Sustainability and high performance of refrigerated space used for the preservation of perishable product capitalises on conservation techniques which reduce environmental impact. The concept embraces a variety of techniques including the exchange, or supplementation of mechanical refrigeration systems by Thermal Energy Storage (TES) that incorporate Phase Change Materials (PCM), and advanced refrigeration control. By using TES as a part of an integrated system, overall efficiency can be improved resulting in lower energy costs.
Introduction The Latent Energy Cycle To properly understand the way TES can be used in a refrigerated environment, it is important to understand the difference between sensible and latent heat. When thermal energy is transferred into or out of a perishable product, that product becomes measurably warmer or colder. This is called sensible heat, and can be measured using conventional temperature measurement devices. Latent heat in this case occurs when a material is going through a phase change from solid to liquid and that material is capable of absorbing thermal energy without becoming measurably warmer or colder for the duration of the phase change process. Once the phase change is complete, the product heat becomes sensible (and measurable) again.
TES modules containing PCM are placed above the storage racking so that they are above the product and are also placed inside the air stream of the evaporator fans. This allows heat to flow via convection to the TES when the air units are off. Once the TES reach their thermal capacity absorbing heat, the air flow from the evaporator fans can efficiently and directly cool the cells back to the solid state.
The phase change materials in the TES system provide latent heat capacity to the refrigerated environment, allowing the TES to absorb a large amount of thermal energy from the surrounding environment while remaining at the same temperature. This functions to allow the refrigerated environment to maintain a cold operating temperature for an extended time period without running the mechanical system(s). The freezer TES systems operate on a continuous 24-hour cycle. The latent heat capacity of the system reduces the frequency of compressor cycling by providing a larger heat sink on which the compressor can now work on while operating a t a higher, more efficient, suction pressure.
Effects on Operating Efficiency
By employing TES in a refrigerated space, measurable improvements in equipment and system efficiency can be realised. By managing the existing refrigeration equipment to leverage the thermal capacitance of the TES, existing refrigeration equipment is able to operate at peak design efficiency, often exceeding typical performance. This effectively improves the coefficient of performance of the equipment, EER of the compressor and the SEER of t he system.
Higher Suction Pressure
Compressors for refrigeration systems are designed for peak conditions. Operation is typically at partial load conditions for the majority of the life of the compressor. By imposing an additional load (TES) on the system, the compressor will operate at higher suctions and improved horse power/ ton, EER and SEER.
The relationship of BHP/ TR as pressure goes up and down. These are actual ratings of industrial large bore and stroke reciprocating compressors pumping R -22. This shows a 2.7 percent improvement in BHP/ TR for a 1 degree rise in suction temperature. In small bore hermetic compressors this is more dramatic due to the small bore and higher operating speeds. By increasing the run time at higher suction temperatures the net or SEER efficiency is improved significantly.
As air unit coils lose their load, the ΔT becomes small, the liquid flow is shutoff by the expansion valve, so the long circuits boil off the liquid refrigerant and the rest of the circuit superheats the gas returning to the compressor. This is one of the built in inefficiencies of DX systems because expansion valves are designed to operate as a function of superheat. Unlike industrial coils, a re-circulated system where liquid is over fed to maximise coil heat transfer, DX coils leave about 30 percent of the coils surface to make sure t he DX valve can provide superheat with which to regulate its DX valve.
The superheat is a menace for several reasons. It forces the compressor to operate less efficiently by pumping superheated gas instead of saturated gas and it tends to wire draw the parts inside the DX valves. The compressor itself suffers because it now operates at higher outlet temperature s, higher compression ratios and with less efficiency. More blow-by is experienced which causes wear, breakdown of oil, etc. By forcing the compressor to operate at higher and more efficient suction conditions, the system operates at a lower horsepower per t on (better coefficient of performance, EER, SEER, etc.).
Reduced Runtime and Capacity
The increased thermal capacity offered by TES can allow for refrigeration equipment sizing to be skewed towards average load rather than peak load, because the additional thermal mass allows the room to warm more slowly, and the TES absorbs heat more efficiently than stored product both in rate of transfer and in its heat capacity.
Otherwise, the compressor would cycle repeatedly from high down to low pressure when at lower than peak load condition. This is necessary the keep product temperatures within their range. TES prevents the short cycling and permits the compressor to operate for longer periods then turn off for extended periods while the TES cool the room.
Repeated cycling is mechanically detrimental to the fans and compressors. Compressor runtimes have been effectively reduced by as much as 50 percent, using the TES system.
Also, TES can mitigate the need for backup refrigeration capacity in certain situations. This can lead to a reduction of refrigeration equipment capacity and runtime required to condition the space, resulting in lower up-front expense, extended equipment life, and a reduction in maintenance costs.
Effective Envelope Improvement
By utilising TES, the room envelope efficiency is effectively improved by limiting the impact of infiltration. Placing TES above product, near doorways, along ceilings, and other sources of infiltration, the impact of infiltration on stored product quality can be reduced as the TES will absorb infiltration more efficiently than the stored product.
Intelligent Defrost Coolers with temperatures at or near 35 °F require defrosting to melt the ice formation during operation. Less ice and moisture is extracted with the TES system because the coil has been forced to operate more time at higher temperatures. While system designs vary, those with greater coil surface can operate at higher temperatures.
Traditional defrost cycles:
- 45-60 minutes per defrost, 3 -4 defrosts per day.
- Surface temperature of heating element over 250 F degrees for duration. Coil can reach 100F.
- Results in steam blown into space which will condense and freeze as frost on any surface.
TES defrost cycles:
- 20-25 minutes per defrost, only as needed; in freezers 1-2 defrosts per day, some coolers much less frequent (once per week)
- Temperature terminated defrost
- Demand defrost based on coil efficiency
- Heaters not operated for entire duration of defrost
- Observation of a proper drip-down time to let the coils dry before initiating fans
By optimising cooling heat transfer temperatures in both the TES and in the evaporator, the infiltration air load is shifted and less moisture extracted. By managing the defrost process, less moisture from the evaporator coils blown back into the room after defrost.
Fewer defrost cycles lead to more uniform product temperatures, leading to less product shrinkage in open, unwrapped product.
Dynamic System
A refrigerated storage environment changes over time. The amount and type of product can change, as well as daily operations. By employing a cohesive control strategy involving the use of TES, the refrigerated system can adjust to both daily and general use fluctuations while protecting stored product and improving energy efficiency. The system can dynamically adjust control strategy to reflect real world conditions.
For example, if a controlled space is in a shifted demand period, but enough heat is introduced into the room via infiltration t hat product integrity is threatened, the system will take steps t o protect the stored product even if that means a slight increase in energy consumption. This can be accomplished while maintaining a desirable demand profile. By measuring product temperature directly, the control system can leverage the thermal capacity of the TES while adequately protecting stored product.
Changes to the room envelope, such as door openings, are incorporated so that pending defrost cycles can be initiated a t an advantageous time. For example, the room can be allowed to recover from an extended door opening before a defrost cycle is initiated that could further increase temperature.
Other Benefits
The application of the TES system can improve the operating efficiency of the existing refrigeration equipment without costly replacement,
While improving the shelf life and quality of perishable foods and other products:
- Refrigeration equipment can operate longer at higher suction pressures and higher coil delta temperatures, where it is more efficient.
- Refrigeration equipment can operate at lower condensing pressures, reducing compressor KW.
- Reduction of refrigeration equipment total runtime required to condition the space, resulting in extended equipment life and a reduction in maintenance costs.
- TES has the ability to shift load throughout the day by leveraging the thermal energy storage capacity of the
- TES to match the utility rate structure and operational needs of the electric utility with Demand Response and Smart Grid Integration capability.
- Incorporation of intelligent defrost capability, reducing the energy impact of defrost.
- Ability to respond dynamically to real world usage scenarios, including product loading and power outages.
- Pre-emptive detection of need for service, including service pre- classification.
- Effective management of moisture (relative humidity) in the room, to improve safety and equipment efficiency.
- Improve quality of product through the reduction of product temperature fluctuation and open product shrinkage, while minimising low temperature suction pressure (temperature) which extracts excessive moisture.
- Refrigeration equipment sizing could target average load rather than peak load, leading to lower initial cost.
The following discussion relates to the operation and use of commercial refrigeration equipment for operating freezer and cooler perishable product storage space. The system employs the use of Thermal Energy Storage cells (TES) installed in the ceiling areas of refrigerated rooms combined with intelligent controls, and a 24/7 remote monitoring package.
Cookie Consent
We use cookies to personalize your experience. By continuing to visit this website you agree to our Terms & Conditions, Privacy Policy and Cookie Policy.
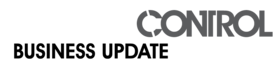