Leaders of cold chain warehousing supply chain discussing the variables that is evaluating the technological addition to the industry to create a viable and better supply chain for Indian market.
With fast growing consumer market in India, there has been a fundamental shift in the industrial warehousing and logistics services in the last couple of years. Albeit, food and beverage industry registering multifold growth and creating ample opportunity for the stakeholders.
Nevertheless, warehousing and logistics industry is still at nascent stage and looking forward to shape up. In this, cold chain warehousing industry has a very important role as India is the largest producer of fruits and second largest producer of vegetables in the world. However, despite having been the largest producer, per capita availability of fruits and vegetables is quite low in the country because of post harvest losses which account for about 25 per cent to 30 per cent of production. Besides, quality of a sizable quantity of produce also deteriorates by the time it reaches the consumer.
According to Akash Agarwal, Director, Crystal Logistics, the estimated annual production of fruits and vegetables in the country is about 130 million tones. This accounts for 18 per cent of country’s agricultural output. Due to diverse agro climatic conditions and better availability of package of practices, the production is gradually rising. “Although, there is a vast scope for increasing the production, the lack of cold storage and cold chain facilities is becoming major bottlenecks in tapping the potential. The cold storage facilities now available are mostly for a single commodity like potato, orange, apple, grapes, pomegranates, flowers, etc. which results in poor capacity utilisation,” says Agarwal.
Prospective rise
The Government of India has shown great level of interest in this regard especially to support the agricultural sector. ‘Operation Green’ which was proposed in this year’s budget has allocated a fund of `500 Cr to promote Farmer Producer Organisation which would include agricultural logistics and primarily cold chain infrastructure. A similar thrust is also needed in overcoming the challenge of defining standards and protocols in handling the operations of a wide array of finished products and raw produce that make use of cold chain as a vital component of the value chain. FSSAI has played an active role in defining the standards for a multitude of products thus opening up new sectors for cold chain warehousing and transportation.
Globally, the F&B sector is expected to grow with the emergence of economies and increase in purchasing power in the developing countries. Consumer focus is shifting towards healthier options with responsibly sourced ingredients thus increasing the need for preservation across the value chain. Governments across the globe are focusing on introduction of standardised labeling on food and beverage packaging. In addition, consumers have become more conscious of ingredients and labeling as a result of recent scandals in this industry.
With global sourcing, comes the challenge of managing a multi-country, multi-modal supply chain while ensuring temperature adherence across all links of the value chain. There is hence a growing demand for alternate solutions such as thermal covers or blankets, eutectic plates and non fossil fuel based technologies that can sustain temperature under extreme conditions for longer durations of time.
The challenges of the cold chain industry are unique to the country mainly on account of the cost consciousness in industries that use the services and the highly unorganised nature of the sector as a whole. “Generating interest to increase investments in temperature controlled infrastructure such as Freezer rooms, CA cold stores, Ripening chambers, Transportation vehicles, etc. is one of the crucial challenges that needs to be overcome,” says Anand Sen, Business Head, Express and Temperature-Controlled Logistics, FSC.
According to Aditya Vazirani, CEO, Robinson Logistics Solutions, the industry at a completely nascent stage at the moment with only a handful of LSP who can offer integrated temperature controlled services in India; on the global horizon it is a completely different picture entirely where there are companies who have enormous capabilities and offerings in terms of location and scale. “There is a definitive scope for growth in the Indian market itself as we have the population to drive demand and quality!” said Vazirani.
Way forward
The need of the hour is to increase the investments in cold chain infrastructure and to ensure uniform distribution of these assets across the country. There have been numerous state and central level subsidy schemes that provide up-to 35 per cent support on the capital expenditure or support at the interest rates thus making ROCE of the investment more viable. Such subsidies help in funding the viability gap which is a major concern for most investors. An estimated investment of more than USD 150 million has been put into cold chain companies by PE firms which are expected to improve the farm level infrastructure through the development of pack houses, ripening chambers and other allied transportation services. The clearance of FDI in multi brand retail which mandates procurement from local markets is also expected to double the food processing levels and bring in world class temperature controlled infrastructure into the Indian ecosystem. “Focus of the industry will thus shift from single commodity storages to modern multi commodity facilities with the scope of consolidation and introduction of better technology thus optimising the entire supply chain,” said Sen.
The development of cold chain warehouses in India has been skewed towards single product storage of potatoes since it also contributes to about 20 per cent of agricultural revenue in this country. Most of the facilities are located in Uttar Pradesh, Gujarat, West Bengal, and Punjab thus creating a lack of storage options in the rest of the country. The lack of development of multi-commodity cold chain facilities can be attributed to multiple factors such as high real estate prices, lack of clarity on changes in land use pattern and dependence on imported technology for refrigeration. It has also been seen that the Cold chain industry consists of multiple players, of which 85 per cent are unorganised players who are unable to invest much in the technology required to build high quality cold storages along with reefer trucks. Lower margins further limit their ability to maintain quality standards and invest in growth.
Critical parameters
The essence of using an unbroken cold supply chain is to ensure that the temperature of the product is maintained at every point of change. With varying customer demands and reduction in shelf life to maintain freshness, service providers need to closely monitor critical parameters such as temperature, humidity and location of the shipment at all points of time. It is also important to maintain transparency with customers since any product level damage due to temperature abuse can lead to cascading effects across the consumption centers.
FSC has been a pioneer in the use of technology across businesses and below are some of the key initiatives taken up for monitoring and control in the temperature controlled sector:
- IoT – IoT is a key component of the temperature controlled supply chain and FSC has integrated its transport management systems, with the remote temperature and location monitoring services offered by multiple IoT companies. This provides a real time feedback of the goods in transit thus ensuring that quality is maintained throughout transit. The same can also be made available to the customers thus ensuring transparency.
- 24 x 7 Monitoring of operational aspects such as the door opening at the warehouse, loading and unloading time, transit time, etc. ensure that there is no impact on the quality of the product.
- Remote temperature management – To eliminate the dependence on drivers for temperature management in transit, FSC is in talks with OEM manufacturers of refrigerated units to develop remote temperature management technologies. This will help transfer the control over in transit temperature from the drivers to the control tower.
- Real time data monitoring and incident alerts– Customers are provided with access to our tracking systems thus ensuring high levels of transparency for goods in transit. This helps in taking immediate action in case of temperature excursions thus preventing loss of quality.
Refrigeration technology for cold chain warehousing
A cold storage unit incorporates a refrigeration system to maintain the desired room environment for the commodities to be stored. A refrigeration system works on two main principles; Vapour absorption system (VAS), and Vapour compression system (VCS).
VAS, although comparatively costlier, is quite economical in operation and adequately compensates the higher initial investment. Wherever possible such a system should be selected to conserve on energy and operational cost. However, it has its own limitations when temperature requirement is below 100C and many of the fruits and vegetables except seeds, mango, etc. require lower than 100C for long storage.
VCS is comparatively cheaper than VAS. There are three types of VCS systems available depending upon the cooling arrangements in the storage rooms i.e., diffuser type, bunker type and fin coil type. Diffuser type is comparatively costlier and is selected only when the storage room heights are low. According to Agarwal, “The operational cost of such units is also higher. Bunker type is the cheapest and is preferred when storage room heights normally exceeds 11.5 m. Its operational cost is also low. Fin coil type, although about 5 per cent costlier than the bunker type, is very energy efficient with low operational cost and higher space availability for storage of produce. Such system is used for units with room heights of 5.4m onwards.”
In a refrigeration system, refrigerants are used to pick up heat by evaporation at a lower temperature and pressure from the storage space and give up the heat by condensation at a higher temperature and pressure in a condenser. Freon used to be a common refrigerant but as it causes environmental degradation; its use is going to be banned by the year 2008. Therefore, Ammonia is being increasingly used and preferred for horticultural and plantation produce in cold storage units.
There is a vast scope for increasing the production, the lack of cold storage and cold chain facilities is becoming major bottlenecks in tapping the potential.
Akash Agarwal, Director, Crystal Logistics
Focus of the industry should shift from single commodity storages to modern multi commodity facilities for the entire supply chain.
Anand Sen, Business Head, Express and Temperature-Controlled Logistics, FSC
There is a definitive scope for growth in the Indian market itself as we have the population to drive demand and quality.
Aditya Vazirani, CEO, Robinson Logistics Solutions
Cookie Consent
We use cookies to personalize your experience. By continuing to visit this website you agree to our Terms & Conditions, Privacy Policy and Cookie Policy.
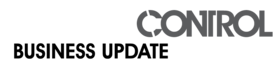