MFG Chemical, a global leader in specialty and custom chemical manufacturing, is improving its manufacturing capabilities in Dioctyl Sodium Sulfosuccinate (DOSS) through the upgrading of its three Dalton, Georgia plants.
Project Odyssey is name given for upgrading MFG Chemical’s Dalton plants. DOSS is a specialty surfactant used in oilfield, lubricants, ethanol, coatings and agricultural industries, as well as polymerization, paints and inks, pulp and paper, resins, textiles and carpets, rubber, metals and minerals, petroleum oils and dry cleaning applications.
As a specialty chemical manufacturer, Project Odyssey has already improved our industrial chemistry management systems in the areas of safety and compliance. Joe Welch, Director of EHS&S, and Fred Carder, Mechanical Systems Manager, work together to assure all engineering and compliance aspects of Project Odyssey are being implemented on schedule. Welch stated, “DOSS is a core chemistry of MFG Chemical, which the company has been producing in large quantities since 1982. These improvements in manufacturing quality, control, consistency and efficiency will catapult MFG Chemical into an industry leadership position in the quality, efficiency and safety of DOSS manufacturing.”
Cooling system Improvement All three plants upgraded control systems, cooling systems, and relief systems, and new technology supports the manufacturer’s strength in advanced chemical processes. For the cooling systems, the improvements include: New cooling towers for better quality control of the reaction using a closed system at known temperature with lower cycle time and lower water waste; among others.
It is capital investment project which is already improving management systems related to process safety and key compliance workflows generally. It will be especially useful for improving the quality, consistency and safety of DOSS manufacturing. The Project improvements will include the following:
- New cooling towers for better quality control of the reaction using a closed system at known temperature with lower cycle time and lower water waste,
- New DCS process control technology for better control on reaction parameters and cycle times,
- New pressure release control valve, safety instrumented systems and upgraded piping to minimize and localize possible run-away reaction.
Automated temperature control
Dr. George Graham, vice president of operations says, “MFG Chemical is undergoing tremendous growth in volume along with the addition of many new product lines. Automatic feed control of multiple simultaneous feeds is one of MFG’s distinctive.” The control features that simplified the process for operators included automated temperature controls for the reactor. Having both exothermic and endothermic reactions, automatic control of heating and cooling has enabled a greater precision of control and reducing the need for operators to continuously monitor temperatures and change set points for different phases of the reaction.
Flow metering devices
No new processing equipment was added, but the existing reactors, distillation columns, condensers and receivers were outfitted with new automation hardware. There was a list of new flow metering devices. New mag meters measure cooling water flow rate directly from the cooling towers, ensuring the primary supply of cooling water. Graham says, “We use vortex meters to measure cooling water flow rates for each reactor and condenser, ensuring sufficient cooling is always available. By measuring the temperature of its cooling water discharge, MFG is tracking how much energy is being dissipated from the reactor. Many new temperature and pressure indicators were also installed. “Nothing revolutionary there, but a lot of new I/O points that were installed,” he says.
Additional cooling towers are part of the improved cooling capacity, which has improved cycle times on cooling-intensive processes. Joe Dymecki, vice president of sales at MFG Chemical said, “We roughly doubled the cooling water flow to each reactor. With reactor-based chemistry, especially feed rate-controlled reactor-based chemistry, one of the big limitations is always dealing with exotherm. So improving our cooling capacity will enable us, eventually, to increase our feed rates because we’re better able to dissipate the exotherm”.
Automation will also improve the process of heating, before flipping over to the cooling phase. “Before those were all operator manual interventions,” Dymecki says. Now, operators can add a button, put a reactor going from heating to cooling, and it’ll automatically de-pressure the jacket, lower the jacket down, and flood the jacket with cooling water. Those were all somewhat manual tasks before we had an automated system, he added.
New cooling water system substantially increased the flow rates to the reactors and condensers. This increases the heat transfer so more heat can be removed from the reactor every minute,” says Graham. Flow rates were designed within proper engineering limits, so maintenance should be minimal, he added.
Safety systems
Safety was essentially where the project started, and it’s paramount to the company’s success with such a wide variety of products and chemistries. “We looked at the variety of chemistries that we make. We looked at the opportunities for mistakes that could be made and what the outcomes could be. And so this was one way that we really designed a relief system that encompasses the boundaries of what could happen from a process hazard perspective,” Graham says.
The system has continuous monitoring of reactor pressure, temperature, and cooling functions. The both absolute value and rate of change is measured, so if the rate of change is too high on any of those parameters, then that will interlock the reactor as well and throw it into what we call max cool. The max cool function will interrupt all feeds to put the reactor into a safe condition, he adds.
OSHA safety management
Company uses a management of change process for each new product and performs a process hazard analysis (PHA), a requirement of the OSHA process safety management for hazardous materials, and which helps determine what administrative and engineering controls are required to address certain risks involved in chemical manufacturing. PHAs are required on all end products and process equipment.
On-site installation took place from the middle of 2020 to April 2021, but years of planning prior to that made the process smooth, even during a global pandemic. Overall, the project only lost about two weeks due to COVID-19. Graham stated, like everyone, the project managed with new safety protocols, but the two-year front-end design phase kept the project wholly on track. On a few occasions during the pandemic, the project felt a crunch when certain staff was affected.
Graham remarks, the features of the modern DCS systems, their ability to communicate with smart sensors and smart hardware in the field, it’s light years ahead of where we used to be, and so now there’s a lot of diagnostics built into the systems. The systems are so flexible in terms of growth and the ability to add I/O onto the systems. Still, over 4 months passed by, after commissioning of new equipment, Graham consider this an establishment phase.
Cookie Consent
We use cookies to personalize your experience. By continuing to visit this website you agree to our Terms & Conditions, Privacy Policy and Cookie Policy.
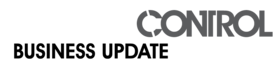