Using actively managed Thermal Energy Storage (TES) improves the net energy cost of ammonia refrigerated frozen storage by 20 percent or more by maximizing the refrigeration output per kWh of energy input, shifting power consumption to off-peak periods, and reducing total equipment runtime.
The energy demands of cold storage operations exist around the clock. Frozen food and other perishable products must be stored within specific temperature ranges at all times without interruption. Viking Cold Solutions, Inc. has developed Thermal Energy Storage (TES) technology which reduces energy demands and provides time- of-day flexibility.
Since 2010, Viking Cold has been providing its customer’s energy savings of 25 percent or more by integrating TES systems into their large HFC refrigerated frozen warehouses.
The same energy saving benefits enjoyed by HFC refrigeration operators can also be realised by operators of cold storage facilities with ammonia-based refrigeration systems. This paper explains how the patented TES technology works, how it impacts the net energy consumption of the ammonia refrigeration system, and how it will save energy and improve the bottom line.
Ammonia refrigeration systems and energy
A lot of work is required to mechanically remove heat from cold rooms. Typically, refrigeration is the first or second highest operating expense. Ammonia refrigeration systems are a popular engineering choice for very large industrial cold storage applications, as they can be very energy efficient in large scale compared to conventional systems utilising HFC (or other synthetic) refrigerants.
To achieve economies of scale, engineers utilise multiple compressors to remove large amounts of heat from the system, and expel it to the outside environment. Since ambient conditions change throughout the year, and the product inventory may change daily, the effective load on the refrigeration system is not constant. Consequently, refrigerationsy stems are engineered to meet the maximum potential refrigeration load. They often have built-in mechanical redundancy and have the ability to scale output for lesser load.
Like every other engineering challenge, there are tradeoffs. In the case of large ammonia refrigeration systems, engineers have to make tradeoffs between the efficiency of a system under maximum load and a system under partial load. The compressors are the largest consumers of energy in the refrigeration system. The most common balance between cost and efficiency starts with the use of multiple large compressors connected in parallel. As the required refrigeration load changes, compressors can be staged on or off. Evaporators are the second largest consumer of energy. The total number of evaporators in the system is dictated by the size and maximum refrigeration load in each room of the warehouse, and for the most part operates continuously. Condensers are often installed in multiples, and can be staged proportional to the load. Liquid recirculating pumps for ammonia and water also consume energy in the system.
In Figure 1’s example with 3 compressors and 2 condensers, the system can be very efficient in one or two partial load conditions when the required output matches an exact combination of fully loaded compressors. In reality, the load changes continuously as dictated by the loads and temperature conditions both inside and outside the warehouse.
To maintain constant temperatures inside the warehouse, the system must provide for fine adjustments to achieve a partial fraction of full load.
Each compressor therefore has an unloading valve, or slide valve to control how much of the compression output is fed into the system. While this is great for matching the load requirements for the system, it usually means that the compressor is consuming more energy than is necessary for the corresponding effective work output. More often than not, compressors operate under these conditions.
Even when variable frequency drives (VFD) are used to slow the RPMs and power consumption of the motors, the effective output efficiency of the compressor is less than ideal. The compressor rotor was designed to be most efficient at full RPM, where efficiency is a function of rotor tip speed. Also, VFD motors are less efficient than high efficiency motors due to power losses from AC to DC conversion.
To summarize, the energy consumption of the system can most effectively be reduced when whole components in the system are idled, and the ideal energy efficiency condition can only be achieved if the refrigeration load exactly matches an exact whole unit (compressor) of output.
Viking Cold TES working pattern
Heat is one of the primary forms of energy that exist in nature. Thermal energy storage taken literally would be the storage of heat. In the case of cold storage however, thermal energy storage is actually storing the absence of heat.
Thermal energy storage requires an additional mass within the cold storage room to change the temperature response. The Viking Cold TES technology uses additional mass that is 300 times more effective at absorbing heat than typical frozen products. (See Appendix A – Phase Change Material)
The Viking Cold TES uses proprietary phase change material (PCM) to absorb heat. When a substance undergoes a phase change its temperature remains constant.
Viking Cold has a variety of PCMs which are designed to change phase at specific temperatures commonly used in frozen warehouses. When the TES cells are absorbing heat load in the warehouse from all the various forms of heat infiltration, they remain at a constant temperature matched to the operating specification of the freezer.
The Viking Cold TES utilises two very important principles of physics to give it an energy advantage.
- Warm air rises; any heat infiltration into the warehouse will naturally increase upward, known as convection. The Viking Cold TES is designed to be passively installed as high as possible in the warehouse to absorb heat from the warm air as it rises.
- The thermal resistance (or R value) of the Viking Cold TES cell is one fifth that of typical frozen product. This means the TES cells, not the product, will absorb 85 percent of the heat inside the warehouse.
Similarly, when the refrigeration system operates it will remove heat from the TES cells five times faster than removing heat from the frozen products. While doing so, the refrigeration system is performing the same amount of refrigeration work, but it is using less energy to do so.
In summary, Viking Cold’s proprietary passive phase change TES technology can store large amounts of energy and is more efficient at transferring heat energy to the surrounding air. Less energy is required for the refrigeration system to perform the same amount of work.
The Benefits of TES with an ammonia system
The heat absorption capacity of the TES system is like having supplemental refrigeration tonnage in reserve. The difference being that TES absorbs heat energy when the primary refrigeration system is idle.
Phase Change Material (PCM) remains at a constant temperature as it absorbs heat energy and changes phase from solid to liquid. The warehouse will remain at specified temperatures until the stored energy is depleted. Since the heat transfer to the PCM is through free convection, it requires little to no evaporator fan to be effective. To realize a net kWh savings using TES, the free energy value of the TES must be cycled on a daily schedule.
During the day, ambient outside temperature is high which requires more horsepower per ton of mechanical system refrigeration. At night when the outside temperature drops, less horsepower is required per ton of refrigeration. The stored thermal energy is used as supplemental refrigeration tonnage during the day, allowing some of the compressors to be idled. Later at night when the compressors can generate more refrigeration tons per horsepower, the heat that was absorbed by the TES can be removed efficiently, completing the daily cycle.
Additionally, the time of day is often correlated to energy prices, especially during peak demand periods late in the afternoon. Having the flexibility to idle equipment and utilised stored thermal energy can greatly reduce the equivalent price paid per kWh.
In summary, utilising TES on a daily cycle allows fewer compressors to run during the day when they are less efficient and when energy is most expensive. The offsetting refrigeration is performed at night by running more compressors efficiently when energy is least expensive.
Other benefits of the Viking cold system
- In addition to the energy savings made possible by leveraging the TES to yield maximum efficiency from the ammonia refrigeration system, the Viking Cold system provides many other benefits:
- Less evaporator fan runtime will result in less frost accumulation on the evaporator coil, which means less frequent defrost cycles are needed for optimal performance, saving energy and the introduction of unwanted heat into the warehouse.
- Reduced runtime for all equipment will result in longer equipment life, therefore extending the timetable for purchasing new equipment assets.
- For systems with evaporative cooling condensers, there is a reduced amount of water and water treatment chemical expenses.
- Many utilities have robust incentive programs for energy efficiency improvements, especially for technology that shifts electrical demand to off- peak hours.
- For operators who have already invested in solar power generation on site, the TES makes it possible to significantly reduce power consumption and demand charges at night.
- The constant temperature of the PCM will result in greater product temperature stability, which will improve the quality of the food that is delivered to customers, and avoid possible ‘temperature abuse’ issues.
Conclusion
Industrial low-temperature refrigerated storage warehouses consume large amounts of energy around the clock. Ammonia refrigeration systems have the potential to be extremely efficient, but partial loading, daytime electricity rates and higher condensing temperatures prevent their achieving maximum efficiency.
Viking Cold’s proprietary phase change TES leverages phase change materials to store large amounts of energy while holding the temperature constant inside the warehouse. As a passive, non-circulating system, there are no incremental energy requirements. Viking Cold’s TES cells exchange heat five times faster than food products alone.
By absorbing heat infiltration, the TES serves as supplemental refrigeration capacity. As a result, whole increments of the ammonia refrigeration system can be idled for long periods of the day. When the refrigeration system does run, it can run under fully loaded conditions for maximum energy efficiency. Additionally, having the flexibility to choose when the refrigeration runs, operators can run the equipment at night to take advantage of lower condensing temperatures and favorable electricity rates.
After becoming a customer of Viking Cold, cold storage operators can use TES technology to reduce their energy costs by 20 or more.
For more details, visit – www.vikingcold.com
Hank Bonar II P.E., CEO – B
onar Engineering, Michael Crisman,
Engineering VP – Viking Cold Solutions
Cookie Consent
We use cookies to personalize your experience. By continuing to visit this website you agree to our Terms & Conditions, Privacy Policy and Cookie Policy.
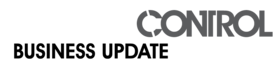