Cold storage quietly keeps the world running, from the milk on your breakfast table to life-saving vaccines. But behind this seamless delivery lies a complex system facing mounting challenges—power-hungry equipment, inconsistent temperatures, and ageing infrastructure. A quiet revolution is underway as demand for fresher, faster, and greener solutions grows. Across India, innovators are blending AI, IoT, and solar power to transform cold warehouses into smart, sustainable hubs. This is the story of how technology is not just cooling goods, but shaping a better, more resilient future for all.
The demand for temperature-sensitive goods is continually rising. The story highlights how businesses can build a more sustainable future. By leveraging innovations, companies can reduce their carbon footprint, maximise operational efficiency, and contribute to the global push for environmental responsibility. The next revolution lies in harnessing greener solutions such as solar energy and advancing power sustainability. Embracing digitisation across operations will simplify processes, reduce the carbon footprint, and minimise waste.
Since long-term viability means adopting cleaner energy and responsible resource management, the focus must shift toward future-ready, sustainable practices.
Sustainability and challenges of diversity
Promoting sustainability in cold storage is critical, yet the sector faces multiple challenges in India and globally, as highlighted by Ms. Debjani Nandy, Chief Executive Officer of Siddhi Cold Chain. One significant issue is the varying temperature requirements for food and pharmaceutical products. While larger storage facilities have been suggested as a solution, they are effective for uniform, commodity-based products. In reality, the diverse nature of items calls for smaller, specialized cold storage chambers. These segmented chambers can maintain various temperature zones and store different types of products safely, preventing compatibility issues.
Compatibility concerns exist, too, as pharmaceutical products cannot be stored alongside food items, and non-vegetarian goods should not be mixed with vegetarian ones. Certain products, like ice cream, also pose unique challenges, as they risk contamination or odour transfer when stored alongside other goods.
The growing demand for quick commerce, e-commerce, and the QSR (Quick Service Restaurant) sector further complicates cold storage needs. As Ms. Nandy points out, various products must be stored under one roof, each requiring precise storage conditions. This growing complexity calls for innovation across warehousing and the entire cold chain.
Innovations
Mr. Yogesh Sood, Deputy General Manager of North Carrier Transicold, observes that consumer eating habits—such as the growing preference for fresh dairy products—have impacted the supply chain. With milk products offered in multiple varieties and often with limited shelf lives, the need for rapid, efficient cold storage has grown. As demand for daily fresh offerings increases, providing solutions to these evolving needs has become even more challenging.
In response to these challenges, Ms. Nandy suggests that cold storage facilities must evolve, similar to cold chain transport, which has embraced compartmentalised vehicles for transporting incompatible products. She notes that the future of cold storage lies in creating multi-chamber setups—modular cold rooms or vertically arranged micro-warehouses—that can handle the diverse requirements of today’s products. Mr. Sood further explains that cold storage is no longer just about long-term preservation; the duration products stay in storage has drastically reduced, with many items staying only two to six hours before being dispatched.
Thus, the focus has shifted towards creating efficient, adaptable cold storage solutions that cater to the increasing variety of perishable goods in today’s fast-paced market.
Ageing infrastructure
Given increasing demand for temperature sensitive goods, Ms. Debjani touches upon the growing relevance of cold stores in India. These facilities manage large volumes of diverse products. This trend is expected to expand into tier-2 and tier-3 cities, in line with India’s shift towards a digitally connected Bharat. However, Dr Nitin Goel, CEO of Inficold, emphasises a critical gap in the cold chain sector i.e., the lack of technical standards. He illustrates this by pointing out that the same type of compressor used in air conditioners 25 years ago is still used, showing little progress. This absence of standards has serious consequences: outdated refrigerants like R22, which are harmful to the ozone layer, are still in use, and the Coefficient of Performance (COP) remains poor. Standardisation could immediately improve COP by up to 30 percent, improving energy efficiency.
He highlights inefficiencies. Major Indian companies use the same compressor for milk coolers and cold storage units despite the vastly different requirements. In cold storage, condenser sizes are often 30 percent smaller, leading to inadequate performance and higher energy costs. This happens because standards exist for milk coolers but not cold storage, creating a complex system design and efficiency situation.
Multipurpose cold storage
Tapas emphasised the growing trend in other countries of building multipurpose cold storage. These accommodate varying temperature needs—for instance, maintaining 10°C, 0°C, or even 15°C based on the type of commodity stored.
Sharing his observations from visiting numerous cold storage globally, Mr Tapas Kumar Haldar, Assistant Vice President of Bry-Air Asia, highlighted that most people focus primarily on the initial investment when setting up cold storage facilities rather than considering the long-term lifecycle cost. As Mr. Amit Sharma, Chief Business Officer of Indicold pointed out, proper attention must be given to the quality of panels used in construction. While the upfront cost may be slightly higher, it significantly reduces ongoing operational expenses. Unfortunately, many prioritise lower initial costs and end up heavily on energy bills later. Since certain products are not stored year-round, the ability to adjust temperatures allows the same facility to be used for different goods at different times. This flexible approach improves sustainability. This helps in reducing energy costs, vital for long-term efficiency.
Operational efficiency of cold storage
Mr Amit explains that doors and thermal insulation play a crucial role in improving the efficiency of cold storage operations. Larger doors allow more air exchange between different temperature zones, which reduces efficiency. As a result, cooling systems have to work harder and run longer to maintain the desired temperature, increasing energy consumption.
Compared to a traditionally designed warehouse of the same size, their energy consumption has dropped by 25 percent. For instance, the average electricity cost for a mezzanine floor facility is about ₹250–₹300 per metric ton, while they have brought it down to under ₹200. In international single-chamber cold storage units with capacities of 45,000–50,000 pallets, the electricity cost per pallet can be as low as ₹75–₹80. This level of efficiency is a game changer. It translates into potential savings of nearly ₹200 per pallet compared to conventional setups.
In today’s competitive landscape, business’s dominant driver is cost efficiency. Customers now expect a baseline of quality and service but are primarily motivated by competitive pricing. As Amit points out, companies recognise that merely passing costs onto customers isn’t a sustainable path to profitability. This is exemplified in the advice from the Thyrocare founder: sustainable growth is achieved by streamlining operations and improving system efficiency rather than charging more.
This focus on efficiency is echoed in the efforts to adopt renewable energy solutions in areas such as cold storage.
Solar power in Cold warehouses
Dr Nitin explains that while solar integration in larger cold storage facilities is typically handled via net metering, smaller operations ranging from 10 to 200 metric tons often rely on off-grid systems. India has even pioneered this model by incorporating solar-powered initiatives into a nationwide subsidy program at the Farmer Producer Organization (FPO) level, with around 1,500 installations in remote areas.
The challenge, however, lies in the current policy. Despite the clear cost advantages and environmental benefits, a significant disconnect exists in government energy subsidies. For example, while a 75 percent subsidy is available for diesel-powered milk coolers, similar support does not extend to solar-powered or thermal storage alternatives—in fact, these cleaner technologies are not permitted at all in some cases. This discrepancy creates a major barrier, especially for smaller systems that could benefit the most from adopting such sustainable solutions.
In essence, both market competitiveness and sustainable technology integration hinge on efficiency. Businesses today must optimize their systems to reduce costs and improve profitability, a philosophy that aligns with the drive towards more efficient, eco-friendly technologies in cold storage. Overcoming policy barriers and re-aligning subsidy structures to support renewable energy options could be a crucial step towards enabling these smaller systems, which could benefit the most from solar integration.
Automation solutions
Automation solutions, especially those involving IoT-enabled sensors, further amplify this push for efficiency. These technologies enhance supply chain visibility and reliability, providing real-time data that enables proactive decision-making. As Yogesh Sood highlights, industries like e-commerce, where every vehicle and shipment must be tracked in real time, rely heavily on such tools to minimize customer rejections and ensure timely deliveries.
He notes that while many transporters compete primarily on pricing, they often fall short on the operational performance that e-commerce giants require. Therefore, businesses increasingly focus on minimizing material rejections and maintaining greater control across the cold chain by integrating digital monitoring systems. These include GPS tracking, temperature sensors, and cloud-based analytics platforms that collectively ensure product integrity, reduce losses, and support sustainability goals.
By combining green energy solutions with automation and IoT, cold chain businesses can achieve powerful synergy—maximising efficiency, reducing environmental impact, and maintaining moisture control over the entire supply chain process in an increasingly demanding market.
Predictive maintenance
Tapas states moisture is a major challenge when targeting sub-zero or zero-degree conditions. If we can control this moisture, we can reduce energy consumption. Even when we maintain room temperatures of 4°C or 5°C, moisture still enters the space—especially during product loading and unloading. This moisture eventually finds its way into the cold storage area and causes issues with the evaporator coils. Frequent defrosting becomes necessary, which increases energy usage.
If we can create a moisture-controlled environment, the overall efficiency of cold storage systems will improve. We have implemented such solutions in India and neighbouring countries, particularly for ice cream storage applications. These facilities often face substantial issues due to high moisture and humidity levels. Ice cream cold storage typically maintains temperatures around -25°C; excess moisture leads to heavy icing. This affects energy performance and damages packaging materials, making it a serious concern for operations.
Preventive maintenance, supported by IoT and data analytics, can reduce energy consumption by ensuring timely upkeep and avoiding equipment failures. However, the cold chain industry in India faces challenges due to a lack of skilled workforce—mainly because the sector has seen more growth in the past decade than in the previous 40–50 years combined.Addressing this skills gap through training and education is vital. As supply chain and cold chain management gain importance, educational institutions and MBA programs introduce specialised courses. This will help develop a future-ready, trained workforce capable of efficiently handling perishable goods—supporting operational excellence and sustainability.
Operational efficiency with sustainability
Ms. Debjani notes that operational efficiency is essential. As highlighted by Mr. Haldar, sustainability is equally crucial in today’s context. Small but impactful improvements, such as those suggested by Amit regarding tunnel doors, can help considerably. For instance, using separate doors for routine movement of personnel and pallets while reserving larger doors for moving palletised goods into chambers can optimise operations. Additionally, installing air and strip curtains can help maintain temperature differences between the dock area, anteroom, and cold chambers, enhancing energy efficiency. These measures contribute to overall operational efficiency.
Conclusively, emerging tools, technologies and insights are set to improve cold storage and warehousing systems by optimising efficiency, improving product quality, lowering operational costs, and promoting sustainability. To tackle these challenges, collaboration among industry leaders is essential. With its accelerating growth and innovative capabilities in this sector, India is well-positioned to take a leadership role on the global stage. While challenges such as high energy and water usage remain, several solutions are already in place, and innovations will continue to occur over the next decade to drive improvements. The government will take the initiative for solar and thermal energy storage and introduce subsidies to encourage their development and adoption.
We know that solutions already exist globally. However, we must recognise that not every technology can be directly adopted in the Indian context. That is why we must educate customers and offer them the right solutions customised to their needs. Finally, the responsibility to bring about change rests with stakeholders and professionals, who must bring change to existing systems in a phased manner.
====
Dr Nitin Goel, Chief Executive Officer, Inficold
Establishing clear technical standards for cold chain equipment is essential to improve efficiency. Simultaneously, subsidy policies must be reformed to promote solar and diesel-free technologies.
Mr Yogesh Sood, Deputy General Manager, North Carrier Transicold
Automation solutions, such as IoT-enabled sensors for digital monitoring, are improving supply chain visibility, which is beneficial for industries like e-commerce to monitor every vehicle in real time.
Mr. Tapas Kumar Haldar, Assistant Vice President, Bry- Air Asia
We can reduce energy consumption by controlling moisture in sub-zero or zero-degree conditions. By creating a moisture-controlled environment, we can improve the efficiency of cold storage systems.
Ms Debjani Nandy, Chief Executive Officer, Siddhi Cold Chain.
Industry leaders must collaborate to find viable solutions for evolving challenges since India, with its rapid development and innovation in this space, has the potential to lead globally.
Mr. Amit Sharma, Chief Business Officer, Indicold.
The ability to adjust temperatures for different products enables the same facility to serve multiple purposes across seasons. This flexible approach improves sustainability and reduces energy costs for long-term efficiency.
Cookie Consent
We use cookies to personalize your experience. By continuing to visit this website you agree to our Terms & Conditions, Privacy Policy and Cookie Policy.
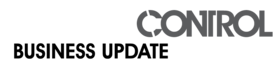