Gaurav Sharma, Strategic Business Unit Head, says Thermax’s O&M process is built on a foundation of operational excellence and digital innovation. Our structured approach begins with plant assessments, allowing the identification of performance gaps and energy optimisation opportunities. With over twenty years of experience in O&M, Thermax delivers technical excellence and helps industries achieve their sustainability and profitability goals.
How does Thermax leverage AI to improve energy efficiency and reduce industry operational costs?
Thermax leverages AI-powered tools and deep industry expertise to deliver smarter, more efficient operations. At the core are predictive analytics and dynamic benchmarking, enabled by 100+ fault trees developed by Thermax’s veterans from design, engineering, and O&M backgrounds.
These tools are already helping 20+ power plants predict failures early and ensure optimal efficiency at varying loads, reducing unplanned shutdowns and boosting performance.
Paired with real-time monitoring through IoT and cloud-based systems, operators receive instant alerts and actionable insights. This enables proactive issue resolution, remote supervision, and smarter decisions, all contributing to reduced operational costs, improved uptime, and enhanced energy efficiency.
How do predictive maintenance and real-time monitoring technologies improve uptime?
Predictive maintenance uses data analytics and machine learning to predict equipment failure, enabling timely maintenance before issues arise. Unlike traditional methods, it focuses on the equipment’s actual condition. Predictive maintenance and real-time monitoring technologies help improve uptime by continuously tracking equipment performance through sensors that monitor parameters like temperature, vibration, and pressure. Using data analytics and AI, these systems detect anomalies and predict potential failures before they occur. This enables timely, targeted maintenance, avoiding unexpected breakdowns and minimising unplanned downtime.
By focusing on actual equipment conditions rather than fixed schedules, predictive maintenance also helps optimise resource allocation, reduce maintenance costs, and extend asset life, ensuring smoother, more reliable industrial operations.
How does Thermax’s O&M process improve the availability of utilities like steam, and compressed air 24/7?
Thermax offers end-to-end O&M services for utility equipment, ensuring 24/7 power, steam, compressed air, and water availability tailored to customer needs. Backed by deep engineering and EPC expertise, our skilled teams integrate safety, digitisation, and predictive maintenance to drive uptime and efficiency. Using real-time monitoring, we detect early-stage issues like steam leaks, power dips, or compressor inefficiencies for swift resolution and zero unplanned shutdowns. Our condition-based maintenance extends equipment life, reduces costs, and ensures peak performance. With over 1000 MW of power plant assets under management, Thermax is a trusted partner for its customers, offering reliable, sustainable utility operations.
What challenges do industries encounter in maintaining equipment, and how do your O&M services address them appropriately?
Maintenance is critical in sectors such as power, manufacturing, and other heavy industries, where unplanned downtime can lead to significant financial losses, reduced productivity, and, in some cases, safety hazards.
We support industries in addressing various O&M challenges to ensure seamless operations and improved efficiency. Ageing equipment often leads to higher wear and tear, resulting in energy inefficiencies and frequent breakdowns. To combat this, we offer comprehensive asset lifecycle management, assisting with timely upgrades or replacements to maintain reliability and performance. Further, with the growing shortage of skilled personnel, maintaining industrial equipment requires a workforce capable of handling complex tasks. Our expert teams bring deep expertise in O&M, providing skilled technicians and tailored training programmes to ensure maintenance teams are equipped to manage complex issues.
Amidst increasing cost pressures, many industries resort to manual or scheduled compliance checks for their equipment. Our O&M services are curated to conduct timely checks and undertake precautionary maintenance to ensure that the plant functions optimally.
Moreover, to address the issue of inconsistent maintenance practices, we implement data-driven maintenance strategies that ensure that equipment is maintained based on actual condition, optimising uptime while avoiding unnecessary maintenance.
How can waste heat recovery and optimisation technologies contribute to reducing energy costs?
Waste heat recovery systems capture residual heat and convert it into energy. This provides avenues for reducing dependence on fossil fuels and reducing costs. These technologies help improve energy efficiency and reduce environmental impact by recycling energy that would otherwise be wasted.
There are some solutions to ensure waste heat recovery and optimisation, which can reduce energy costs. Waste heat recovery systems, such as HP heaters and heat pumps, capture heat that would otherwise be lost and repurpose it for various applications like heating, cooling, or even generating electricity. This process reduces the need for additional energy input and improves overall energy efficiency. Technologies, including HP heaters, heat pumps, dump condensers, and absorption chillers, convert waste heat into usable energy, thereby enhancing the entire system’s efficiency. Further, the recovered heat can be used to preheat fluids or air in industrial processes, decreasing the need for fuel to generate the required temperatures.
By using waste heat, industries decrease their reliance on fossil fuels, leading to cost savings and improved sustainability.
How do you strategise tailored offerings to suit different industries’ energy needs?
O&M servicing is all about tailor-made offerings. There is no standard way of operation for an O&M business. It is all about customer needs and preparing solutions. Thermax has over two decades of experience providing O&M solutions and boost of a renewal percentage of over 90%. Thermax’s O&M services provide typical manpower and also provide the manpower as a byproduct of the solution. For e.g., if a plant is not running at the optimum efficiency or has problems either identified or unidentified, Thermax O&M services will prepare a programme addressing the problem by putting together a team of experts for 5-7 days to look at problem identification and resolution to customer satisfaction. The outcome of the resolution will be an O&M service offered with guarantees.
Please briefly talk to us about a few projects undertaken in India.
We have had the privilege of serving customers across various industries, including cement, textiles, and food & beverage. Our primary focus has been on providing consistent O&M services. We began offering O&M services over two decades ago, and a leading cement company that partnered with us 20 years ago is still with us today, relying on our support to operate its plants.
This year has been particularly exciting for our Value-Added Services. We have worked on projects, including the plant assessment of a 660 MW facility for one of India’s largest industries, a chemical plant restoration, and the dismantling, relocation, erection, and commissioning of an entire power plant from one state to another. We have also managed the load distribution of multiple boilers and turbines, ensuring zero wastage of steam and power for an alumina industry client. Throughout these projects, we have consistently delivered exceptional results to our clients.
How does Thermax align its services with sustainability goals?
Thermax aligns its services with sustainability goals by offering solutions that help industries achieve their ESG targets. Our O&M division has a dedicated Value Added Services (VAS) wing, providing energy optimisation offerings like Load Management Systems, plant and system upgrades (electrical, control and instrumentation, boiler capacity), microturbines, and heat recovery solutions such as heat pumps, high-pressure heaters, etc.
We focus on enhancing energy efficiency, reducing waste, and optimising resources. Through predictive maintenance and real-time monitoring, we help lower energy use, minimise downtime, and extend equipment life. Our waste heat recovery technologies enable energy reuse, cutting carbon emissions and operational costs. These initiatives support industries in meeting ESG standards while driving long-term sustainability.
What are future strategies for expanding your business?
The next decade is a decade of services. The next decade will see a surge in demand for comprehensive services like O&M, R&M, upgrades, spares, and value-added solutions in India’s evolving power sector. Thermax is positioned to lead in the value-based services segment, leveraging our expertise in design, engineering, manufacturing, and O&M. Our research shows strong demand for reliable O&M in process plants, particularly in steel and distillery industries where we have already secured initial orders. Thermax is uniquely qualified to serve as a trusted O&M partner, aiming to double our service revenue within the next 3-5 years.
Cookie Consent
We use cookies to personalize your experience. By continuing to visit this website you agree to our Terms & Conditions, Privacy Policy and Cookie Policy.
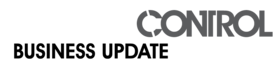