this website you agree to our Terms & Conditions, Privacy Policy and Cookie Policy.
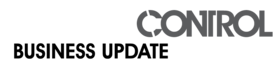