Rahul Juniwal, Founder and owner of Andhra Refrigeration, Hira Industrial Corporation, emphasises that proper maintenance practices are crucial for ensuring the optimal performance of thermal insulation in refrigeration systems. Implementing these practices, from regular inspections to moisture management, ensures optimal energy efficiency and performance over time.
What types of materials are employed in thermal insulation for refrigeration systems?
Materials such as polyurethane, polystyrene, fibreglass, and mineral wool are commonly used in refrigeration systems for their thermal insulation properties. These materials minimise heat transfer, decrease compressor workload, and uphold consistent temperatures. This leads to energy savings by reducing energy consumption and enhancing system efficiency.
How does cold chain management utilise thermal insulation to preserve perishable goods?
In cold chain management, effective thermal insulation is crucial in maintaining constant temperatures across the supply chain. It prevents variations in temperature and preserves perishable goods. Additionally, it guarantees adherence to regulations and sustainability efforts by reducing energy consumption.
How do thermal insulation technology advancements influence refrigeration equipment’s effectiveness in sectors like pharmaceuticals and logistics?
Advances in thermal insulation technology greatly enhance the effectiveness of refrigeration systems used in the pharmaceuticals and logistics sector. These advancements allow for precise temperature management, maintain product quality, and contribute to sustainability by reducing energy consumption and environmental impact throughout the supply chain.
How does insulation contribute to preventing condensation and frost formation in refrigeration systems?
Insulation is crucial in preventing condensation and frost formation within refrigeration systems by creating a barrier between the cold interior and the warmer surroundings. When the surfaces of refrigeration equipment are adequately insulated, they remain at a temperature above the dew point of the surrounding air, reducing the likelihood of condensation forming on the surface.
Condensation and frost formation pose various challenges in refrigeration systems. Excessive moisture can foster the growth of mould, mildew, and bacteria, which can compromise product quality and pose health risks, especially in industries like food and pharmaceuticals. Additionally, frost accumulation on evaporator coils can hinder system efficiency by insulating the coils and impeding heat transfer, ultimately increasing energy consumption.
We can minimise condensation and frost formation by effectively insulating refrigeration systems, thus improving energy efficiency. Effective insulation ensures that refrigeration equipment operates more efficiently by sustaining consistent temperatures and diminishing the need for the system to compensate for heat loss or gain. This results in lower energy consumption and operational costs, making insulation a vital component in optimising the performance of refrigeration systems while preserving product quality and safety.
How do regulatory requirements and industry standards stimulate innovation in thermal insulation materials within the refrigeration sector?
Regulations and standards drive innovation in thermal insulation materials within the refrigeration industry by setting criteria for energy efficiency, environmental considerations, and product safety. Compliance with laws such as the Montreal Protocol and ENERGY STAR fosters the advancement of environmentally friendly and effective insulation materials. Moreover, industry-specific standards set by entities like ASHRAE and ISO further push manufacturers to improve performance and sustainability. This collaboration creates more efficient, sustainable, and compliant insulation materials, benefiting both the industry and global conservation efforts.
Could you elaborate on the maintenance procedures to optimise thermal insulation efficiency within refrigeration systems?
Proper maintenance practices are essential for maximising the effectiveness of thermal insulation in refrigeration systems. Regular inspections should be conducted to detect any signs of damage, wear, or moisture infiltration. Prompt repair of any damaged insulation is necessary to prevent heat leaks and maintain thermal efficiency. This includes sealing gaps, repairing tears or punctures, and replacing deteriorated insulation material.
Moisture management is also essential to prevent moisture-related issues like reduced effectiveness and mould growth. Correct installation of insulation materials helps minimise gaps and thermal bridging, ensuring consistent temperature control. Keep insulation clean and free from debris, dust, and contaminants that can degrade its performance over time. Regular cleaning helps maintain optimal thermal conductivity and extends the lifespan of the insulation.
Implementing a monitoring and testing system helps assess insulation performance regularly. This may involve conducting thermal imaging tests or using temperature sensors to identify areas of heat loss or inadequate insulation. Additionally, maintaining other refrigeration system components, such as doors and seals, complements insulation effectiveness. Properly functioning components help minimise heat transfer and maintain thermal efficiency. Educating personnel on insulation maintenance ensures early identification of potential issues. By implementing these maintenance practices, the thermal insulation in refrigeration systems can be effectively preserved, ensuring optimal energy efficiency and performance over time.
What market trends do you see in the air conditioning sector, considering the rising urbanisation, expanding spaces, and climate change?
Several market trends are influencing the air conditioning sector, including increasing urbanisation, expanding building spaces, and climate change. Due to increasing urban populations and larger building spaces, there is a growing demand for energy-efficient air conditioning systems. Consumers and businesses seek solutions that can provide comfort while minimising energy consumption and environmental impact.
Sustainable cooling solutions are gaining traction, driven by concerns about climate change. This includes using renewable energy sources and developing eco-friendly refrigerants with lower global warming potential. Integrating smart technologies and IoT is reshaping the industry, offering remote monitoring and predictive maintenance features.
As urbanisation increases and cities experience higher temperatures due to the urban heat island effect, there’s a growing need for air conditioning solutions that can effectively cool densely populated areas. This may involve innovative design approaches like district cooling systems or green infrastructure integration.
Stringent regulations and building codes aimed at reducing greenhouse gas emissions and improving indoor air quality influence the design and adoption of air conditioning systems. Manufacturers and suppliers must comply with evolving regulations while delivering high-performance and environmentally friendly solutions.
Overall, the air conditioning industry is evolving to address the challenges posed by urbanisation, building expansion, and climate change. Market trends emphasise energy efficiency, sustainability, connectivity, urban adaptation, and regulatory compliance in shaping the future of air conditioning technology and solutions.
Cookie Consent
We use cookies to personalize your experience. By continuing to visit this website you agree to our Terms & Conditions, Privacy Policy and Cookie Policy.
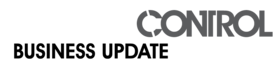