Industry’s leading performance is achieved by using oil free, magnetic bearings that provide world class efficiency and zero performance degradation over the life of the compressor.
Oil free compressor is nothing new for the industry. This, in fact has been rolling around from years, but we never realised its significance to the operational functions. With the increasing concerns over efficient cooling across the globe from the last recent years, several companies are now keen in creating innovations in the HVAC chiller and cooling technology for various industrial purposes. Turbocor Chiller, is the new kid that took off in the recent years in the industry. Turbocor chiller is one of the market’s leading compressor technology that formulates the industrial air- and water-cooled chillers ultra-efficient and achieves a COP rating of 8.
These centrifugal chillers with the chiller test bench, are certified by the Air conditioning, Heating and Refrigeration Institute (AHRI), are highly energy efficient and equipped with new generation centrifugal compressors with magnetic bearings, making them ideal for data centres, hospitals, hotels, green buildings, educational institutions, as well as industrial and process applications.
No single process or product is the solution for delivering quality compressed air. They are instead often referred as oil-free compressors. Key to it, lies in the meeting the technical standard requirements in terms of maximum reliability and efficiency.
Almost every major players of HVAC sector are indulged in providing quality compressor with latest oil-free compression technology. Danfoss, one of the leading manufacturers of oil free compressors,has pioneered Danfoss Turbocor compressor – the world’s first oil-free magnetic bearing compressor for the HVAC industry.
Danfoss Turbocor compressors use advanced technology to deliver high efficiency and low sound levels in a compact footprint. Industry leading performance is achieved by using oil free, magnetic bearings that provide world class efficiency and zero performance degradation over the life of the compressor. Permanent magnet motors and variable speed drives provide unmatched full and part load efficiency.
Danfoss Turbocor® oil-free centrifugal compressors have the flexibility to be used in air cooled, water cooled or evaporative cooled chillers operating in wide range of applications such as comfort cooling, low temperature process, ice storage and heat recovery.This flexibility has resulted in over 70,000 compressors installed in job sites around the world. Its compressors are manufactured in Tallahassee, Florida and Shanghai, China in a ISO 9001:2015 and ISO 14001:2015 certified facility. Sales and service centers are located in the USA, Europe and Asia to serve customers around the world.
Not just for the bearing and compressor technology, but there are companies involved in innovations in chiller technology. Vertiv is one of the leading sellers for chillers compatible for oil-free Turbocor compressors from Geoclima, an Italian manufacturer. The compressors use magnetic bearings, that levitate the moving parts instead of using oil, making them frictionless.The units, customised for the data center industry and branded Vertiv Liebert OFC, were launched at the Data Center World event in London this March.
The Geoclima units use “active” magnetic bearings, which have to be powered up. It is good at modulating and has been used in offices, but previously also took a while to restart. Vertiv’s work has been to refine it for a continuous steady load, and also for a fast start-up time, suited for a critical load.
Another leading company Stulz, which is one of the world’s leading solution provider for energy-efficient temperature and humidity management technology, has announced CyberCoolWaterTec series of water cooled indoor chillers which is highly innovative Cybercool comprise of five different models, with a cooling capacity ranging from 350- 1400kW, CyberCoolWaterTec is designed for use in a wide variety of applications including data center manufacturing and production locations, as well as commercial environments.
Innovating next level technology for chiller and compressors
Danfoss took technology to the next level and introduced ‘The Turbocor a compressor service and repair app to its tech casket. Compressor service for Danfoss Turbocor® compressors is easier than ever with the Danfoss TurboTool® App.You can troubleshoot potential issues right from your mobile phone by entering the symptoms into the app and instantly receive a list of recommendations for how to resolve the problem. Visual aids make navigating the app and troubleshooting compressor issues smooth and easy.
Whereas, the spray evaporator technology in the StulzCyberCoolWaterTec range works with climate friendly HFOR1234ze refrigerant and reduces the required charge quantity by up to 70 per cent compared to flooded evaporation. Just as importantly, the minimum efficiency values according to level two of the Ecodesign Directive’s Seasonal Energy Performance Ratio (SEPR) and Seasonal Energy Efficiency Ratio (SEER) for the year 2021 are also met. Free Cooling is now established as a highly effective way to reduce the energy consumed by chillers. The CyberCoolWaterTec can be equipped with a precisely fitted free cooling module, which minimises running time of the compressor and is fully integrated in the control system. Optimisation is guaranteed, with 24/7/365 operation in free cooling, mixed and compressor modes, with smooth transitions.
These use oil-free magnetic bearings and variable-speed drives to deliver better IPLV efficiencies than conventional oillubricated centrifugal, reciprocating, scroll and screw compressors. They’re also high speed – up to 48,000 rpm, very compact, very quiet, rugged and reliable. Power factor is a high .92. Proprietary magnetic bearings replace conventional oil-lubricated bearings, eliminating high friction losses, mechanical wear and high-maintenance oil management systems to deliver energy savings of 35 percent and more over conventional chillers while ensuring long-term reliability. Over 90,000 magnetic bearing compressors are operating in the field, mainly in high-end vacuum pumps and CNC spindles – any innovation risk with this component technology has been long overcome. Turbocor’s one main moving part (rotor shaft and impellers) is levitated during rotation by a digitally controlled magnetic bearing system. Position sensors at each magnetic bearing provide real-time feedback to the bearing control system, 120 times each revolution, ensuring constantly centered rotation.
Quick dismantling – thanks to modular design
In order to offer the most flexible solution possible, CyberCoolWaterTec not only ensures future safety and energy efficiency, but also meets the practical requirements of consultants and refrigeration specialists. With trouble free installation and assembly features, the system can be quickly and easily dismantled into its basic components. A removable control cabinet that comes with factory installed wall mounting preparation as standard also provides additional functionality.
Control is at the heart of CyberCoolWaterTec and it uses the latest hardware to offer an enhanced experience. An integrated touchscreen allows all components and equipment options to be precisely controlled, while intelligent partial load, parallel operation, pump and valve control can be precisely adapted to respective customer requirements. In addition, a simple connection to all standard Building Management Systems (BMS) systems is possible.
Christian Lohrmann, product manager chillers at STULZ headquarters Germany commented,“From our perspective, the new CyberCoolWaterTec has paved the way for an even more energy efficient and ecological future in the cooling industry, which is particularly relevant with regards to the current discussion on refrigerants and CO2 emissions.”
Vertiv has focused hard on free cooling of late, reducing the amount of time DX chillers are required, but it’s now time to concentrate on chillers again. The ideal is to not use refrigerant based cooling at all, and just use the external air temperature, but there’s always going to be a dependency on DX. Vertiv pushed free cooling as far as it will physically go within the limits of their range, so now we have to focus back towards the DX element.
In spite of every effort to protect the environment, the composition of the intake air still remains the biggest problem in guaranteeing a constantly high air quality. The compressor acts as a giant vacuum cleaner that sucks in, and concentrates, the contaminants in the ambient air. Fortunately, the cooling fluid/oil has a welcome cleaning in addition to its other functions. The additives in the oil neutralise sulphur dioxide, for example, and the oil itself traps solid particles sucked in with the ambient air
Cookie Consent
We use cookies to personalize your experience. By continuing to visit this website you agree to our Terms & Conditions, Privacy Policy and Cookie Policy.
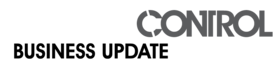