Modern MEP guidelines are integral to sustainable construction, harmonising energy efficiency with green building practices and reducing greenhouse gas emissions. Key advancements include the integration of IoT for real-time monitoring, energy-efficient designs, and renewable energy sources like solar power. Improved controls and predictive maintenance systems are also helping to optimise energy usage and achieve net-zero goals.
MEP guides in advancing green building practices and designing environmentally friendly HVAC systems. The MEP systems are designed to optimise the energy performance of a building, reducing its overall energy consumption and greenhouse gas emissions. The convergence of MEP guidelines with the principles of green architecture aims to reduce the environmental impact of buildings.
Green buildings and greenhouse gas emissions
Solar panels and building simulation are becoming increasingly popular among homeowners. Solar panels are expected to become more prevalent. Building simulation can be achieved through various applications for thermal comfort. Mr. Dipak Ganpat Babrekar, Chairman and Mentor at Benchmark MEP Engineering Consultancy, says the goal is to achieve a net-zero building by 2070 – a significant step towards becoming carbon-zero. This goal has to be reached by 2050, noting that the HVAC sector is one of the contributors to energy consumption. By 2070, energy consumption will decrease due to the increased use of electrical energy. Therefore, it is crucial to start implementing these technologies today. The parameters of a business’s design and construction are well known to all designers and organisations involved. Mr. Sandeep Rane, Director of Sheetal Academy, adds that maintaining a good design and regular maintenance, including energy and waste audits, is crucial.
Mr Himanshu Sirohi, Manager – MEP, Lodha, believes that MEP design has taken center stage in shaping the future of construction. The significance of MEP design lies in its ability to optimise building performance and occupant comfort. Without proper MEP design, buildings would lack functionality, efficiency, and safety. The importance of MEP engineering also lies in its ability to integrate these systems seamlessly into a building design and construction process for thermal comfort.
Thermal comfort control
MEP focuses on integrating energy-efficient HVAC systems that optimise thermal comfort while minimising energy use. It involves equipment, such as high-efficiency heat pumps, variable air volume systems, and advanced controls that adjust to occupancy patterns and external conditions. Thermal comfort in built-environment settings involves metabolic clothing, insulation, and air circulation rates. It aims to determine the amount of fresh air and temperature, with a range of 50–80 degrees Celsius, which can be adjusted to meet thermal comfort requirements in lead.
Ms Prabhavathi noted that when it comes to controls, one can achieve thermal comfort design by following ASHRAE 55, which will help to earn design credits easily. The controls should be there at every workstation. Collaborative spaces such as conference and meeting rooms should also have individual controls. If there are ten meeting rooms in an office, each room must have its own thermostat or remote control. Complying with these requirements and a thorough analysis can secure the necessary credits.
Life cycle analysis assessment
The design helps to assess the environmental impact of HVAC systems throughout their lifecycle -from manufacturing and installation to operation and disposal -to identify opportunities for improvement and sustainability. Technological advancements, regulatory requirements, and the growing awareness of environmental sustainability drive the MEP guidelines. Initially, MEP systems focussed on functionality and safety. However, as energy costs rose and the ecological impact of buildings became more apparent, the emphasis shifted towards efficiency, sustainability and assessment. Mr. Raji R Panicker, GM Engineering – Adani, Navi Mumbai International Airport, highlights building life cycle assessment analysis offers insights into the potential for reuse and recyclability, especially in scenarios where scrapped materials and reused products are evaluated. A net present value analysis is conducted at the end of a product’s life cycle to assess its significance in commercial decisions. It uses NPV or LCCA software, with NPV being more useful for Excel sheet use. Comparative studies are necessary for the equipment to determine its impact on carbon emissions, which is crucial for green building projects.
Energy efficiency
Energy efficiency is a cornerstone of modern MEP guidelines and green building practices. MEP systems optimise the energy performance of a building, reducing its overall energy consumption and greenhouse gas emissions. When a designer designs a system, the operation team maintains its functionality. The design team must adhere to the operation and maintenance manual, which depends on the skill. Outsourcing is not an issue, as the operation team assumes the system is fully operational. A standard operating procedure (SOP) is necessary to address maintenance issues, and the design and operation team should work together to ensure the system’s functionality. This collaboration can improve the operation’s efficiency and the product’s life cycle. Therefore, both parties must understand and address maintenance issues.
Green building standards and air quality
MEP systems into green structures require adherence to recognised green building standards and certifications. These standards provide a framework for designing, constructing, and operating sustainable buildings. Two of the most widely recognised green building certifications are Leadership in Energy and Environmental Design (LEED) and Building Research Establishment Environmental Assessment Method (BREEAM). LEED certifications recognise buildings for sustainable features, including energy efficiency, indoor air quality, and water conservation, influenced by MEP design choices.
In green buildings, there are no direct points or credits for co-generation in LEED or A green factory certifications. However, energy simulation tools can help take advantage of energy reduction due to co-generation. It is achieved through boiler systems, pressurised air, or water for chillers. However, as a directory, you do not earn any points. Ms Prabhavathi is categorical in stating that a provision can take advantage of energy savings through optimised energy performance credit. It helps in achieving green building certifications. By documenting this data, one may approach the LEED, IGBC, or GRIHA teams to show the benefits of our system in terms of green building compliance. Although there is no direct control over these standards, feedback to these bodies must be provided by submitting validated data for assessment.
Consultants should know their respective subjects, such as architecture and MEP. They can help reduce lighting, power density, and chiller consumption and improve performance in hybrid chiller systems. By integrating these subjects and setting a specific EPI target, consultants can work on the best industry standards, leading to better designs and reduced operational costs. This approach can also help reduce capital investment and profit in terms of operational costs. Therefore, it is crucial to have knowledgeable consultants in these areas. Mr. Himanshu remarks MEP design is central to optimising performance and securing LEED certification that promotes sustainable design and construction practices.
Designing Cost
The cost of implementing an energy-efficient HVAC system can be balanced to conserve energy consumption. Mr. Dipak says clients often come to MEP consultants seeking tailored designs based on their specific demands and requirements. They may need to be made aware of options such as gold, silver, or platinum. To create awareness, consultants must first understand the client’s preferences and input on the design. They must also consider the site conditions, capex and opex strength, and the client’s budget.
The cost of designing is directly proportional to the capital cost, which is visible during the payback period. The OPEX is a factor in determining the capital cost. Clients may not realise the significant capital costs associated with building management. By understanding the client’s needs and preferences, consultants can create a more effective and cost-effective solution for their clients.
Green building compliance and energy-efficient systems often result in higher costs for equipment and systems. However, consultants add safety factors and costs based on factors like the number of people, efficiency, and temperature. This can lead to increased system size. Ms Prabhavathi thinks that to optimise design, a consultant should rely on data and energy simulations to determine the anticipated energy consumption when the building becomes live. This allows them to consider additional safety factors and reduce capital costs.
For example, a chiller with a coefficient of performance (COP) of 6.0 is 30–40 percent more expensive than a chiller with a COP of 6.5. By optimising the size of the system, the cost can be balanced compared to conventional and energy-efficient buildings. However, it is essential to remove safety factors or cushion factors from the budget, as they can impact the overall cost of the building. By focussing on data-driven optimisation, consultants can better balance the benefits of green building compliance and energy-efficient systems while minimising the impact on the budget.
IoT benefits in real-time monitoring
Monitoring is vital to saving money. Observing various projects, it is evident that key performance indicators (KPIs) should be given to the right team, like sales for sales team performance. Ms. Prabhavathi asserts a metering system is crucial for monitoring and determining the performance of a building. A cloud-based integrated building management system to help building owners and project managers identify areas of gaps in their projects. Proper metering systems can help identify specific power points, such as lighting or office spaces. The building’s lifespan should be 60 years. Therefore, it is essential to monitor buildings and metering systems. Without a cloud-based system, people may not take it seriously, and the performance of all systems, including chillers, lighting, and electrical, may degrade.
Future trends
Efficient MEP design optimises energy consumption, reducing operational costs and improving building sustainability. Himanshu says that with the increasing focus on environmental conservation and energy efficiency, MEP engineers play a role in implementing innovative technologies and strategies to minimise buildings’ carbon footprint. This includes integrating renewable energy sources, Smart building automation systems, and energy-efficient equipment and appliances. MEP can further enhance the sustainability of HVAC operations by using renewable energy sources and lowering greenhouse gas emissions.
While MEP systems with green building practices offer numerous benefits, it also presents challenges. These include the need for specialised knowledge and skills, the cost of implementing advanced technologies, and the complexity of coordinating multiple systems.
Mr Raji R Panicker, GM Engineering – Adani, Navi Mumbai International Airport Pvt. Ltd.
Building life cycle assessment analysis offers insights into the potential for reuse and recyclability, where scrapped materials and reused products are evaluated.
====
Mr. Sandeep Rane, Director, Sheetal Academy.
Awareness of energy efficiency is limited, making it essential to maintain good design practices.
Ms. Prabhavathi, Partner, Conserve Consultants Pvt. Ltd.
There is a provision through optimised energy performance credit to take advantage of energy savings that help to achieve green building certifications.
Mr. Dipak Ganpat Babrekar, Chairman and Mentor, Benchmark MEP Engineering Consultancy.
Prioritising operation and maintenance in HVAC will help determine future energy consumption.
Mr.Himanshu Sirohi, Manager – MEP, Lodha.
MEP design is central to optimising performance and securing LEED certification that promotes sustainable design and construction practices.
Cookie Consent
We use cookies to personalize your experience. By continuing to visit this website you agree to our Terms & Conditions, Privacy Policy and Cookie Policy.
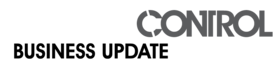