Electric motors are essential part of many products ranging from industrial applications to many applications such as HVAC, water pumping, and nowadays heavily in space and transportation applications. Naturally, electric motors are a component in a whole system, responsible for delivering required mechanical power to system to achieve some motion functionalities. Energy consumption of the system links with electricity consumption of motors and associated subsystems. This paper attempts to present the energy consumption of motor and associated subsystems to highlight what needs to be done to achieve higher energy savings through case studies with different efficiency class motors of 18.5kW, Variable Frequency Drives (VFD) and process and optimisation.
Motor systems use approximately 45 per cent of the global electricity. In the European Union 65 per cent of the electricity is used by motor systems. In industry, depending on branch and region, the share of motor systems consumption is 65-75 per cent. Electric motors along with VFD are extensively used in industrial, HVAC, water and many other applications. The global stock of electric motors is estimated at 2.23 billion wherein small motors less than 750 Watts account about 90 per cent of the electric motors population (approximately 2 billion), which consumes only 9 per cent of the overall electricity consumption. There are around 230 million motors i.e. 9 per cent of installed motors the power range of 0.75 kW to 375 kW are responsible for 68 per cent of the electricity consumption by motor systems. Large motors, i.e. powers above 375 kW represent 0.6 million motors installed globally, which are consuming about 23 per cent of the energy use. In electric motor systems, there are energy losses in the motor, mechanical assemblies and so on. But, at the same time, motor systems have a large potential for energy savings itself and hence energy saving potential are available. As on today, possible energy savings potential are:
• 90 per cent of the total savings potential remains insufficiently addressed
• 10 per cent – Increase component efficiency
• 30 per cent – Use variable speed drives
• 60 per cent
System and process optimisation
There a few research papers attempt to highlight on energy savings. An energy-savings in Ship Central Cooling Systems and comprehensive review on energy efficiency enhancement initiatives in centrifugal pumping system. But only few papers to attempt to highlight case studies on energy savings with specific example. This paper presents different case study scenarios accounting Direct Online starters (DOL), Component Level, Variable Frequency Drives (VFD’s) and through system and process optimisation.
System with improved component efficiency
The International Electrotechnical Commission (IEC) has come out with internationally applicable standards for testing of electric motors and efficiency classes wherein IEC 60034-2-1 defines the testing of motors and IEC 60034-30-1 defines the motor efficiency (“IE-code”) classes:
• IE1 Standard efficiency
• IE2 High efficiency
• IE3 Premium efficiency
• IE4 Super premium efficiency
India has an efficiency label for motors from 2009 and there is voluntary standard on IE2 level since 2012. However, the 20 years old IE1 motor are being replaced by the modern IE3 induction motors. As on today, most of the countries with power consumption more than 70 per cent of the global electricity have decided to have Minimum Efficiency Performance Standard (MEPS) for motors either on IE2 or on IE3 by 2015/17. At an electricity cost of Rs8/kWh the payback time is around five years, which once again depends on the application and therefore the theoretical calculation cannot be always confirmed in the actual application. The Fig. 2 show one such mark on IE3 at component level.
From Table II, it is evident that for the same capacity of 18.5kw motor with IE3 efficiency class operated through DOL gives an energy saving about 2,961 kWh’s compared to IE1 efficiency class motor, which corresponds to 5.63 per cent improvement on energy savings with respect to baseline value. This gives an opportunity to move from IE1 to IE3 motors at component level. But, at the same time, few possible pitfalls to be considered which are follows:
• High efficiency induction motors have a lower slip than low efficiency motors, and consequently the speed will be slightly higher
• A higher speed will lead to a higher power
• In a fan application, according to the affinity laws, the power increases with the cube of the speed
• If this is not carefully considered, then the situation can occur that the energy use of a system upgraded to a high-efficiency motor will be higher than the original system with a less efficient motor
• One best possible solution is to use a variable speed drive
System with VFD
Today, VFDs are the quite common method of air flow control. The VFDs regulates the speed of the motor depending on the speed and load requirements. Higher system efficiency is achieved with big savings by taking advantage of the affinity laws. When motor speed is reduced, the power requirements are reduced by the ratio of the speed cubed. If the VFD is added to the baseline system, keeping the old motor, the payback time with Rs8/kWh is less than a year.
It is evident from Fig. 3 (b) that system with VFD gives huge power savings with respect to baseline DOL case.
From Table III, for the same capacity of 18.5kW motor with IE1 efficiency class operated through VFD gives an energy saving about 25,363 KWh’s compared to IE1 efficiency class motor with DOL which corresponds to 48.18 per cent improvement on energy savings with respect to baseline case.
Nowadays motor technologies are getting improved day by day and Fig. 4. Gives overview of different motor technologies with higher efficiency classes.
With the above motor technologies, if we use the higher efficiency class motors with VFD’s, there is further energy improvement are possible, which is shown the below Table IV.
From Table IV, it is more evident that higher efficiency class motor i.e. IE3, IE4 with VFD gives the best possible energy savings. In the selected case, IE4 motor with VFD gives energy savings opportunities up to 55.75 per cent.
System and process optimisation
Next level of optimisation is at the system level and process optimisation for the entire plant. One of the example considered here is wastewater treatment plant. The wastewater treatment plant has reconfigured it is processes and optimised them with variable speed drives that allow the production process to be adapted to the variation during a 24-hour cycle as shown in Fig. 5. Nowadays this facility has a net production of heat and electricity, supplying the district heating system in Denmark. By using co-production of electricity and heat based on methane gas extracted from the aerobic sludge, a 130 per cent electricity production is achieved.
It is interesting to note from the case study that each system has it is own advantages and disadvantages. It is seen from the case study, motor with DOL does not save any energy, motor with higher efficiency classes i.e. IE2, IE3 and IE4 gives few per cent incremental energy savings and Motor with VFD’s seen as potential candidate to gain significant advantage on energy saving. Apart from these, System level optimisation results in the highest energy savings and there are some key elements which make this possible
• Freedom of choice to combine VFD with the right motor technology for the specific application
• Open availability of efficiency data, also in part load conditions, to be used in optimal system design
• Use of energy optimised motor control is key to harvest the efficiency potential of electric motors
• Authorities and regulators are encouraged to focus both on component efficiency and on system efficiency in legislation and regulation
• There is a huge cost effective untapped potential
• 80 per cent of the installed motor systems are fixed speed
• At least 50 per cent of the fixed speed installations can be retrofitted to variable speed with payback times less than a year to three years
• 70-80 per cent of the sold motor systems are without a variable speed drive
Authored article by:
Dr S Paramasivam,
Danfoss Drives, Chennai, India
Cookie Consent
We use cookies to personalize your experience. By continuing to visit this website you agree to our Terms & Conditions, Privacy Policy and Cookie Policy.
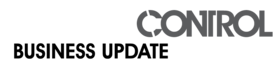