Chillers are substantial energy consumers in building operations, often accounting for 30-40 percent of a building’s energy usage. Chiller performance directly impacts operational costs and occupant comfort. This article explores practical methods for monitoring chiller performance to optimise building operating costs, emphasising the importance of regular assessments and trend analysis.
Whether a building has a water-cooled or air-cooled chiller, this equipment is critical for ensuring the comfort of the building occupants. It validates the asset operations are running at an optimal value. Chillers are the big consumers of energy in a building. With the associated auxiliary systems such as cooling towers, pumps, AHU, etc., more than 30 – 40 percent of energy is consumed by the air conditioning system in a building. Therefore, the Building Operations and Maintenance (O&M) team must manage the chiller’s operation efficiently, balancing the comfort and cooling expectations of the building occupants and the cost of running the plant. A famous management saying goes, “What gets measured, gets managed”. A key aspect of running a chiller plant is to measure the system performance so that the operators know how the system is running. Corrective actions can be taken when performance deviates from rated values. However, chiller performance measurement is difficult, as the number of components and variables is high. Following another management concept introduced by the famous management guru John Doer may be a more practical approach – “measure what matters”. This article dwells on practical approaches to measure chiller performance rather than the more advanced testing approaches defined by relevant industry standards such as ASHRAE standard 30.
Why measure chiller performance?
The design of the chiller is finalised at the building design stage. There is a long lead time between the design finalisation and the actual operations of the chiller plant, which is the construction phase in a typical new build scenario. When the chiller is commissioned, the whole system is not in place. In many instances, the chiller can not be tested to its rated load as the building is not fully ready or only a phase of the space to be cooled is operational. It may take up to a year before the chiller plant can operate to more than 80 – 85 percent capacity. There are also changes in the design of the building during the construction phase on account of changes in using the space. It directly impacts the chiller performance when the building becomes operational.
To assess how the equipment is performing, we need to know the output parameters the system should produce for given input conditions. In chillers for buildings, the input parameters are never static. There is not a clear reference when it comes to measuring how well the chiller is performing. It is necessary to find out how efficiently the chiller is operating. This is the equipment which consumes the most energy in a building. Consequently, it contributes maximum to the operating cost.
Measuring the chiller’s performance also helps the O&M team identify any underlying system faults or deficiencies, which can then be addressed. This allows the plant to run efficiently for the maximum period of time.
Practical chiller performance measurement
ASHRAE standard 30 prescribes methods for obtaining liquid-chilling or liquid-heating equipment performance test data using the vapour compression thermodynamic cycle. The ANSI/AHRI standard 550/590 lists the requirements for the Performance Rating of Water-Chilling and Heat Pump Water-Heating Packages Using the Vapor Compression Cycle. These and some other industry standards for measuring the performance of chillers provide a robust framework to measure and assess the functioning of the chiller plant. However, calculating performance using the methodology used in these standards is a complex and time-consuming process. It can not be done daily in the plant room of a building by the O& M team. These standards require stable operating conditions and external test equipment requiring specialised expertise.
A more practical approach to assess how the chiller plant is operating is for the chiller operator to measure key plant parameters and compare them to the values provided by the OEM. And, basis the general working experience the team has of the plant in those operating conditions. Some parameters that an operator should effectively track and analyse are – Condenser approach temperature – This is the difference between the temperature of the refrigerant in the condenser and the temperature of the water leaving the condenser. The higher the approach, the poorer the heat transfer that is occurring. It indicates the scaling of the condenser tubes or an ineffective cooling tower. The recommended approach is between 2- 4 degrees centigrade. However, this will also depend on the load. The operators should be aware of the approach to typical loading patterns in the building.
Energy drawn—Modern chillers have a relatively advanced chiller control system that can display the energy and the cooling load at any given point. Close monitoring of the chiller’s energy usage for given load patterns can help identify potential deviations from its design parameters. A worn bearing may result in a higher current drawn, and early fault diagnosis can prevent a major breakdown as well as costly repairs.
Chilled water outlet temperature: The chiller set point is one of the most important parameters that the plant operator should monitor, as the value gives a high-level view of the chiller’s performance. The typical set point is between 7 and 9 degrees centigrade.
Each of the above parameters indicates how effectively the chiller is operating. The OEM data book will provide values for these parameters at different operating loads, and comparing the actual values with the design values will give the operator an idea of how the plant is performing. When there is a deviation from the design values, operating parameters such as refrigerant temperatures, compressor speed, and loading patterns can be evaluated. This leads to the identification of the root cause of the deviation.
Daily observation and monitoring of the parameters may not yield significant insights into the chiller performance, especially when the change in parameters is incremental or marginal. A more effective approach is to undertake a weekly or monthly trend analysis of the critical parameters of the chiller plant. It involves plotting the identified parameters and observing any changes ( increasing or decreasing trends) at similar operating conditions. For example, observing the condenser approach and energy consumption at the peak load time of 1300 hrs over a month will give an insight into how the plant operates at peak load. If the condenser approach shows a minor upward slope, it indicates the beginning of the fouling of the condenser tubes or a problem with the cooling towers.
Challenges in operational performance measurement
Knowing what to measure and when is often the most complex part of performance measurement. A chiller has numerous parameters, all critical and reflective of the functioning of the plant. Since the chiller plant is an integrated system, all sub-systems are connected, and anyone not operating optimally will affect the overall plant performance. It is impossible to measure and monitor all parameters to the same level except when a BMS system is doing this task. The practical approach is to measure the key outcomes as these are a summation of the operational state of the sub-systems.
Another challenge to performance measurement is the reliability of the measurement instruments. Due to the rough environment that most chiller plants operate in, the reliability of the sensors that measure the key parameters is not always very high. Pressure gauges may not show the correct values, temperature sensors’ sensitivity may deteriorate due to local environmental conditions, etc. Thus, it is important to regularly calibrate the measurement sensors and equipment.
Conclusion
Building O&M teams typically rely on the Annual Maintenance Contract (AMC) supplier to undertake annual chiller performance tests. It includes the calculation of the IKW and testing the system to assess conformance with design parameters. While this yearly test will give insights into the chiller’s performance health, any degradation occurring during the plant’s operation may lead to the system operating at off-design points for prolonged times, resulting in higher operating costs. Thus, operators should continuously monitor performance using a few key parameters and undertake trend analysis regularly to identify potential off-design operations. This will help reduce operating costs and prolong the life of the asset.
Expertise shared by-
Aneesh Kadyan
Senior Executive Director, Property Management Operations
CBRE South Asia Pvt Ltd.
Cookie Consent
We use cookies to personalize your experience. By continuing to visit this website you agree to our Terms & Conditions, Privacy Policy and Cookie Policy.
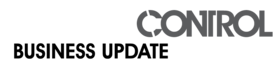