As long as refrigerant is not mixed with large amounts of air, there should be little hazard from some refrigerants during normal handling and use.
An HVACR technician is exposed to many personal safety hazards during the course of a normal workday. In addition to the obvious hazards such as sharp metal, electrical wiring and climbing ladders, the technician needs to be aware of the safety hazards that refrigerants pose.
Refrigerant safety is straightforward: If the refrigerant stays contained in the cylinder or in the system then it presents little danger to people. The hazard occurs when the refrigerant comes out of the container or system, often quickly and unexpectedly. Injuries can be avoided if regular safety checks are performed.
Regular checks on containers and systems for holding pressure and preparing safety equipment and procedures to minimise personal exposure after unexpected releases should help avoid any injuries when handling refrigerants. Specific hazards from refrigerant fall into three categories:
- Toxicity
- Combustion / flammability / decomposition, and
- Pressure
Toxicity and personal exposure
Most refrigerants have undergone extensive toxicity testing before being released for general refrigeration or air-‐conditioning use. Testing generally involves a range of exposure levels and times to determine any possible effects on test animals.
- Short‐term exposures at high concentrations indicate any acute hazards such as irritation, sensitisation of the heart to adrenaline and lethal concentration (LC50 is the amount which kills half the animals in a short amount of time).
- Tests that expose animals for longer periods of time, such as 90 days to two years, are designed to indicate chronic problems. These can include mutagenicity (changes to cells), reproductive problems and effects on organs ocarcinogenicity (cancer-causing).
ASHRAE Standard 341 provides a safety classification for refrigerants based on information related to personal exposure. AHSRAE Standard 152 uses this safety rating and additional toxicity information to set requirements for machinery rooms and sets limits on the amount of refrigerant allowed in systems outside machinery rooms. Many blends containing these individual components are also classified.
Refrigerants not classified in ASHRAE Standard 34 should be reviewed with suppliers to make sure enough is known about their toxicity properties. Some blends may not be classified, but contain classified components. (Note: Many building codes have adopted the new refrigerants listed in ASHRAE standards. Some building codes have not, and therefore, require special permits. A refrigerant that is not listed will most likely require an engineering study to determine if it can be used safely.)
Exposure levels are values given to refrigerants to indicate how much of the chemical a person can regularly be exposed to without adverse effects. All toxicity test results are considered when setting this level. The American conference of government and industrial hygienists (ACGIH) sets the TlV-TWA values for chemicals. TLV-TWA stands for Threshold Limit Value-Time Weighted Average, which is the amount of chemical a person can be exposed to for 8 hours a day, 40 hours a week, without adverse effects.
The maximum value for any chemical is 1,000 ppm, though many refrigerants have shown no effects in toxicity testing as values much higher than that. Other organisations and chemical producers have similar exposure level indexes based on the same criteria. These are the Workplace Environmental Exposure Limit (WEEL) set by the American Industrial Hygiene Association (AIHA); Permissible Exposure Limit (PEL) set by OSHA; and Acceptable Exposure Limit (AEL) used by DuPont.
There are also the Short Term Exposure Limit (STEL) which is based on a 15-minute exposure time in any given day as well as the value Immediately
Dangerous to Life or Health (IDHL). These are used to give guidance for machinery room requirements, ventilation and alarms in an emergency or escape situation, or in circumstances where short releases of refrigerant are expected, which could include refrigerant transfers or servicing large equipment.
Toxicity data is summarised in great detail on Material safety data sheets (MSDS). What all of this data means to the technician, however, is that commercial refrigerants are safe enough to use provided you don’t breathe too much of them. Industry practices for handling refrigerant are intended to minimise personal exposure as well as reduce releases into the atmosphere. General rules to follow are:
- Minimise the amount of refrigerant released. Proper recovery procedures, including clearing hoses, will keep the refrigerant in the containers instead of potentially exposing it to people.
- Never intentionally release refrigerant in a confined space. Even the safest refrigerant can still displace enough oxygen to cause suffocation.
- Set up ventilation equipment, like a portable fan, in areas where possible release would mean high concentrations.
- Refer to AHSRAE Standard 15 and local building codes for additional guidance.
R-22 and R-134a fall into this category. R-22 was found to cause a combustion hazard during a pressurised leak test with air. For this reason, most refrigerants should be used only with pressurised nitrogen for leak testing. As long as refrigerant is not mixed with large amounts of air, there should be little hazard from some refrigerants during normal handling and use.
Decomposition can occur with any refrigerant when it gets hot enough (generally above 7000F). Refrigerant can decompose in systems or containers exposed to fire or other extreme heat, electrical shorts (burnouts), or in refrigerant lines being soldered or brazed without being cleared first. Obviously, refrigerant containers or charged systems should never intentionally be exposed to a flame or torch.
When a refrigerant is decomposed or burned, the primary products formed are acids: Hydrochloric Acid (HCI), if the refrigerant contains chlorine, and Hydrofluoric Acid (HF), if is contains fluorine. These products are certainly formed when hydrogen is present, such as from the breakdown of oil, water or if the refrigerant has hydrogen attached (like R‐22 or R‐134A). If oxygen is also present (from air or water), then it’s possible to form carbon monoxide, carbon dioxide and various unsaturated carbonyl compounds – the most notorious of which is phosgene.
Decomposition of R-22 or HFCs may form other carbonyl fluorides, however they are not as toxic as phosgene.
The standard practice for handling decomposed refrigerant is to collect the gas, treat the refrigerant and/or the system for acid contamination, and appropriately dispose of the burnt gas. Please note that any cylinder or system component exposed to high heat or fire should be retested or discarded. Cylinders used to recover burnt gas should be checked and cleaned before being put back into service, especially the valve and/or pressure relief device.
Physical hazards
The fact that it’s a liquified gas under pressure is one of the more obvious hazards of refrigerant. Sudden, unexpected release of pressurised refrigerant can result in personal injury.
Frostbite – Liquid refrigerant suddenly released from high pressure to atmospheric pressure will flash and boil to vapor. Naturally, the temperature of the refrigerant will drop quickly to the boiling point and the refrigerant will quickly absorb heat from whatever it is touching. If the refrigerant is touching skin it can cause frostbite. Frostbite damages skin by freezing water inside the skin cells, which can expand and burst the cell walls. To treat frostbite, cover the exposed area with warm (not hot) water or a wet compress. The skin must recover slowly or more damage can occur. Do not rub the affected area to try to warm it as it may inflict more damage. Protective clothing, gloves and eye protection are effective at preventing frostbite by keeping liquid refrigerant away from the skin.
Rupture of tank or system – Cylinders or systems without pressure relief devices could break if the refrigerant pressure inside were to exceed the strength of the cylinder or system component. This type of failure can be quite hazardous if the refrigerant is at a high pressure or solid material is blown loose. Containment failures are caused by one of two things: The refrigerant pressure has increased above the pressure rating of the cylinder or system, or something has happened to the –
- Cylinder or system so that it will no longer hold normal refrigerant pressure.
- Elevated refrigerant pressure can be caused by exposure to heat. Refrigerants with pressures similar to R‐12 will develop more than 500 psia at temperatures above 2000F. Refrigerants with pressures similar to R-502 will achieve the same pressures at about 1500F.
- Hydrostatic pressure also can develop quickly in a confined volume that has been completely filled with liquid refrigerant, for example liquid-full hoses between shut valves or an overfilled recovery cylinder.
- Refrigerant tubing, hoses, system components and some refrigerant cylinders surely would fail at some elevated pressure without certain safety provisions. Various pressure relief devices are used to lower the pressure back to safe limits by releasing some or the entire refrigerant.
Cookie Consent
We use cookies to personalize your experience. By continuing to visit this website you agree to our Terms & Conditions, Privacy Policy and Cookie Policy.
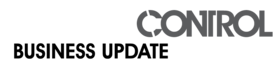