Digitalisation will play a big role in boiler operation, inspection, safety, etc.; IoT can also identify boiler performance variations and suggest required tuning parameters changes to achieve optimal performance.
Thermax is an Indian multinational company working in energy and environment, focusing on providing solutions for clean air, clean energy, and clean water. Thermax started its journey as a manufacturer of small boilers in 1966 as Wanson India Pvt. Ltd. Slowly, it has expanded in other areas of energy and environmental solutions. Currently, Thermax manufactures products and offers solutions in the process of heating, large capacity boilers & heaters, waste heat recovery, absorption chiller, wastewater solution, environmental solution, speciality chemicals and power generation.
Design considerations are essential for boiler safety The typical failure modes of the boiler are thermal stress, circulation, overheating, corrosion, and erosion. Design considerations for boiler safety vary with the design of the boiler. In a firetube boiler, thermal stress, overheating, tube plate cracking, and furnace failure due to lower water levels are some common problems. Flexibility plays a vital role in designing a fire tube boiler, as it helps reduce thermal stress and stress concentration in the boiler. It is achieved using a corrugated furnace, suitable breathing space, and a flexible tube plate design. The role of fuel is also quite important, as the gaseous fuel has less heat transfer in the furnace due to non-luminous radiation in comparison to the luminous radiation of the fuel oil. It reduces heat flux in the furnace but increases furnace exit temperature and can cause overheating of the tubeplate and tube plate cracking. Entry velocity and ligament play a very important role in tube plate cracking. This is essential for fuel change planning and retrofitting the gas burner. In a water tube boiler, natural circulation ratio, heat flux and water quality play quite a significant role in boiler safety. Erosion is another critical failure mode of the boiler and is the function of relative hardness, angle of incidence and flue gas velocity. The boiler design should be carefully reviewed to eliminate the possibility of corrosion in different operating conditions.
Technology developments for boiler inspection and safety practices
Digitalisation will play a big role in boiler operation, inspection, safety, and performance optimisation. This will help to identify the health of the various components, corrosion & erosion of the heat transfer surfaces, and slagging and fouling of the boiler. Thermography will play an important role in identifying the hot spots and the possibility of failure due to overheating. Online identification of corrosion and tube thickness will play a significant role in minimising boiler downtime and minimising production loss. Techniques like EMAT and RFET will help in the boiler audit for the safe operation of the boiler. Digitalisation will also help maximise boiler efficiency and reduce running costs.
IoT helps in optimising boiler efficiency and advance maintenance alerts
Variability is the key to boiler operation. It can encounter changes in fuel characteristics, ambient conditions, heat transfer performance due to slagging and fouling, the boiler components’ health, and refractory health. All these changes affect the boiler’s performance, efficiency, emission, and life. IoT can identify these changes in the runtime, determine the impact of these variations on the boiler performance and suggest the required changes in tuning parameters to achieve optimal performance and longer boiler life. It can benchmark the current performance against the design parameters to identify the gap and helps the user reduce the gap to operate the boiler efficiently. It can monitor the changes in tuning parameters and conduct the impact analysis to allow the user to finetune the boiler. It can help the user identify the critical components’ health status and assist in predictive maintenance planning and spare part management.
Efficiency rating system for boilers:
Currently, India does not have a rating system for boilers. However, the Bureau of Energy Efficiency is working with boiler manufacturers to develop an appropriate rating system for the boiler.
Evolving technologies for the waste heat recovery boilers
The major area of the development of the waste heat recovery boiler is the development of the process specific heat recovery solution. Low temperature heat recovery is the key to developing process-specific heat recovery solutions. Some significant challenges in waste heat recovery boiler technology are fouling and corrosion of heat transfer surfaces due to flue gas contaminants. Low cost corrosion resistance material development and economical waste gas cleaning will play a vital role in developing waste heat recovery boilers.
Future of the boiler industry in India Efficiency, emission, fuel flexibility and the use of renewable energy are the key drivers for boiler development. Biomass gasification and combustion will play a major role in heating. Developing a hybrid boiler with different energy sources like solar, geothermal, electrical and biomass will be critical for process heating applications. Smart automation with model-based control, data analytics, machine learning, and artificial intelligence will play a significant role in future energy generation and utilisation. The development of zero-emission combustion technologies like unmixed combustion, chemical looping combustion, and oxyfuel combustion will be critical for the future of the boiler business.
Cookie Consent
We use cookies to personalize your experience. By continuing to visit this website you agree to our Terms & Conditions, Privacy Policy and Cookie Policy.
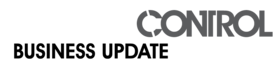