Effective indoor air quality is achieved through filter monitoring, sensor integration, and proper ventilation. In commercial buildings, ventilation systems manage air quality and energy efficiency. Davide Di Dia, CAREL Application Specialist for HVAC Commercial, highlights that these systems balance controlled mechanical ventilation with precise temperature and humidity control to optimise overall performance.
What are the different types of ventilation systems commonly used in commercial buildings?
Ventilation systems in commercial buildings serve two different purposes. The controlled mechanical ventilation (CMV) system manages air exchange if, there is already a primary heating or cooling system. The aim is to guarantee occupant well-being, monitoring and controlling the CO2, PM and VOC levels through dilution with filtered outside air. High concentrations of these three parameters can lead to occupants developing symptoms of sick building syndrome (SBS), including headaches and tiredness. Volatile organic compounds (VOCs) are released by building construction materials, while CO2 gets released via respiration. Particulate matter (PM) involves solid and liquid particles suspended in the air and can originate from inside or outside the building. There is no primary heating and cooling system. The ventilation system also provides temperature and humidity control, in addition to control of the parameters described above. In the latter case, the heart of the system, i.e. the air handling unit (AHU), is more complex and manages higher air flow rates. To control temperature, heat exchangers (rotary or plate) and water, electric or direct expansion coils are used for humidity control, and humidifiers (isothermal or adiabatic) or dehumidification coils are used, depending on specific needs.
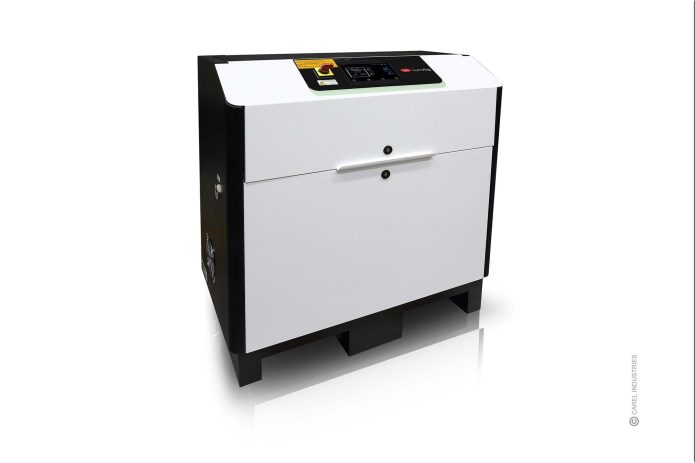
What factors of AHU technologies can improve indoor air quality and energy efficiency?
Correct indoor air quality requires careful monitoring of the filters and robust temperature, humidity, and CO2 sensors. The filters purify the air from the outside, thus avoiding fouling the AHU components. The building’s occupants breathe air with a low solid and liquid pollutant content. The filters accumulate dirt, so their pressure drop increases as they become clogged. Differential pressure switches or differential pressure transducers measure this increased pressure drop, allowing the AHU controller to signal the appropriate time required for maintenance.
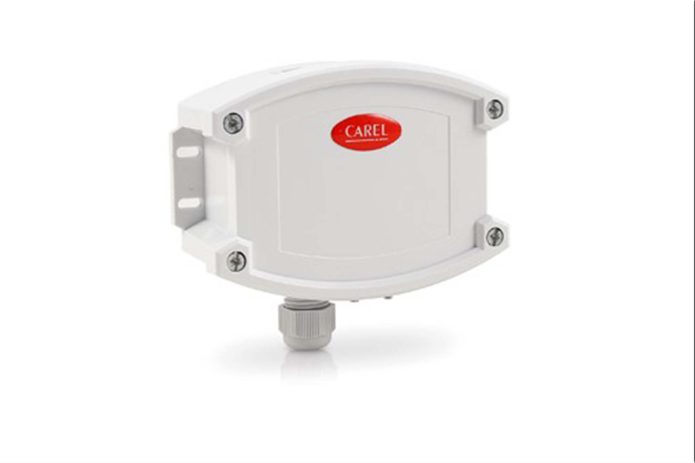
Temperature, humidity, and CO2 sensors have a dual purpose. They are essential for monitoring indoor air quality parameters and ensuring the unit only operates when required (demand-controlled ventilation—DCV).
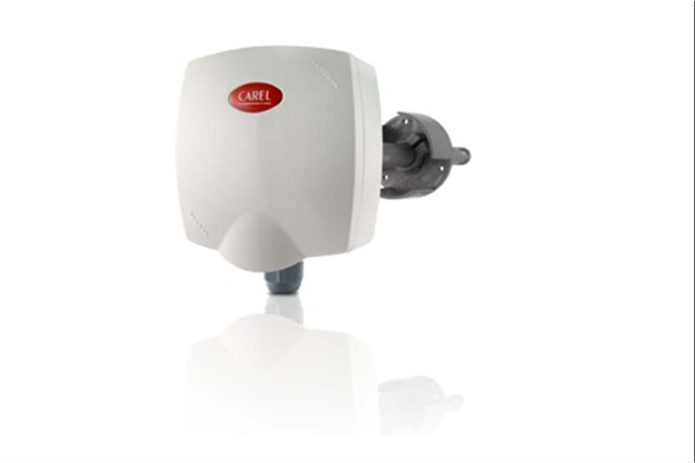
If permitted by the laws in force, air handling units (AHU) increase their energy efficiency through direct expansion rather than water coils. The heat transfer fluid evaporates or condenses directly in the coil placed in the AHU air flow instead of using an intermediate heat exchanger. Energy efficiency increases if the refrigerant circuit has an electronic expansion valve and variable-speed compressor. Both components can adjust the refrigerant flow rate based on system requirements.
How do Smart controls and automation in AHUs enhance the overall functionality of HVAC systems?
Smart parametric controllers, such as CAREL’s k.air, are programmed by expert developers with specific expertise in thermodynamics and automation. Through advanced algorithms for energy efficiency and improved indoor air quality, these activate the various devices on the AHU in sequence, from the least to the most energy-intensive, guaranteeing the desired indoor conditions and improving occupant comfort.
Moreover, they continuously monitor performance and detect problems before failures occur, providing data for energy audits and identifying areas to save energy.
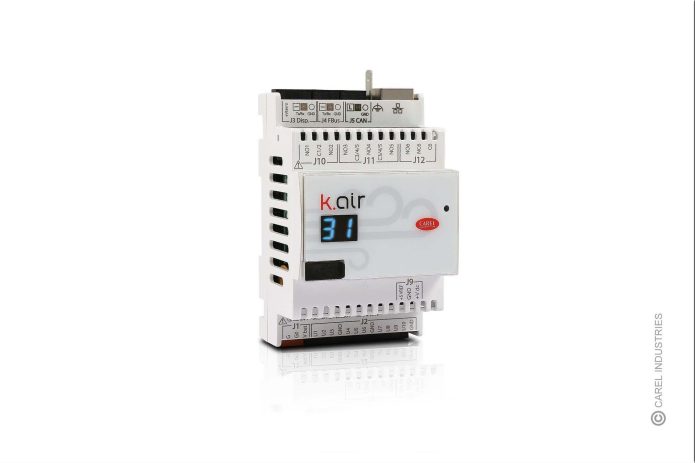
How do you evaluate AHU’s design for implementation in various industries?
Many factors evaluate the design of an air handling unit for various industries. Ensure regulatory compliance with standards such as ASHRAE, ISO, and GMP. Effective temperature and humidity control is essential for maintaining a suitable environment. Airflow efficiency should be optimised to focus on energy efficiency through technologies like modulating systems, inverters, and energy recovery methods.
Operating and maintenance costs should be assessed to ensure long-term affordability. The design should offer flexibility and integration capabilities, including modular design monitoring and supervision systems. Consider the quality of components, material resistance, and ease of maintenance.
Evaluate the environmental impact by looking at sustainability practices and emissions. Lastly, design should be customed to the needs of the industry, whether it’s healthcare, pharmaceuticals, manufacturing, or food production. These factors ensure that the AHU is efficient, compliant and suitable for the specific operating environment.
For AHUs with specific hygiene requirements, such as in healthcare and pharmaceutical applications, HEPA filters, accurate temperature and humidity control, extensive use of stainless steel, and contamination control logic are essential, at times at the expense of energy efficiency.
Efficiency is fundamental for AHUs used in manufacturing industries and painting processes to ensure low energy consumption and emissions. Heat recovery, management of fresh and recirculated air flows, adiabatic humidification, and evaporative Cooling play a crucial role, together with components that are resistant to corrosion and high temperatures and are ATEX certified.
Cookie Consent
We use cookies to personalize your experience. By continuing to visit this website you agree to our Terms & Conditions, Privacy Policy and Cookie Policy.
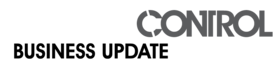