Processes requiring a pressure dew point between 3°C and 6°C employ refrigeration dryer to dry the compressed air by cooling down the air to nearly freezing point.
The power industry is heavily dependent on the quality compressed air for the intricate operations involved in the industry. It finds application in diverse jobs ranging from coal handling, ash conveying systems, and assuring the smooth functioning of pneumatic instruments required for powering the tools that start the gas turbines, boilers, generators, precipitators, etc., insertion and withdrawal of reactor rods, and stamping.
Considering that compressed air powered pneumatic machines are essential, it is highly imperative to closely monitor the quality of the compressed air and ensure that there are no traces of contaminants in the form of moisture/water, oil fumes, dust particles, or any form of solid contaminants.
As moisture is a source of menace across the industries, similarly in the power industry it can exceedingly intervene with the Pneumatic Ash Conveying System. Compressed air is responsible for conveying the bulk material from one point to another including the several discharge points through the Pressure Conveying System. Here majorly dry fly ash is transported from the surge hopper to the silo for storage. Considering that ash is highly susceptible to water, even the slightest presence of moisture in the compressed air can moisten the ash and give it a sticky consistency and block the conveying pipeline by scale formation. This acutely disrupts the free flow of the ash. Along with this, there is also a high chance of contamination at the point where the compressed air comes in direct contact with the hygroscopic material.
If the issue of moisture in compressed air is left unattended then it can lead to damage of the pneumatic tools and machines. Moisture increases the probability of corrosion in the pipelines, cylinders, and other components. During cold weather, the issue is further compounded when freezing occurs in the exposed lines. All these factors are cumulatively responsible for the sluggish and inconsistent functioning of valves and cylinders. This results in increased downtime of the machine which invariably puts a lot of pressure on the company to increase the maintenance cost of the pneumatic machines.
Therefore, in order to address the problem, it is highly imperative to ensure the supply of dry compressed air free from contamination of water, dust particles, oil, or solid contaminants. To achieve this, power plants must install compressed air dryers to attain the highest quality of compressed air. Delair offers Compressed Air Treatment solutions that save the production and energy costs of the company. There is a wide range of refrigeration and desiccant/adsorption dryers that makes use of different drying principles but give the same desired outcome of eliminating moisture from the compressed air.
Processes requiring a pressure dew point between 3°C and 6°C employ refrigeration dryer to dry the compressed air by cooling down the air to nearly freezing point. The processes for which extra dry air is needed ranging between atmospheric dew points of -40°C and -60°C make use of adsorption or desiccant drying. It works on the principle of heatless regeneration that makes use of desiccants to adsorb and desorb the water vapor.
In a way, quality compressed air can avoid any instances of power plant shutdown or temporary discontinuity of the operations occurring due to the malfunctioning of the machinery and save the company from the huge revenue loss.
Cookie Consent
We use cookies to personalize your experience. By continuing to visit this website you agree to our Terms & Conditions, Privacy Policy and Cookie Policy.
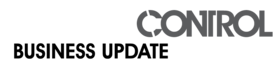