Until recently most manufacturers and retailers with sustainability goals were focused on measuring carbon emissions generated by their own organization or by the generation of the electricity they purchased. Now both are being pressed by end consumers to also reduce the carbon footprint of their distribution partners throughout the entire supply chain (Scope 3 emissions).
To remain competitive, lower their costs, and improve their own sustainability measures, supply chain partners are looking for technologies that give them the most carbon reduction impact for the investment. For years LED lighting has been the low-hanging fruit to cut costs and energy consumption, but most operations serious about energy reduction have already installed lighting upgrades.
According to the US Energy Information Administration across all commercial buildings, refrigeration is the largest definable category of consumption (16 per cent) after lighting (17 per cent). When looking specifically at buildings with large cold storage areas the same data shows refrigeration accounts for 43% of electricity consumption. With the right technology, this presents an opportunity to reduce a large percentage of energy consumption in one targeted area.
A proven technology that reduces refrigeration consumption an average of 26% while maintaining required temperatures inside low-temperature facilities is Thermal Energy Storage (TES) by Viking Cold Solutions. These TES systems are comprised of phase change materials (PCM), a 24/7 cloud-based monitoring and notification platform, and intelligent controls that balance temperature requirements and refrigeration run time for maximum energy reduction.
The PCM is installed near the top of the room and is frozen using the airflow from the existing refrigeration system. As it transitions between solid and liquid states it becomes 300 times more heat absorbent than the food. As heat rises through natural convection the PCM absorbs 50 per cent to 85 per cent of the heat infiltration and consolidates it directly in the refrigeration airflow for more efficient removal. As it absorbs the heat the PCM releases the energy it has stored in the form of cold. Convection continuously pulls this cold down across the food to maintain stable food temperatures.
Protecting food while reducing energy consumption is the key to safely improving sustainability. Adding the flexibility to decide when this reduction happens during the day is the key to maximising the cost savings.
TES’s 300 times higher rate of heat absorption allows for long periods of time without active refrigeration. By aligning these periods with times that incur higher energy prices, facilities can achieve electricity cost savings of 35 per cent or more. One M&V study found that a 93,000 square foot frozen food warehouse in California was able to maintain temperatures without active refrigeration for 13 hours per day. The combination of improved efficiency and time-of-use flexibility to avoid peak period energy prices continues to save the facility nearly 50% of their annual energy costs.
Customers are requiring greater carbon reduction from their distribution partners. Those that meet customers’ Scope 3 emissions requirements have a competitive advantage and increase the likelihood of keeping and growing their customer base. New technologies like thermal energy storage are critical for supply chain partners to meet these requirements and to lower their own operating costs. Reducing the carbon footprint of frozen food warehouses is a win for the operator, a win for the customer and the end consumer, and a big win for the environment.
For more details, visit:
www.vikingcold.com
Cookie Consent
We use cookies to personalize your experience. By continuing to visit this website you agree to our Terms & Conditions, Privacy Policy and Cookie Policy.
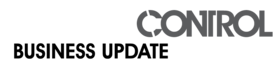