Global supply chain software specialist EPG deployed its innovative Warehouse Management Systems LFS at Schneider Electric’s Sarre- nion warehouse and distribution centre in France.
Schneider Electric looked to Ehrhardt Partner Group (EPG) to install flexible, state-of-the-art Warehouse Management Systems that could match their specific needs more closely. Before the upgrade, the centre’s previous WMS was built on a legacy mainframe, with existing data becoming less reliable.
Responsible for all enclosures and accessories to Schneider Electric’s local distribution centres and third-party suppliers worldwide – the equivalent of 30 trucks per day leaving the site. The reliable and always-on IT and software systems are vital in efficiently running the 10,000 sq. ft. warehouse and distribution centre.
Fast implementation LFS is EPG’s off-the-shelf WMS, customised to intelligently connect the planning and control of all material flow in a logistics facility. It actively guides the movement of all manual and automated storage units with 100 percent safety and transparency, a clear advantage over rival systems. Implementation of the project was trouble-free and required no downtime at Sarre-Union. The process took 18 months, and the EPG team worked closely with Schneider Electric teams with initial workshops and project specifications to prepare for the customisation, tests and deployment.
Performance result Since implementing LFS, the centre has experienced significant improvements to its processes, including a 15 percent uplift in logistics capacity. In just three months, the centre outperformed previous benchmarks and boosted capacity by 15 percent.
Department Operations Manager Kevin Cartolano confirmed, “All configurations are controlled by our key users, who can manage the jobs, change the flows and processes all by ourselves. The label management facility enables us to print directly via LFS. The benefits include no fixed batch jobs and no downtime needed to integrate new orders. Meanwhile, the printer management function permits key users nominated by us to manage individual printers.”
Schneider Electric managers and staff were also impressed with the system’s easy-to-use interface. This makes it more comfortable for relevant teams to adopt, mainly as it is flexible enough to be used on several platforms as required throughout the facility, such as tablets, handheld units, laptops and desktop computers. “Schneider Electric is delighted with the flexibility benefits provided by the multiple functionalities incorporated within the customised LFS,” Kevin Cartolano shared. The quality and speed of communication provided by EPG’s versatile and expert support personnel have been commendable, and we look forward to working with EPG on many future upgrading projects.
As a company with almost 200 years of history in sustainable innovation, Schneider Electric is a leader in the digital transformation of energy management and automation and the provider of electrical distribution equipment and secure energy equipment for homes, buildings, data centres, infrastructure, and industry.
Cookie Consent
We use cookies to personalize your experience. By continuing to visit this website you agree to our Terms & Conditions, Privacy Policy and Cookie Policy.
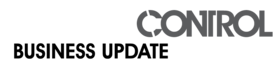