Industry’s leading refrigeration experts discuss the advantages of natural refrigerants, their cost-saving capacity towards energy efficiency and maintenance. They further discussed the challenges and solutions for shifting towards natural refrigeration.
The global refrigerant market is expected to record a value of US$19.57 billion in 2024, and the global Natural Refrigerants market size will reach 3070.0 million $ in 2025. The market is dominated by fluorocarbon refrigerants due to their increased demand for the production of AC and refrigerator units, because of their advantages of stability, non-flammability and low toxicity. Choosing refrigerants for application Natural refrigerants have GWP values as low as 10 and are cheaper than synthetic alternatives. A few notable trends may include increasing use of dehumidifiers, accelerating R&D spending for energy efficiency, rising demand for natural refrigerants and use of IoT-enabled refrigeration solutions for equipment monitoring.
According to Wilson Lawrence, Vice President & General Manager, India Engineering & Technology Center, Trane Technologies, “There are a couple of criteria when it comes to natural refrigeration and natural refrigerant and obviously,. GWP, ODP are going to be primary ones Safety measures are another important point which we have been hovering around the available standard guidelines especially during selecting a natural refrigerant. With it, we will attain strong KPIs in place to understand and ensure whether we can meet the safety standards as per the AHRI standards.” Efficiency is another vital aspect to consider in refrigeration. There are no questions or complications towards the cost, but there are challenges towards efficiency. We have been trying to address the efficiency element through several ways, by considering what if we go and adjust something towards the thermodynamic cycle of the system so that we don’t compromise too much in energy efficiency. Even the amount charge is also a bigger constraint when it comes to hydrocarbons and CO2, especially. Trane Technologies is largely into the transport business with truck refrigeration, trailer refrigeration, bus air conditioning among others, and we have been viewing CO2 turning out to be a good alternative option out there. The obvious reason is we have some challenges in terms of handling the largest volumes. So, these are some of the key KPIs we typically consider when it comes to qualifying the natural refrigerant.
Pricing and affordability factors in refrigeration industry
Price is a key parameter that comes into play, and the affordability does not rest just with price. “If you are looking to shift towards natural refrigerants then the price in itself should not be that big a constraint, but if you look at some of the other low-GWP options like HFO’s and the others then the price is definitely a factor as it is it depends on the demand in a particular region. So here, the production region, factors for imports, fluctuation of forex comes into play, but if you are looking at ammonia or a CO2 then it doesn’t seem to be a big challenge”, says Nagahari Krishna L, Director – Industry Affairs and Regional Hot Spots, Danfoss India.
If we look from an affordability perspective, it is not just the price that comes into play because when you are using natural refrigerants and you are trying to move from a particular refrigerant; like, you’re using ammonia you want to move towards a cascade system or a transcritical system. Here, efficiency also comes into the picture as it is a factor that where your design engineers has a key role to play, as in designing a natural refrigerant, and ammonia refrigerant and make it a future forward.
Safety and regulatory challenges towards natural refrigerants
Talking about the challenges for smaller applications, a lot of compressors are not available, so my imports become costlier, says Niteesh Dua, Design Engineer, Bombay Ammonia Refrigeration Company Ltd. “We have also tried smaller systems with DX systems, and they work very well but somehow for smaller systems people would go for HFCs. The reason being that ammonia would be costly as a representative over there as the system and the initial cost will become dearer.”
If we are installing ammonia system for residential buildings, then people would wonder what if there is a leakage in ammonia system. So, a lot of people install ammonia with best safe practices, but there is thought process among the people not to have ammonia installed in their residential premises as we don’t have regulatory authorities to actually monitor what is being built. This is one of the critical challenges that we face while promoting ammonia refrigeration systems in residential areas. Thirdly, sometimes people say that there could be a leakage and contamination. If the welding as well as all the standards are followed it is very rare that it leaks. In the machine room, probably yes, it does leak during maintenance but if all the international standards for welding and inspection are followed there is a very less possibility of a leak. “People today would rather like to go for CO2 with ammonia as cascade system; obviously, because CO2 cannot be used directly because the critical pressure in the air is around 320C, it is not feasible to have it on the condensing side, but they would use it as a cascade”, adds Niteesh.
Whereas, according to Krishna, the relevance of safety standards in India is very important, especially when we look at the roadmap for natural refrigerants in India. From a standards viewpoint or a regulatory and policy viewpoint, BIS (The Bureau of Indian standards) has done commendable work in this space. Today, you have adopted a lot of global standards on safety for India and they’re available for Indian stakeholders, specifically on ammonia, BIS has now drafted a safety standard for all ammonia-based applications, and I guess the new safety guidelines will soon be made available for practice.
Not just the system, but even the manpower the handler should be safe. If the plant worker says that the plant is safe, and everybody is safe, especially after you have the right skill sets in place and your killed manpower is ready to take care of the safety aspect, automatically the natural refrigerants uptake will improve.
Adding more light to the discussion, Wilson says “Bringing in standards into your products, technologies and services certainly makes us confident to ensure that our documents are secured, our people, equipment and machines are safe.” But this also increases the pricing factor and brings cost addition to the market cost addition especially in markets like India, where people highly cost sensitive, especially in the residential market spaces and many of us are already aware of that fact that India is an extremely cost sensitive market and obviously, anything towards safety is going to bring some addition to the cost. “We need to see how mindset of the people will be shifted in spending additional cost towards safety. This is going to be a critical challenge in our region, but globally, especially in developed countries, we don’t find many challenges”, Wilson adds.
Accessing quality refrigerants
“When it comes to natural refrigeration or natural refrigerants, one important parameter that we have seen is that, we see a lot of devices and solutions that are coming into play, which can help you in ensuring that you do not have too much of a loss of refrigerant that happens in the system”, says Krishna. There are systems like air purger and IoT – enabled devices and controls that help you in reducing the loss of refrigerant that happens. And if you can reduce that there are two benefits that come; you don’t lose too much on efficiency there because you continue to maintain a particular pressure in the system.
Second important thing is that you need not keep charging the system with a lot more refrigerant because you are ensuring that the refrigerant doesn’t leak out. It’s all about looking at the total cost of ownership for clients. Companies today are increasingly innovating on products and bringing those solutions into the market. But the challenge for these innovations coming into the market is leveraging the total cost of ownership for the clients rather than just looking at the upfront investment. And this challenge is with every manufacturer that is there, and we need to engage with clients on a regular basis and help them understand them.
“Since we’re talking about the quality of the refrigerant on construction sites on hydrocarbons that way, this is again absorbed in one of our tests as we know hydrocarbons can’t be used like a fuel. There are too many variations in terms of contaminations”, says Wilson. All of us know that some Sulphur components exist in hydrocarbons and how much Sulphur is reactive to materials like copper that we use in our HPC systems.
So, we have to be cautious when it comes to hiring on the quality side but I can suggest some of the standards published like AHRI 700, that’s one of the best standards which our teams have come across which nicely lists out what are all the specifications from a quality standpoint have to be followed. “So, if we were able to, you know, be very watchful in making sure those specs have been taken care of, then I don’t think so, we have much of a challenge when it comes to quality sight from the refrigerant standpoint, he adds.
Assess the efficiency among natural refrigerants
Coefficient performance (COP) is one part of the system and we can calculate the COP of system but other than that we have seen many cold storages are to say it is a 5000 metric ton cold storage, as this is a very standard cold storage in India. Niteesh explains the concept of energy-efficiency refrigeration with an example, “One of the companies has installed a HFC-based solution and we installed an ammonia-based system and the final electricity bill explained the better operability of both the refrigerants. So, the electricity bill indicates the efficiency level of your system and operations of both the refrigerants are same, their opening is same, loading system, loading pattern as both are loaded right in the beginning, and stays for a long time and then it will open. Same process is applied for a controlled-atmosphere in cold storages where similar things happen. So, in that case, the electricity bills will tell you what the difference is. Other than that, if you want to do a COP analysis, that will give you much more ideas.
Explaining the efficiency level from a larger perspective, Wilson says “We did some investigations in ammonia and it certainly took us into the low efficiency the efficiency or the efficiency advantage. To the larger extent we are trying to pick up some alternate materials which could be able to reduce the efficiency loss. Also, a lot of investigation is being made towards the component levels, where it could be compensated efficiency. They are not expansions; although quite a lot of efforts are going on to compensate not the efficiency which we are losing out of this tool so that we are able to compensate, right. We are making an adjustment in making sure that the efficiency has been taken care of to a large extent.
Niteesh further adds that if you don’t have a properly automated system in ammonia, then ammonia power can also be more than the HFC waste thing. We’re talking about copper and stainless steel as I have designed both HFC systems and ammonia-based systems. The copper efficiency is high but heat transfer efficiency of ammonia is higher. Ammonia-based evaporator and Freon-based evaporator have approximately the same sets. So, pressure drop in both the systems is approximately the same on the evaporator side. In some cases, it can be lower depending on the circuit but because heat transfer efficiency of ammonia is higher, even though we have copper which has higher conductivity to it.
Cookie Consent
We use cookies to personalize your experience. By continuing to visit this website you agree to our Terms & Conditions, Privacy Policy and Cookie Policy.
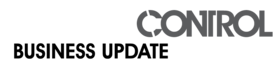