New technologies in the cold storage industry such as Quick Freezing Racks, wireless RFID and product picking improvements, have created huge opportunities in the market.
The new normal demands digital and technological shifts and the businesses may need to think differently about automation. Such technologies offer advantages in moving products on conveyors that saves downtime and labour. This also involves maintaining and tracking systems for products such as fruits and vegetables by reducing wastage possibility of temperature sensitive products. Warehouse automation includes cloud technology, robots, conveyor belts, truck loading automation, and energy management. Refrigerated storage has become an integral part of supply chain management in terms of transporting and storing temperature-sensitive products. Moreover, rising automation in refrigerated warehouses is projected to boost the market further.
Automation uses robots to fulfil the tasks performed by humans to run a cold storage warehouse. These systems are more advanced and flexible and easier to incorporate into your daily warehousing operations. Explored herewith are few factors to determine the right solution for automation, such as palletisers, automated storage and retrieval systems, conveyors, automated picking solutions, automated truck loading/unloading systems, and other types of material handling equipment have a reputation for moving large volumes of inventory with high levels of accuracy.
Sensing systems and devices for warehouse operations
Cold storage warehouses can be classified by storage: automatic or manual or rack-supported or not. Nevertheless, the most common differentiation lies in the installation’s temperature setting. Refrigerated warehouses with a controlled temperature between 32°F and 50 °F are used in the food (dairy, cold meat, etc.), pharmaceutical, and hospital sectors. Cold rooms that maintain a controlled temperature of -22 °F to 32 °F are especially widespread in the frozen food industry. It’s important that this continuous temperature control is required not only during storage, but also in goods receipt and dispatch which significantly increases energy consumption in the installation, driving up the cost of each logistics process. Sensing systems—including wearable devices—play a foundational role in the implementation of Industry 4.0 solutions. The information they provide helps link the physical and digital worlds, driving Industry 4.0. Within a warehouse, automated-guided vehicles (AGVs) equipped with laser sensors are but another example as stated in an article published by Deloitte.
Rajashekara remarks that Industry 4.0 was about mass customisation at various levels. With Industry 5.0, manufacturers aim to bring in creativity and innovations in products with robots doing all the repetitive jobs. Skill development will become a very arduous task as the manpower needs to be trained to use cutting-edge technologies and learn machine language.
Automated cold storage warehouses
The purpose of an automated cold storage facility is to streamline processes and improve safety for both the employees and the goods. To automate a warehouse, you need to install automatic handling equipment, such as stacker cranes (AS/RS) for pallets or for boxes. These storage systems are usually served by conveyors, which speed up goods flows and do away with the need for operators to move stock in unfavourable environmental conditions.
Across the world, businesses use temporary workers and experience high turnover. Alan Taliaferro, a partner at Deloitte remarks, “The main justification for automation is primarily labour related. You have concerns like turnover and difficulty recruiting people to work in a freezing environment. Plus all the unpleasant things about working in a cold environment mean you’re paying more than you would in a dry environment, which makes the cost of labour higher.” Incentivising with higher wages may level the playing field for recruitment in some cases, but many governments place regulations on cold chain labour that reduce the productivity of these resources.
The ripple effect of adding people goes beyond wages. More people lead to more equipment such as forklifts and RF scanners. Also, more hands on the floor could increase the chances for data logging errors, mispicks, or damaged products in transit. With low availability of warehouse labour across all industries, it is difficult to sustain manual labour in cold chains. These conditions make automation a great fit. Automation doesn’t steal jobs; it changes them. Not many people want to work in -24°C (-11°F) temperatures while moving 50kG (110 lbs.) boxes. By introducing these systems into the warehouse, you automate jobs people generally find undesirable. Meanwhile, automation creates new jobs in management, maintenance, and repair. It is a shift of employment opportunities that likely appeals to younger generations more interested in managing technology.
Business strategy and mindset
Businesses with short-term strategies may need to think differently about automation. Many third-party logistics (3PL) providers operate on one-to-three-year contracts with their customers. This makes automation decisions difficult. Automation investments made for one customer may not work for another customer. This could lead to costly and unjustifiable retrofitting or other workarounds. In these scenarios, and for industries that experience a lot of disruption, robotics such as automated guided vehicles or autonomous mobile robots (AMRs) may be a better option. These technologies can be moved to other buildings and leasing options might work better in terms of the pricing structure. Fully-automated warehouses tend to see a better ROI than semi-automated warehouses.
Smart technology and changing trends
According to a report from consulting company MarketsandMarkets, the frozen food industry is slated to grow by 5.14 percent annually over the next three years, reaching a global turnover of more than $283 billion in 2023. During the pandemic as e-commerce orders grew, retail orders shrank. As a consequence, warehouses were seeing more units picking than ever before. Before deciding on automation, it’s critical to consider the changing dynamics of consumer behaviour and order profiles overall. These trends have been growing for a long time, but Covid may have deepened consumer reliance on online shopping. “I think the growth of e-commerce is going to be even greater than people imagine,” says Taliaferro. “e- commerce was expected to have a 15 to 20 percent growth this year, but now it’s probably going to hit 100 to 200 percent.” Navigating this question could be the key difference in making a smart technology investment for the future.
Automation offers key benefits that can reduce costs, improve material flow, increase accuracy, and streamline operations. Automation is built for velocity. If your business moves a lot of inventory, automation is a great way to churn the orders. Also, automation scales well. Typically, these systems are designed for high throughput based on your operation’s peak averages. End-to-end visibility is key to pleasing customers and meeting regulations in all regions. However, when it comes to food and pharmaceuticals stored in freezers, the spotlight on foul and lost products is brighter. While traceability is possible with manual operations, it’s more prone to blind spots or errors in your records. Over time, labour costs exceed the investments businesses make in automation. Sometimes, it’s better to invest upfront. This mindset also applies to warehouse robotics, but the applications are different. Making a one-time investment sets you up for years, even decades, of high-volume throughput sounds appealing. It’s important to build solid business requirements and get buy-in from your leaders, but if the business case is there this can be a strategic move that overcomes volume and labour challenges.
Advantages of automation
With the implementation of automated storage systems and handling equipment, companies with cold storage warehouses get benefits in terms of increased productivity. In freezing environments, only automation guarantees high-frequency inflow and outflow cycles. This is because the excessive exposure of operators to these temperatures can be detrimental to their health. Also, the deployment of automatic or semi-automatic picking systems — such as voice-picking shortens the time operators spend in the cold rooms, optimising their picking routes.
Automation ensures hygiene in all logistics processes, a key factor in sectors such as the food and pharmaceutical industries. For improved safety and hygiene: automated cold storage warehouses see to it that both the products and the employees are protected, reducing goods management errors and preventing operators from exposure to extreme environmental conditions.
QFR and RFID Technology creating opportunities
Introduction of new technologies in the cold storage industry such as Quick Freezing Racks (QFR), Wireless Radio Frequency Identification (RFID), cross-docking, and product picking improvements, has created huge opportunities in the market. Product picking improvements involve voice-activated robotics. These hands-free machines let cold storage workers command and control order pickings and processes without removing thermal gloves and risking exposure injury. QFR is replacing the way blast freezing is done. New facilities are choosing quick freeze racks that improve air flow to reduce freezing time.
Conclusively, automation in cold storage offers key benefits to reduce costs, improve material flow, increase accuracy, and streamline operations. The key companies are adopting the merger and acquisition strategy to improve their market revenue at the global level. Automation also reduces the dependency on manpower in harsh conditions where labour recruitment is difficult.
Furthermore, as the regulations of the track and trace of frozen goods increase, it is important to utilise automation solutions. Rajesh is of the opinion that infrastructure and HVAC industry is expected to grow hand in hand. For effective and meaningful HVAC industry growth, automation will play a very crucial role. Moreover, digitisation being a key word in the budget this year, automation industry has to play an important role in most of all the processes.
Compiled from sources:
Masterclass.koerber-supplychain.com
Cookie Consent
We use cookies to personalize your experience. By continuing to visit this website you agree to our Terms & Conditions, Privacy Policy and Cookie Policy.
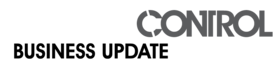