Dr. D.B. Jani, Associate Professor from Government Engineering College, emphasises that the future of advanced pumping technologies in industrial fluid handling is set for innovation, addressing challenges like optimising designs for specific applications, fluid compatibility, and improving sustainability by reducing environmental impacts. Modern pump and valve designs achieved energy efficiency improvements while maintaining high-performance standards.
In industrial fluid handling, the evolution of pumping and valve technologies is a cornerstone for optimising efficiency, reducing energy consumption, better fluid control and enhancing overall system performance.
The latest innovations in advanced pumping and valve technologies have revolutionised how fluids get transported and ensure precision, reliability, and sustainability across various industries. Recent advancements in pump and valve designs have prioritised energy efficiency without compromising performance. Efficiency enhancements contribute significantly to energy savings, making these pumps economically and environmentally beneficial. Variable frequency drives (VFDs) and intelligent control systems further complement these designs by adjusting pump speeds according to demand, resulting in substantial energy conservation.
Pumps for process plants
Pumps may be classified based on the applications they serve, the construction materials, the liquids they handle, and even their orientation in space. A more basic system of pump classification lies in the principle by which energy gets added to the fluid. Under this system, all pump types generally fall into two main categories.
• Dynamic (Centrifugal) Pumps – Energy is added to increase the fluid velocities within the machine.
• Positive Displacement Pumps – Energy is added by force to one or more movable boundaries of enclosed, fluidcontaining volumes. These are further divided into many forms, as shown in Fig.1.

The type of pump selection mainly depends on our requirements. The application includes the type of fluid you desire to pump, the distance to move the fluid, and the quantity you require to get over a particular time frame.
At their most basic level, valves control, regulate, or direct flow within a system or process. They often feature a range of characteristics that help to define their ideal application. However, whether you are looking to control flow or provide safety in a system that is piping liquids, solids, gasses or anything in between, there are likely stainless steel valves available to help.
Valves feature a range of characteristics, standards, and groupings that help to give you an idea of their intended applications and expected performance. Valve designs are one of the most basic ways to sort the valves available and find a good fit for a project or process.
Pumps selection
The selection of the right pump for the flow requirements needs some criteria to follow. The system’s flow rate depends mainly on the system’s physical characteristics, such as friction, static head, and fluid viscosity if the fluid is different from water. The fluids have their characteristics and are pumped under varying conditions. Therefore, ascertain all the pump’s relevant product and performance data before selecting the right one. Some steps are needed to choose the Right pumps.
Firstly, determine the flow rate. In industrial settings, the flow rate depends on the production level of the plant. Careful analysis is required to determine the exact flow rate required. Secondly, determine static and friction head. The static head is determined by measuring the different height levels. The friction head depends on the flow rate, pipe size, and pipe length. Thirdly, sum up the static head and friction head. Finally, select the right pump depending on your required flow rate, static head, and friction head.

Future trends and challenges
The future of advanced pumping technologies in industrial fluid handling is poised for further innovation and integration. Challenges such as optimising pump designs for specific applications, ensuring compatibility with diverse fluids, and addressing sustainability concerns by reducing environmental footprints remain focal points for ongoing research and development.
Virtual reality (VR) is another emerging technology that impacts the pump industry. This technology is used more frequently for pump design and testing. It would allow engineers to create virtual models of proposed pumps and test them under various conditions. Virtual reality could be used for training, such as teaching people how to maintain or operate a particular type of pump. Augmented reality (AR) is similar to VR but involves superimposing computer-generated images onto the real world. AR has much potential in the pump industry as it is used for maintenance and repair. Many pump data can be accessed through AR, such as technical sheets, maintenance records, operational performance, etc. It would allow technicians to see a virtual representation of the pump they are working on, making it easier to identify problems and do repairs. AR could also be utilised for training, such as teaching people how to use new pump models. We expect to see these innovations in the pump industry over the next few years. These advances will impact how pumps are designed, manufactured, and used. Hence, select a pump manufacturer who will incorporate the latest innovations in products and processes and deliver highly advanced pump solutions.
Additive manufacturing advantages and applications: Valves are sophisticated devices used for fluid flow and pressure in hydraulic systems. However, additive manufacturing provides the benefits of design freedom, part consolidation, and efficient manufacturing processes.
Additive manufacturing (AM) enables the creation of intricate internal passages, channels, and fluid flow paths that are challenging or impossible to achieve using traditional manufacturing techniques. AM enhances the performance and efficiency of servo valves by optimising fluid dynamics and reducing pressure losses. It creates lightweight structures by optimising material distribution and removing unnecessary material. It reduces the overall weight of the servo valve, resulting in improved energy efficiency. AM also allows customisation to tailor servo valves to specific applications or system requirements. The flexibility of 3D printing technology enables design modifications, such as varying valve sizes, shapes, and flow characteristics for bespoke purposes.
Valve manufacturers rely on digital technologies to optimise the functionality of control valve positioners. The digitallybacked control valve positioners perform better than traditional electrical or pneumatic valve positioning systems.
In 2023 and beyond, valve manufacturers will explore advanced technologies to optimise the functionality of control valve positioners and provide adequate fluid control mechanisms to meet valve demands as the world transitions to smart manufacturing and Industry 4.0. Intelligent control valve positioners will spur innovation in the valve industry. The demand for device diagnostics means valve manufacturers will increasingly integrate sensor technologies in designing and fabricating control valves and positioners. Hall effect sensors will enhance valve positioner feedback acquisition and improve remote valve diagnosis.
Other technologies dictating the evolution of intelligent control valve positioners include:
Use of energy-efficient central processing units to enhance the autonomy of valve positioners.
• Implement intelligent control systems for performance monitoring, selfdiagnosis and enhanced fail-safe capabilities.
• Equip control valve positioners with fugitive emission and internal valve friction monitoring sensors.
• There is a major focus on improving AI data processing and decision-making capabilities, integrating AI technology in manufacturing process valves, and utilising AI-generated data in control valve design to maximise performance, safety, and durability.
Digital twins and valve reconditioning: Digital twins involve creating virtual (digital) replicas of physical systems, in this case, control valves. Manufacturers combine sensor data and AI-generated analytics to create digital valve replicas and develop simulations to analyse valve performance characteristics. However, plenty of work happens in labs and design centres.
Conclusion
The latest innovations in advanced pumping technologies have significantly transformed industrial fluid handling processes. Energyefficient designs, intelligent systems, sealless technologies, precision pumps, and advancements in materials showcase the strides made toward enhancing efficiency, reliability, and safety in fluid handling applications. As technology evolves, these innovations will continue to shape the landscape of industrial fluid handling, fostering sustainability and operational excellence across industries. Together, a commitment to excellence and sustainability pave the path for a future where fluid control systems reach new heights of efficiency and reliability.
Cookie Consent
We use cookies to personalize your experience. By continuing to visit this website you agree to our Terms & Conditions, Privacy Policy and Cookie Policy.
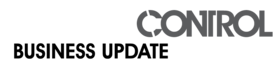