This article outlines the various means in which cold chain products can be transported, including refrigerated trucks and railcars, refrigerated cargo ships, reefers and air cargo.
While globalisation has made the relative distance between regions of the world much smaller, the physical separation of these same regions is still a very important reality. The greater the physical separation, the more likely freight can be damaged in one of the complex transport operations involved. Some goods can be damaged by shocks, while undue temperature variations can damage others. For a range of goods labelled as perishables, particularly food (produces), their quality degrades with time since they maintain chemical reactions, which rate can be mostly mitigated with lower temperatures. It takes time and coordination to move a shipment efficiently, and every delay can have negative consequences, notably if this cargo is perishable. To ensure that cargo does not become damaged or compromised throughout this process, businesses in the pharmaceutical, medical and food industries are increasingly relying on the cold chain.
While the idea of transportation is a relatively new concept, the transport of temperature-sensitive products really dates back to the late 1700s, when ice was used by the British to keep fish from spoiling. Late 1800s, it was used to transport perishables as well. Dairy products were transported from rural to urban areas to be sold, and due to a European meat production shortage, South America was sending frozen meat to France and Australia, while New Zealand was sending it to Great Britain. Cold chain tech has always been, and will continue to be, hugely important to global trade.
Moving freight that requires temperature control involves multiple moving parts to work seamlessly. The normal process of moving freight is simple – plan the route, load the container, move the product, and deliver to the customer. When products require temperature controls like reefer or frozen shipments, each phase of shipping involves multiple additional steps.
Planning: When a cold storage shipment is planned, the shipper and carrier must work together to ensure they have the right equipment to transport the goods to its destination. The biggest hurdles exist with international shipping, where in most cases, the products being shipped will require movement to different containers. Carriers must also ensure their shipments comply with food safety standards, to reduce the growth of bacteria, spoilage, and ensure the product is delivered on time.
Loading: Most LTL carriers maintain cold-storage depots that permit them to keep products within their ‘danger-zone’ of temperature tolerance. Once the shipment is ready for movement, carriers must work quickly to load cargo onto temperature-controlled containers.
Movement of Freight: The cold supply chain needs to move efficiently. While today’s cargo containers are built better than ever, it’s still a reality that the longer cold storage products are on the road, the more opportunity for damage to the freight exists. Shippers and carriers also need to work closely with the recipient to ensure they are available for deliveries to reduce shipping delays.
When a cold storage commodity is moved through the supply chain, failures to maintain temperature-control can impact public health. Specifically, there are two areas where cold supply chain shipments can cause harm to the general public if not correctly controlled.
Medical Products: Every year, pharmaceutical companies develop medication and vaccines that require storage at certain temperatures in order to maintain their effectiveness. Some of these products include life-saving produces like insulin for diabetics, vaccines, and antibiotics for serious infections.
Food Products: Perishable products like produce, dairy, meat, and frozen foods make up 25% of the total supply chain across the globe. Keeping these products within their ‘danger-zone’ of temperature storage helps to reduce the growth or spread of bacteria. Most food-borne illness issues you hear about on the news are caused by lapses or mistakes within the supply chain.
While moving products from one location to another is a relatively straightforward process, the cold supply chain simply has more moving parts. The biggest issue that new cold-commodity shippers deal with is understanding the excessive regulations and control involved in this segment.
Cold chain logistics has many moving parts. Some of the elements (Fig. 1) include:
Cold storage: Facilities that store goods and products waiting to be transported.
Cooling systems: Systems that brin g food up to and keep it at an appropriate temperature during all aspects of the supply chain, including processing, storing and transporting.
Cold transport: Ensures goods remain at stable temperature and humidity levels.
Cold processing: Facilities that allow for processing goods with sanitation in mind.
Cold distribution: Deals with loading boxes or crates and pallets to distribute goods.
From an economic development perspective, the cold chain enables many developing economies to take part in the global perishable products market either as producers or as consumers. The growth in income is associated with a higher propensity to consume fruits, vegetables, fish and meat products. Increasing income levels are associated with a change in diet with, among others, growing demand for fresh fruit and higher value foodstuffs such as meat and fish. People with higher socioeconomic status are more likely to consume vegetables and fruit, particularly fresh, not only in higher quantities but also in greater variety. Consumers with increasing purchase power have become preoccupied with healthy eating. Therefore producers and retailers have responded with an array of exotic fresh fruits originating from around the world.
The packaging industry is constantly evolving in order to cater to the demanding needs of cold chain logistics. Companies are looking for packaging with better insulation material and pallets that are significantly more resistant to damage during transport. Several industries are embracing eco-friendly packaging solutions and are turning towards reusable containers to reduce waste.
From a geographical perspective, the cold chain has the following impacts:
Global. Specialisation of agricultural functions permitting the transport of temperature-sensitive food products to distant markets. It enables the distribution of vaccines and other pharmaceutical or biological products from single large facilities to any market around the world.
Regional. It can support the specialisation of production and economies of scale in distribution. This could involve large cold storage facilities servicing regional grocery markets or specialised laboratories exchanging temperature sensitive components.
Local. Timely distribution to the final consumer of perishables, namely grocery stores, and restaurants.
Cold Chain Technologies
Cold chain transportation relies on several methods to keep goods at proper temperatures (Fig. 2). How long the transport is, the size of the packaged shipment and seasonality are all factors that affect which method is used.
Gel packs – Often used for medical and pharmaceutical shipments.
Dry ice – Can keep goods frozen for extended time periods. Used for dangerous goods, pharmaceuticals and food. Sublimates rather than melts when coming in contact with air.
Liquid nitrogen – Used primarily to transport biological cargo (organs, tissues).Extremely cold, keeps items frozen for longer periods.
Eutectic plates – Also called cold plates, similar to gel packs but can be reused.
Reefers – A temperature-controlled, insulated van, semi, truck or standard ISO container. Allows for temperature-controlled air circulation.
Quilts – Insulated quilts can be wrapped around or placed over freight and are used to keep temperatures constant, so frozen items will remain frozen for a longer time.
Operational Conditions of Cold Chain Logistics
Three operational conditions (processes) are fundamental (Fig. 3) in a cold chain:
Conditional demand: The demand of a product at a market (or place of consumption) is conditional to its qualitative attributes. Each product has a specific level of perishability. For some products, such as vaccines, value (and demand) drops to zero if the shipment has been slightly damaged since the product can no longer be used. Other products, such as produces (fruits & vegetables), see a decline of their value in relation to the level of spoilage that took place during transit, since it will limit their shelf life and as such their commercial potential.
Load integrity: Relates to the load conditions that must be provided to ensure that a product keeps its value during transport. It can include adequate packaging and packing, as well as the conditioning that the product must go through before transport (being washed or cooled down). The reefer has become a common temperature-controlled transport unit used to insure load integrity since it can accommodate a wide range of temperature settings and accordingly a wide range of temperature sensitive products. However, using reefers and many other refrigerated modes of transportation is facing the empty backhaul problem as the majority of refrigerated trades do not have a return equivalent.
Transport integrity: The series of tasks and safeguards that must be performed to ensure that the temperature controlled environment remains constant. A breach integrity can take place during transport, at terminals and distribution centers involved in the transport chain. For instance, the temperature of a shipment is often constantly tracked so that deviations can be mediated as soon as possible. An outcome of more stringent requirements in transport integrity has been the setting of specialised modes and terminal facilities designed to support cold chain logistics.
Common Cold Chain Management Issues
The fact that cold chain logistics uses a wide range of refrigerants and consumes too much energy for storing temperature-sensitive products makes it a challenging environment for becoming sustainable. Innovative solutions are necessary to strike the right balance between the energy-intensive processes of cold chain logistics and addressing the various environmental issues that are starting to impact everyday life.
Cold supply chain companies face the challenge of ensuring the quality and safety of temperature-sensitive products during shipping and distribution. These perishable goods are tested in a variety of environmental conditions that recreate different physical situations. This iteration process is used to fine-tune and optimise conditions that are traditionally cost and energy-intensive. Computer simulations are a solution for testing solutions faster at lower costs.
Common cold supply chain management issues can have a real impact on freight shipments. Drivers are typically very cognizant of these potential problems and will do their best to keep on top of them to prevent issues from arising in the first place.
Product quality issues: For food items and produce, quality can be an issue from the start. Proper sanitising, cleaning and sorting must be done prior to packaging and loading.
Inadequate packaging: Important to prevent contamination and transport-related damage. Air flow can also be an issue.
Lack of proper documentation: All steps of cold supply chain management need to be well-documented. This is especially true during transit, where data loggers that record storage temperatures and conditions can help prevent inadequate conditions from spoiling a load.
Shipment/transport delays: Delays are an obvious issue for any shipper, but they can be particularly detrimental when dealing with cold chain logistics, since cold chain technology is time-sensitive.
Disrupted climate control and/or temperatures: Temperature variation can be a big problem in cold chain logistics. It can result from multiple deliveries (meaning doors opening and closing often), loading food from the field, improper pre-cooling, extreme weather or other conditions like faulty cooling devices or transports.
Monitoring the condition of temperature-sensitive products being shipped across significant distances is crucial for many businesses if they are to avoid unnecessary losses. Monitoring the temperature of products while they are in transit allows for improved quality and safety in industries like agriculture, food and pharma. The rising demand for real-time temperature monitoring and location tracking has given rise to many innovative startups working on cold chain solutions. In recent years, partly as a result of the huge increase in pharmaceuticals that are sensitive to temperature change, there’s been a clear shift towards standardising global transportation regulations for healthcare-related products.
Authored by
Dr. D.B. Jani
Government Engineering College, Dahod,
Gujarat Technological University – GTU, Ahmedabad, Gujarat
Cookie Consent
We use cookies to personalize your experience. By continuing to visit this website you agree to our Terms & Conditions, Privacy Policy and Cookie Policy.
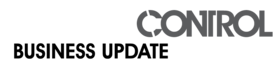