In this article, Kiran Panchal, Business Manager, Mark Compressors, stresses that it is crucial to maintain relative humidity levels below 50 percent to ensure the effectiveness of the compressed air. Optional PDP indicators are available to assist in monitoring the drying process.
In most industrial applications where compressed air is utilised, maintaining a pressure dew point (PDP) between +2°C to +8°C is essential. Refrigerated air dryers offer the best performance and are highly reliable for these applications. Regarding pneumatic applications, prioritising pressure dew point over atmospheric dew point ensures that the compressed air contains a safe and acceptable moisture level, which will be harmless to the processes.
Only a few industrial applications require compressed air with a PDP below +2°C, such as cryogenic processes or hygroscopic materials. In these cases, combining a refrigerated air dryer with an appropriate desiccant dryer is advisable. This approach reduces overall investment and minimizes the purge loss associated with desiccant dryers.
It is crucial to eliminate moisture from compressed air before it enters process machinery to prevent corrosion, rust, pollutants, and the growth of germs within your system. This ensures that your industry’s quality standards are met and minimizes the wear and tear on your process equipment. Using a refrigerated dryer enhances the efficiency of process machinery and pneumatic tools.
Refrigerated dryers serve the purpose of removing moisture and water vapour from compressed air. They are typically a cost-effective solution and are well-suited for safeguarding your process requirements and prolonging the lifespan of your system. Furthermore, modern refrigerated dryers often come equipped with built-in PDP indicators.
How does a refrigerated dryer protect equipment?
Refrigerated dryers operate by cooling the compressed air to remove moisture. During compression, the heat produced causes the air’s moisture to become vapour. When the refrigerated dryer cools the air, this water vapour condenses into a liquid form. Before the compressed air enters the process, the condensed moisture is removed. Failure to eliminate moisture from compressed air can result in corrosion, rusting, and reduced operational efficiency of your process equipment. This approach helps prevent the risk of corrosion and contamination while simultaneously enhancing the system’s overall efficiency through moisture removal from compressed air.
Operating refrigerated dryer
Refrigerated dryers operate like household refrigerators, primarily focusing on environmental friendliness by utilizing eco-friendly refrigerants to cool the hot compressed air. These dryers comprise key components, including an air-to-air heat exchanger, an air-to-refrigerant heat exchanger, a closed-loop refrigeration cycle, and a condensate drain system.
- Incoming hot compressed air is partially cooled by outgoing cold compressed air leaving the dryer.
- At the same time, the outgoing compressed air is re-heated around room temperature, so condensation does not form outside the piping after the dryer.
- Cooling of incoming air reduces the energy required by the refrigerant compressor, ensuring further power saving.
- Incoming air is further cooled down to the required PDP level at an air-to-refrigerant exchanger by an eco-friendly refrigerant.
- Water vapour in compressed air is condensed and drained through an automatic condensate system.
- Hot refrigerant is again passed through a closed-loop refrigeration cycle to transform into a cold refrigerant required for the next cycle. The equipment is quite simple and easy to operate. The maintenance and operation, too, are as easy as that of a house fridge.
Certain models incorporate advanced features such as smart condensate drainage systems, which utilise electronic sensors to remove condensate while conserving compressed air efficiently. Additionally, these models offer cost-cutting capabilities and the option of an add-on filtration system.
To ensure the effectiveness of the compressed air, it is crucial to maintain a relative humidity level below 50 percent. Optional PDP indicators are available to assist in monitoring the drying process. These devices gauge dew point, provide fan status information, and come equipped with PDP alarms.
Despite this, the installation and upkeep of a refrigerated dryer are relatively straightforward. We designed machines for durability and ease of operation, focusing on minimising operational expenses as much as possible.
Non-cycling
The market offers both non-cycling and cycling variants of refrigerated dryers. Cycling dryers regulate the dew point by cycling the refrigeration cycle on and off, which keeps the system’s PDP within a range of ± 5°C. On the other hand, non-cycling dryers continuously control the dew point, ensuring a consistent level. Non-cycling dryers are more energy-efficient because they adjust cooling based on air demand, unlike cycling dryers, which can run unnecessarily. No matter the air demand variation, a non-cycling Mark dryer will maintain a precise PDP with minimal energy consumption. This equipment is known for its simplicity, safety, and reliability.
Environmentally friendly gases
CFC content in refrigerant gases affects the environment. If the ozone layer worries you, our MDS dryer uses environmentally safe R513A, R410A and R452A gas.
Proper drainage
You must utilise an oil-water separator at discharge if your refrigerated dryer is attached to an air compressor that uses oil injection. Properly disposing of oil is paramount, especially when awareness of environmental safety concerns is a universal problem.
Furthermore, when disposing of condensate, it should be done with great care. Condensate water released from compressed air often contains traces of oil, even though these remnants are too small to be visible to the naked eye. Therefore, it is crucial to follow stringent protocols.
Never dispose of contaminated condensate on the ground or in a plastic container. It is advisable to ensure that you comply with the appropriate regulations and adhere to strict environmental management system (EMS) guidelines.
Choosing a refrigerated dryer for your air compressor
Choosing the correct capacity for a refrigerated air dryer is crucial when your application is critical. The capacity of the refrigerated dryer is influenced by factors such as the temperature of the incoming compressed air, the pressure of the compressed air, and the temperature in the compressor room.
Our compressed refrigerated air dryers are known for their reliability and ease of installation. These devices offer significant value when it comes to ensuring the quality of your processes and protecting your compressed air equipment.
When assessing equipment, it’s important to consider factors like installation, reliability, dew point performance (PDP), and the use of high-quality components. Additionally, finding the most energy-efficient option is of utmost importance.
Cookie Consent
We use cookies to personalize your experience. By continuing to visit this website you agree to our Terms & Conditions, Privacy Policy and Cookie Policy.
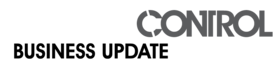