Count on environmental impact assessment, sustainable habitat, energy labelling and ECBC codes while selecting a new chiller. There is a massive requirement for chillers’ way forward, and there is a huge future for the chiller.
A chiller is a machine that removes heat from a liquid coolant via a vapour-compression, adsorption or absorption refrigeration cycle. This liquid can then be circulated through a heat exchanger to cool equipment or another process stream (such as air or water). Adsorption refrigeration also includes a generation process where refrigerant vapour molecules desorb from the solid. In this process, there is no use of CFCs or ammonia. The thermally driven cooling process is environmentally friendly. As a necessary by-product, refrigeration creates waste heat that must be exhausted for greater efficiency or recovered for heating purposes.
Vapour compression chillers may use any of the ‘numbers of different types of compressors. Today’s most common chillers are the hermetic scroll, semi-hermetic screw, or centrifugal compressors. The condensing side of the chiller can be either air or water-cooled. Even when liquid is cooled, the chiller is often cooled by an induced or forced draft cooling tower. Absorption and adsorption chillers require a heat source to function. Chilled water is used to cool and dehumidify air in mid to large-size commercial, industrial, and institutional facilities. Water or liquid chillers can be liquid-cooled, air-cooled or evaporative-cooled. Water or liquid-cooled systems can provide efficiency and environmental impact advantages over air-cooled systems.
Chillers type
Chillers, in general, are divided into two categories: vapour compression and absorption. In vapour compression, the most popular part includes reciprocating, centrifugal screws and scroll chillers. Vapour absorption chillers are becoming more popular lately because of the adoption and usage of green refrigerant gases. These are relevant for today’s world of the heating and cooling cycle.
Applications
Applications of chillers are typically in spaces where heating and cooling are required. Water-cooled chillers usually sit in the plant rooms, and the air-cooled chillers sit over the buildings. The water-cooled chillers are associated with cooling towers and pumping systems. However, air-cooled chillers are a more independent type of system. When we talk about the application of chillers, today, chillers are required in buildings, air conditioning, commercial projects, hospitals, hospitalities, marine application processes, low-temperature plastic industry, industrial refrigeration projects, mining, shipping and more. So, chillers cover a significant part of the application scenario.
Earlier chillers ought to be a luxury, but now they have become necessary. There has been a lot of demand for chillers over the years. Building construction is also projected to increase rapidly. HVAC systems contribute to about 31 percent of energy use. There is an increase in demand for air conditioning. It is rising in all applications – residential, office, retail or hospitality. In every city, there is an increase in demand per se for air conditioning; hence, chillers are warranted. More or so, the institutional frameworks to be followed are – decarbonisation and energy-efficient units.
The following should be kept in mind while selecting any chiller for its application: the ECBC code, environmental impact assessment, sustainable habitat, mission, energy labelling, city regulation and green building association.
Is VRV or VRF a threat to the chiller?
It is said that any technology is good if applied correctly. So, no technology becomes a threat to each other. It depends upon the designer how to design the building and put it in application mode. The chillers are tried, tested and trusted products with a stable market but face challenges from new technologies.
The scroll compressor with and without VFD or inverter, air-cooled condenser, DX evaporator electronic expansion valve and in-built pump are part of any chiller model. We are ahead in applied sciences by comparing this to a VRV/ VRF while it is designed, operated, installed or commissioned; the equipment’s safety and adaptability are to be ascertained. Also, whether that machine carries certification or not and the lifecycle cost of equipment is to be considered. So when we talk about any design, compare a chiller with the VRV: the fundamental difference between a chiller and a VRV is that chilled water is running in the entire space. However, in VRF, the refrigerant is running in this space. So, we have to decide what is most comfortable for the application. The design of the system must be on the base of site requirements. The viewpoint should aim at better solutions for the client’s needs and demands. The designing of the system should be done by considering site conditions and their constraints.
Installation
The installation of the chiller will support any length of chilled water piping because it has to be enhanced by pumping. The chilled water can reach any specified length. The elevation difference and the length between indoor and outdoor units are insignificant in the chillers. The system installation should be easy for the contractor avoiding complications for the end user.
Hence, when we are just deciding what has to be applied – see the demand, see the application and see how it has to be used better. The chiller’s maintenance is easy because most people are accustomed to it. The OPEX and the CAPEX of the chillers can be justified when thinking about owning a chiller. When the life of the equipment is concerned, there is a difference only in the refrigerant running inside the spaces.
The chiller as a technology can give a by-product in the name of the superheater, which can produce hot water and the domestic hot water requirements. So, this is an added advantage one gets through chillers regarding any leakages at the site. It can be easily maintained and does not affect many indoor units per se. In indoor air quality, chillers have inherent benefits by providing fresh air indoors and hence are most preferable in India today.
Certifications
Regarding chillers’ certifications, authorities like Eurovent and Indian certification authorities have made a lot of efforts. The certification ensures that chillers are recognised or certified in a manner that the users can take advantage of. Also, the user can understand how these are certified, thus enabling them to make intelligent choices. Eurovent is Europe’s Industry Association for Indoor Climate (HVAC), Process Cooling, and Food Cold Chain Technologies.
In future, the chillers can be installed in Greenfield projects, retrofit projects and reconstruction of buildings. They should be installed on new buildings that are coming up, the latest industrial developments and the food processing industry. The Emergence of Smart cities and Airports in B-class cities has also influenced the increase in demand for chillers.
Future of chiller
The centrifugal compressors came in 1922, screw compressors came in 1967, and compressors with VFD prototypes came in 1979. Magnetic or oil-free compressors with minor efficiency enhancement in the last 50 years have attracted massive demand. The heat exchangers’ improvement expansion devices have improved from thermal to electric motor efficiencies. Improved economisers have been added to the compressors. Compressor manufacturing has been seeing refinement and advancement in a significant way. “There is a huge requirement of chillers’ way forward, and there is a huge future for chillers’ way forward”, asserts Kshama Jain.
Cookie Consent
We use cookies to personalize your experience. By continuing to visit this website you agree to our Terms & Conditions, Privacy Policy and Cookie Policy.
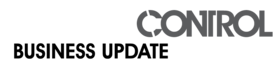