In the changing cooling technology scenario, industries such as food, data centres, and refrigeration are witnessing significant shifts. Innovative approaches are shaping the future of cooling systems, from smart solutions in food storage to the rising prominence of liquid cooling in data centres and advancements in low GWP refrigerants.
What role do smart technologies and automation play in optimising cooling efficiency during supply chain and transportation?
Serena: The core business of the food industry lies in the sale of goods rather than the management or optimisation of cooling systems. These skills are not part of corporate know-how, yet they are becoming a strategic asset. The proper transport and storage of food, coupled with the effective operation of cabinets and air conditioning systems, directly impact business outcomes. To address this, smart technologies and automation can translate unit data into understandable information, making system complexity accessible to those who need to make decisions without necessarily being leading experts in technology.
Proper digitisation of equipment can overcome the challenges posed by this shift. The most critical issue is certainly IT security. Secure data management requires the application of processes and compliance with procedures that are often only understandable to specialists; recent cases in the industry have raised concerns about the risks associated with data security.
Interoperability between different systems is another significant aspect, especially for suppliers like CAREL providing control systems. Quite often, a system comprises units made by different suppliers, and therefore, the possibility of integrating open systems becomes fundamental. Solutions are now available to facilitate information exchange at all levels, from the field to the cloud. Combining data with other information can bring new value, depending on the type of analysis conducted. Establishing a common vocabulary is crucial to giving meaning to collected data and transforming them into valuable information.
The Internet of Things (IoT) simply becomes a means to reduce the energy footprint of the whole chain. Given the vast number of application scenarios, we are confident that the technology is now ready to achieve and probably surpass our goals.
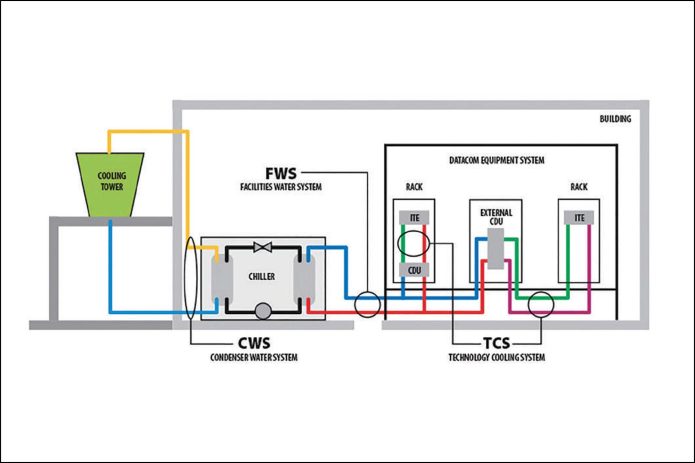
How are liquid cooling systems evolving in the context of data centres?
Enrico: The exponential growth of computing power, coupled with the miniaturisation of components, has resulted in a substantial rise in electrical power density, presenting challenges in heat dissipation. Server racks now receive power up to 100 or even 120 kW, a level once the total for a medium-sized data centre. While such power was previously reserved for specialised applications such as supercomputers for universities, meteorology, and scientific calculation, the exponential growth of AI has led to the widespread deployment of High-Performance and High-Density data centres.
In response to these challenges, ASHRAE expects a growing reliance on liquid cooling, which proves more effective in heat removal than traditional methods (up to 3000 times more efficient, according to Gartner). There are various forms of liquid cooling, which may include either the use of plates inside the chassis that support the servers (often referred to as ILC, indirect liquid cooling), or specific liquid heat exchangers that are in contact with the CPU casing in place of a finned heatsink (DLC, direct liquid cooling) and even immersing the entire server in a tank filled with a dielectric fluid (TLC, total liquid cooling).
As the chip’s temperature is normally around 55-60°C, liquid cooling allows fluids to reach 45-50°C, facilitating cooling through a radiator and outdoor air, leading to substantial energy savings. The achieved temperatures also open the possibility for heat recovery, serving heating needs in winter or supporting industrial processes. This approach aligns with recommendations from EPEE, which proposes including this into a European standard.
What trends are emerging for low GWP refrigerants for cooling perishable commodities?
Miriam: Using natural refrigerants as an alternative to high GWP refrigerants is becoming the most popular choice in refrigeration commodities, which implies the application of new technologies and additional safety measures.
One of the most common natural refrigerants is R-290 (propane). Applications where propane or other hydrocarbons are currently used include commercial, professional and domestic stand-alone units. The major challenge for the use of hydrocarbons as refrigerants is due to their high flammability. This requires a cautious system design and compliance with specific requirements for flammable refrigerants defined by standards. For instance, the last edition of the safety standard IEC 60335-3-89, which should be applied for commercial refrigerating appliances with an incorporated or remote refrigerant unit or compressor, requires using hermetically sealed units when using flammable refrigerants. This requirement underscores the imperative of using sealed units to enhance safety while using flammable refrigerants.
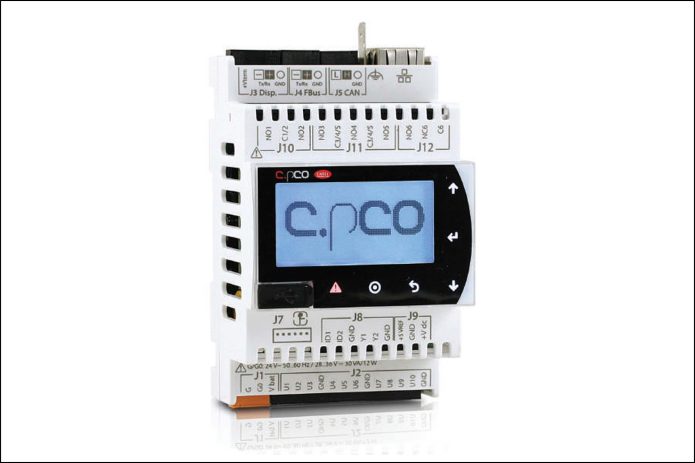
The refrigerant R-744 (CO2) is the preferred option in supermarket systems and is also being utilised in other refrigeration applications such as convenience stores and cold rooms. CO2 has the advantage of being the sole non-flammable natural refrigerant. However, its high operating pressures and the possibility of reaching a transcritical state achievable at not very high temperatures have led to different configurations with new components.
Parallel compression and ejectors are some technologies now being applied to increase the efficiency of transcritical systems. An additional suction line is introduced in parallel compression, improving energy efficiency by directing refrigerant from the receiver directly to compressors in the parallel line, eliminating the need for expansion. Moreover, ejectors leverage the Venturi effect to reduce the compression ratio and the flow rate handled by the compressor. These technologies require the use of an efficient control and supervisory system to optimise the performance of the units.
Cookie Consent
We use cookies to personalize your experience. By continuing to visit this website you agree to our Terms & Conditions, Privacy Policy and Cookie Policy.
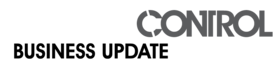