Innovations in automation, eco-friendly refrigeration, and connected technologies are transforming the cold chain industry. The cold chain industry embraces technologies like AI, robotics, and eco-friendly refrigeration to tackle sustainability challenges. By modernising warehouses and optimising operations, the industry aims to reduce waste, enhance energy efficiency, and ensure the safe delivery of temperature-sensitive goods, fostering a more sustainable future.
The cold chain industry expansion in the coming years stands to be driven by factors such as the widespread adoption of connected devices and the automation of refrigerated warehouses worldwide. The cold chain typically starts at the source and continues to the point of consumption, often referred to as ‘farm to fork’ for items like fruits and vegetables. However, there exist challenges in handling perishable items of various kinds. Any perishable product requiring controlled temperature conditions to preserve its freshness needs a refrigerated cold chain throughout its entire supply chain, says Srinivas Reddy, Vice President of Commercial Refrigeration Business at Blue Star Limited. Maintaining a sustainable cold chain is of utmost importance to ensure both the quality and quantity of these products and to prevent significant losses.
Sustainability concerns
It is essential to consider sustainability in light of the significant losses incurred due to disruptions in the cold chain. The production of perishable goods requires substantial resources, including water, soil fertility, human labour, time, capital, and energy. Various reports from analysts indicate that post-harvest losses account for about 30 percent of production. Consider the implications of conserving even 10 percent of these losses regarding sustainability. Consequently, expanding cold chain logistics and warehousing is vital in achieving sustainability. The positive growth observed in warehousing and logistics is a promising indicator.
There are adequate technological developments in refrigeration in cold chain logistics and warehousing to address environmental concerns. These involve the utilisation of eco-friendly refrigerants and highly energy-efficient refrigeration systems.
Temperature-sensitive cold chain
On a global scale, there have been technological advancements in refrigerants that offer refrigeration industry participants the opportunity to embrace environmentally friendly and low-GWP hydrocarbon refrigerants. Several international players have used CO2 as a refrigerant in certain user applications. Paradoxically, there is no ownership of perishables as they progress through the value chain, given that ownership shifts occur at different stages. This situation frequently results in notable losses throughout the entire value chain. All parties along the value chain should recognise the importance of upholding an uninterrupted refrigeration chain. They should coordinate efforts to ensure the secure handling of temperature-sensitive products. Reducing wastage is vital, considering the fundamental requirement to guarantee food security and preserve resources for future generations. This requires the modernisation of warehouses and streamlining of operations.
Automation in warehouses
The emphasis on warehouse management has increased with the rise in global trade and the emergence of e-commerce companies. The increasing international trade has driven companies to adopt cutting-edge technologies to optimise warehouse management. By leveraging technologies like AI, robotics, and data analytics, warehouse management systems can improve efficiency, reduce costs, and improve productivity. Many companies have invested heavily in improving the efficiency and productivity of their distribution centres and storehouse facilities by integrating advanced technologies like AI, ML, and data analytics.
As warehouses grow in size and height to accommodate large-scale operations, smooth operations integration becomes imperative. Repetitive tasks such as point-to-point transfers and the loading/unloading of standardised packages make the deployment of automation essential. This involves the use of ‘automated battery-operated pallet trucks’, autonomous mobile robots (AMRs), robotic palletisers, and packing machines, all of which play critical roles in warehouse operations. Barcode scanners and readers are integrated for material identification.
Approximately 80 percent of cold chain warehouses in India lacked automation, including proper warehouse management systems. According to sources, although WMS usage has started to increase, it is not as widespread as desired, especially compared to the global industry worth around $900 billion. Advancements in warehouse management have been helping businesses to improve their logistical capabilities. The importance of the logistics sector in delivering goods and services has been increasing progressively each year.
The rise of e-commerce platforms in retail, healthcare, consumer goods, and other end-use industries has helped consumers to order different types of goods, thus compelling companies to manage warehouses, inventories, transportation systems, and others. According to Vikas Choudaha, Senior Vice President & Business Head of Godrej Storage Solutions, the warehouses continue to grow in size and height to accommodate large-scale operations. With only 40 percent of current warehousing facilities classified as Grade A, there is a pressing need for sustainable, cutting-edge solutions to improve the quality and efficiency of India’s warehousing industry.
Consumerism is rapidly changing, leading to a need for innovative supply chain strategies and practices. Automation technology is the key to achieving ambitious goals in this regard. He adds the potential and possibilities of automation in intralogistics are enormous. Its adoption could vary from simple conveyor systems to cobots to AI/ML-driven technologies. Intralogistics space will see more companies adopting and investing in these systems/ technologies as they realise the advantages, including increased efficiencies, productivity, accuracy, and cost savings in the long run. While using technology to automate intralogistics offers numerous advantages, integrating these technologies with existing warehouse setups and workflows is the challenge.
Technology adoption in the warehouses
There is a need for improved education among equipment operators. Lack of proper skills can lead to challenges and failures in utilising advanced technologies. Organised market players can access WMS and ASRS technologies, while most of the country’s warehouses remain unorganised. This knowledge gap hinders widespread adoption and leaves many individuals without the necessary expertise. Progressing in advanced technologies requires starting with the basics and obtaining crucial data for training models. Rajat Gupta, Co-founder and CEO of TESSOL, says we have shown a remarkable ability to adapt quickly once we have access to the right technologies. We embrace change and have swiftly adopted temperature monitoring and data sharing in field deployments. Implementation is not a major challenge, but higher-level decision-making remains crucial. Overall, the country has a positive acceptance and willingness to adopt technology.
Warehouse management
Cold chain warehouses in India adhere to standardised rules and guidelines. The infrastructure is not the issue; the challenge lies in shifting mindsets towards accommodating multi-commodity storage and enabling collaboration with evolving trade and e-commerce platforms.
Over the years, businesses have started to pay attention to modernising their warehouse facilities to ensure timely delivery. As a result, companies are developing full-proof strategies to administer godowns and distribution centers. Various studies have shown that warehouse management, which involves supervising and overseeing day-to-day operations, helps companies streamline their business operations. It involves various activities such as receiving finished goods from factory outlets, transporting, storing, inventory administration, packaging, shipping, and many more.
Moreover, certain principles developed by experts in this field control the different tasks involved in godowns. The effective use of space, equipment, and labour is necessary. Secondly, implementing comprehensive control techniques to coordinate orders, inventory stocks, and people working in the facility is important. All the processes involved in this field should be customer-centric and data-driven.
With the growing digitalisation of different services, supply chain management companies have partnered with IT giants to develop specialised applications for managing storerooms and godowns. These solutions, popularly known as warehouse management systems, are primarily deployed to simplify the complexity of logistical operations. Since these platforms use digital and automation technologies, their ability to handle large volumes of goods and products is better than that of conventional tools.
Automation and thermal management
The global cold chain logistics market’s 14 percent CAGR mirrors India’s expected growth of around 14-15 percent. As Indian consumers increasingly demand fresh and frozen foods, TES technologies reduce energy consumption by up to 30 percent and reduce the dependency on diesel-based backup. Reducing last-mile wastage due to temperature non-compliance will be crucial in scaling up cold storage facilities, says Vishnu Sasidharan, VP of Climate Technologies at Pluss Advanced Technologies. This growth will support India’s shift towards healthier eating habits while ensuring food safety and quality in the logistics chain.
He elaborated that as a provider of PCM-based solutions for thermal management, their primary objective is to enhance energy efficiency and promote decarbonisation. While monitoring temperature and electricity usage is essential, other parameters, like tracking the frequency of opening and closing cold warehouses to assess operational efficiency, are worth considering.
The emergence of innovative technologies such as AI and ML, robotics, data analytics, etc., improved the quality of these WMSs significantly. AI tools, for instance, analyse large volumes of data and predict the inbound receipt and outbound delivery patterns. Machine learning algorithms can assist in demand forecasting, resource allocation, route optimisation, etc., to rationalise the processes involved.
In the past few years, automated guided vehicles, collaborative robots, and other systems have transformed warehouse management. These high-tech robotic solutions simplify repetitive tasks like picking, sorting, packaging, etc. Warehouse operators must understand the importance of creating proper temperature-controlled anti-chambers and ensuring dock areas have suitable buffers to prevent product temperature breakage. From the moment of acceptance to storage, maintaining proper temperature conditions is essential. From a technology standpoint, the importance of adopting technology in warehousing and logistics is rising. However, the main barriers to adoption revolve around cost concerns. Further, governmental initiatives to minimise food waste, trade liberalisation efforts, and the expansion of multinational retail chains are expected to stimulate this industry’s growth.
For the future
To summarise, the rising importance of logistics and supply chains in international trade has increased the importance of the warehouse management landscape. Principles aid companies in managing their godown facilities. However, emerging technologies like AI, data analytics, AR, ML, VR, etc., opened new avenues of growth in the sector.
Many companies have invested heavily in improving the efficiency and productivity of their distribution centres and storehouse facilities by integrating advanced technologies like AI, ML, and data analytics. However, integrating advanced technologies such as artificial intelligence, blockchain, and data security solutions predicts the essential need for robust cybersecurity.
The global cold chain market, valued at USD 279.94 billion in 2022, is projected to exhibit a CAGR of 18.6% from 2023 to 2030. The importance of warehouse management and automation has increased with the emergence of online e-commerce companies. However, it is projected that by 2027, over 70 percent of warehouse operations worldwide will be automated, with robotics playing a significant role in tasks like product placement and e-commerce logistics. The extent to which India will catch up with this trend by 2027 remains to be seen, but the future lies in automation.
==========
Vishnu Sasidharan, VP & Business Head, Climate Technologies, Pluss Advanced Technologies
TES technologies reduce energy consumption by up to 30 per cent, reduce the dependency on diesel-based backup, and reduce last-mile-wastage due to temperature non-compliance.
Srinivas Reddy, Vice President, Commercial Refrigeration Business, Blue Star Limited.
An uninterrupted cold chain is of utmost importance to ensure both the quality and quantity of these products and to prevent significant losses.
Vikas Choudaha, Senior Vice President & Business Head, Storage Solutions, Godrej & Boyce Mfg. Co. Ltd.
Automation in intralogistics adoption varies from simple conveyor systems to cobots to AI/ML-driven technologies.
Rajat Gupta, Co-founder and CEO, TESSOL
Higher-level decision-making is crucial as there is a positive acceptance and willingness to adopt technology in the country.
Cookie Consent
We use cookies to personalize your experience. By continuing to visit this website you agree to our Terms & Conditions, Privacy Policy and Cookie Policy.
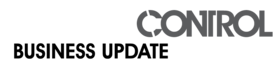